Druk 3D w motoryzacji: Ekonomiczna reprodukcja zabytkowego skutera
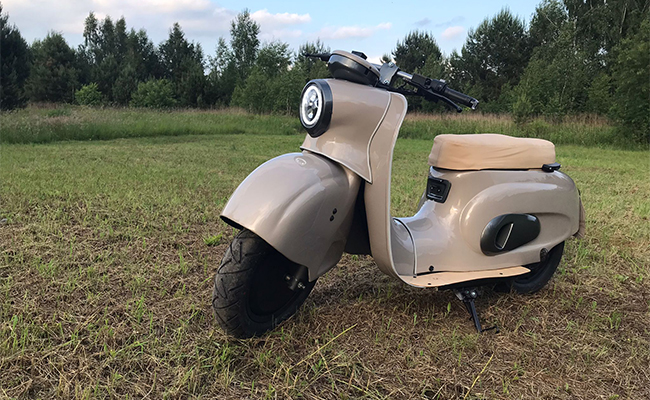
Falectra to firma motoryzacyjna założona przez Piotra Krzyczkowskiego, która zdobyła rozpoznawalność w branży motoryzacyjnej dzięki zbudowaniu pierwszego polskiego motocykla elektrycznego. Marka zajmuje się również reprodukcją pojazdów, a ostatnio stworzyła klasyczny skuter o nazwie Be-e, oparty na WFM M50, polskim motocyklu z lat 60-tych. Druk 3D od samego początku odgrywa znaczącą rolę w działalności Falectry. Nie inaczej było w przypadku projektu Be-e. Do odtworzenia zabytkowego skutera firma wykorzystała desktopowe drukarki 3D Zortrax M200 Plus, Zortrax Inventure i Zortrax M300 Plus.
Projektowanie części 3D dla motoryzacji: rekonstrukcja klasycznego skutera
Pomysł na projekt skutera Be-e pojawił się równolegle z pracami nad elektrycznym motocyklem “Falectra” oraz podczas współpracy ze studiem 911 Garage nad serią Porsche “Remastered”, będącą wariacją na temat klasycznych modeli 911 z nowoczesnymi detalami. Kiedy z przyczyn niezależnych od firmy prace nad Falectrą stanęły w miejscu, na pierwszy plan wysunął się Be-e. Ponieważ panuje coraz większa moda na restomody, Krzyczkowski spodziewał się, że taki projekt przyciągnie uwagę miłośników motoryzacji. Wiedział też, że chce oprzeć swój nowy skuter na flagowym modelu WFM z lat 60. i wykorzystać do tego celu swoją ulubioną technologię wytwarzania addytywnego. Jedyną kwestią, która go zastanawiała, była nazwa projektu. Projektant chciał, aby kojarzyła się ona z oryginalnym modelem, a także odzwierciedlała to, w czym specjalizuje się firma. “Be-e” wydawało się być idealnym wyborem: “Vespa to po łacinie osa, bee to po angielsku pszczoła, a Be-e, w naszym przypadku, jest rozwinięciem hasła “Be electric” – wyjaśnia Piotr Krzyczkowski, założyciel Falectry. Jak dokładnie wyglądał proces twórczy w przypadku tego skutera?
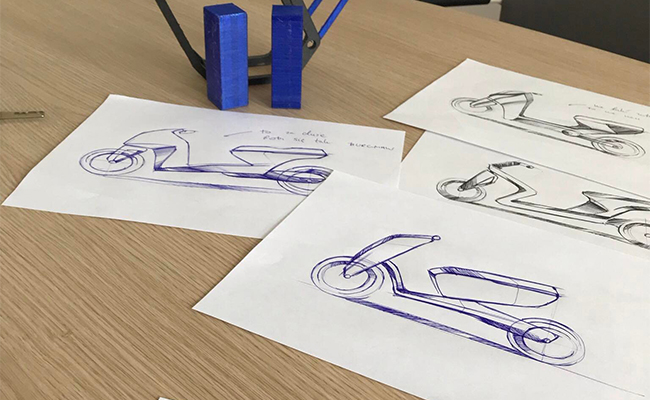
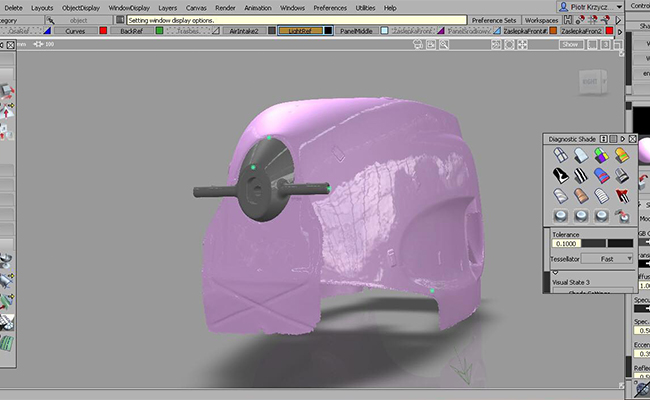
Etap 1: Szkicowanie części i tworzenie modeli CAD
Najpierw Piotr naszkicował całą bryłę skutera. “Postanowiliśmy zainspirować się oryginalną bryłą, ale ją uprościć – pozbywając się elementów, które niepotrzebnie obciążały ogólną formę” – mówi Piotr Krzyczkowski. Następnie, po przygotowaniu pierwszych szkiców poszczególnych elementów, zaczęły powstawać pierwsze wizualizacje – projektant zdecydował wówczas m.in. o tym, jakie detale zaimplementować, czego brakuje w ramie, czy gdzie konkretnie wprowadzić elementy funkcjonalne, np. tylne oświetlenie. Twórca korzystał z oprogramowania CAD Autodesk Alias.
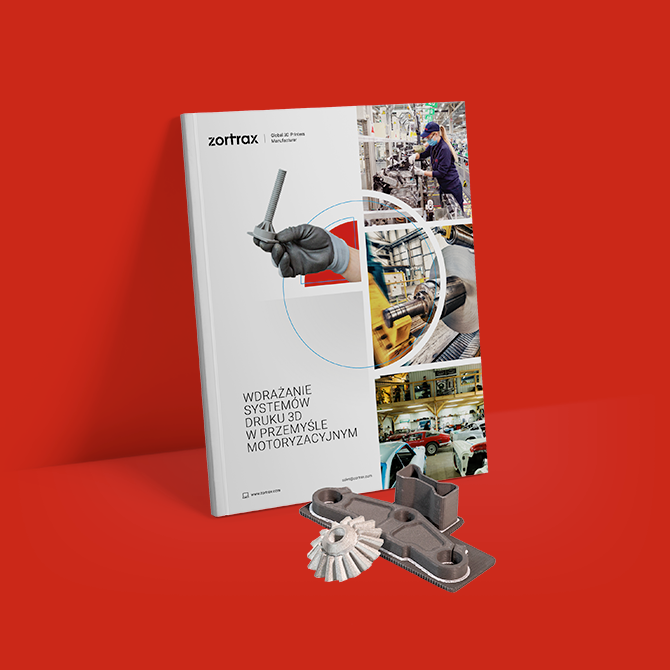
Discover 3D printing solutions for automotive
Download free ebookEtap 2: Skanowanie 3D i druk 3D części funkcjonalnych
Po naszkicowaniu ostatecznej ramy, Piotr przystąpił do budowy prototypu; zewnętrzne panele całego korpusu zostały wykonane z laminatu, a następnie, po dopasowaniu do ramy, całość została zeskanowana w 3D. Dzięki pierwszemu prototypowi Falectra mogła wykonać precyzyjne elementy w technologii druku 3D. Po przygotowaniu modeli do druku 3D w programie Z-SUITE przy zastosowaniu ustawień wysokiej jakości druku i 30% wypełnienia, rozpoczął się proces druku 3D. “Wszystkie elementy zewnętrzne, takie jak obudowy lamp, płetwy przedniego błotnika, obudowę wyświetlacza wykonaliśmy na Zortrax M200 Plus. W przypadku Zortrax M300 Plus, ze względu na duży obszar roboczy drukarki, mogliśmy wykonać większe elementy, jak wloty bloków. Breloczki czy figurki w kształcie skuterów z kolei były wykonywane na Zortrax Inventure” – podkreśla właściciel Falectry. Materiałem wybranym do wykonania docelowych części był Z-PETG w kolorze Grey.
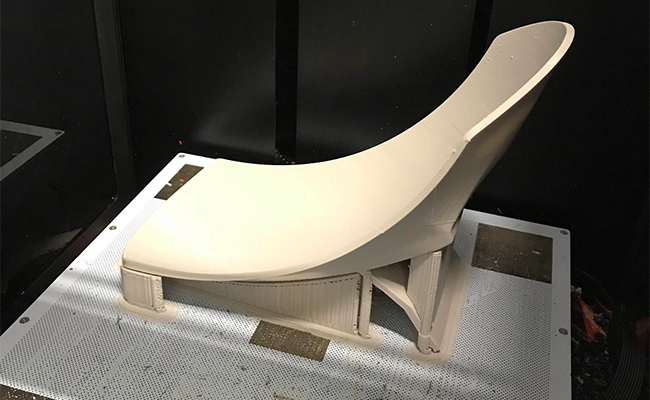
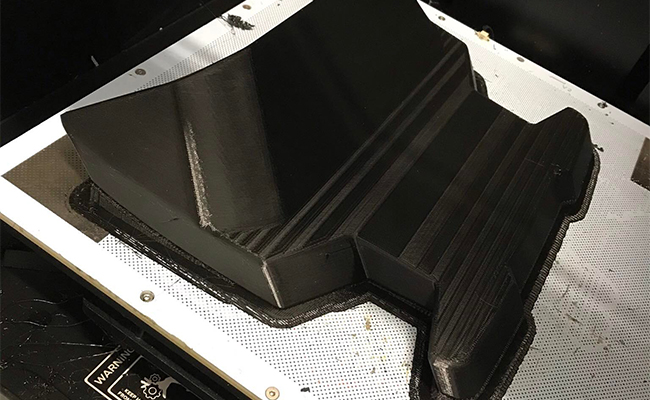
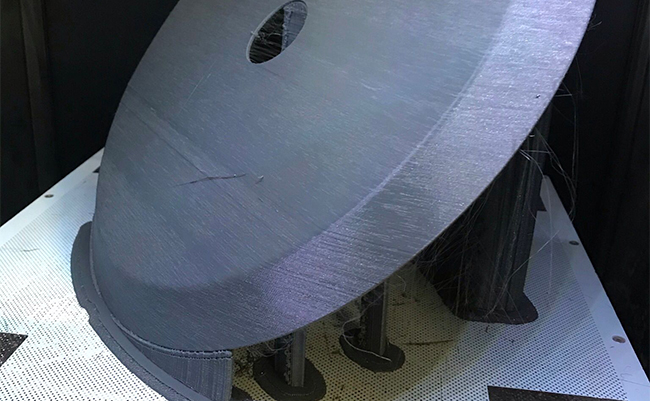
Etap 3: Obróbka końcowa i składanie modeli
Następnie Piotr wygładził wydrukowane w 3D części do skutera za pomocą szpachli natryskowej i nałożył na ich powierzchnię lakier bazowy. W kolejnym kroku, aby nadać jeszcze większą głębię koloru i lekko błyszczące wykończenie, modele zostały pokryte dodatkową warstwą lakieru transparentnego i pozostawione do wyschnięcia. W tym momencie twórca mógł przejść do jednej ze swoich ulubionych czynności podczas procesu tworzenia funkcjonalnych elementów pojazdów – składania części. “Uwielbiam proces składania dużych modeli wydrukowanych w 3D z kilku mniejszych elementów. Przypomina mi to trochę składanie modeli samolotów z dzieciństwa. To nostalgiczne uczucie, które bardzo lubię” – zauważa Piotr.
Korzyści z zastosowania druku 3D w niewielkim zakładzie motoryzacyjnym
Według Piotra Krzyczkowskiego, druk 3D oferuje możliwości, które wcześniej po prostu nie istniały. Szczególnie podkreśla aspekt szybkiego prototypowania, nieoceniony w motoryzacji, gdzie części często muszą przejść szczegółowe testy pod kątem ich właściwości mechanicznych, lub muszą być produkowane na miejscu, ze względu na niedobór komponentów. “Nie ma nic wspanialszego, moim zdaniem, niż gdy masz wszystko czego potrzebujesz do produkcji we własnym warsztacie. Potrzebujesz konkretnej części, siadasz przy komputerze, modelujesz ją i w ciągu zaledwie kilku godzin trzymasz w ręku fizyczny model, czy to do testów funkcjonalnych czy docelowego zastosowania”. Założyciel Falectry zauważa również jak bardzo uniwersalna jest technologia wytwarzania przyrostowego dla branży motoryzacyjnej: “Moim zdaniem druk 3D sprawdza się genialnie w wielu równych miejscach i etapach w branży motoryzacyjnej, począwszy od samego projektowania, poprzez tworzenie komponentów do istniejących samochodów, a skończywszy na spersonalizowanych częściach dla indywidualnych klientów. Druk 3D pozwolił mi zaoszczędzić mnóstwo czasu, jak również pieniędzy, które musiałbym wydać, jeżdżąc do różnych podwykonawców, aby zlecić wykonanie wspomnianych części tradycyjnymi metodami” – podkreśla Krzyczkowski.
Z własnego doświadczenia Piotr Krzyczkowski poleca przede wszystkim Zortrax M300 Plus. “Zortrax M300 Plus to niezawodna maszyna do drukowania wysokiej jakości części o dużych rozmiarach. Poleciłbym ten sprzęt zarówno profesjonalistom z branży motoryzacyjnej, jak i fanom tuningu aut, którzy chcą wydrukować części, które będą miały fizyczne zastosowanie w prototypach zbliżonych do wersji produkcyjnej” – podsumowuje Piotr Krzyczkowski.
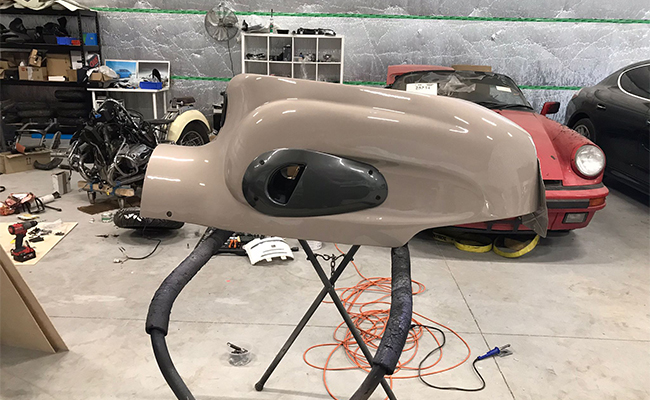
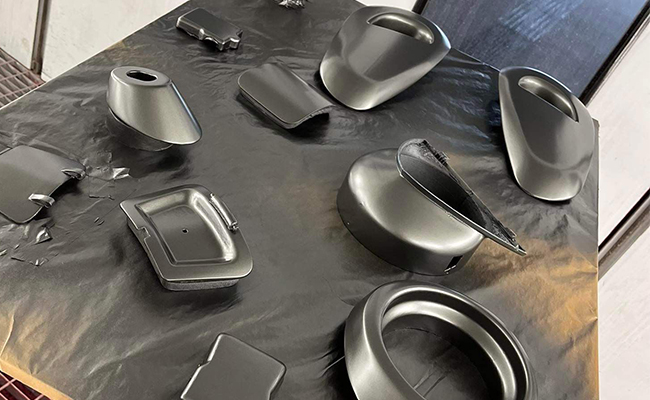
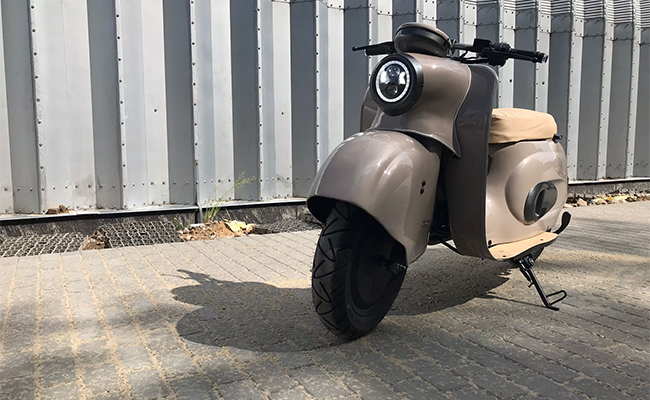
Gdyby nie technologia druku 3D, proces budowy elementów funkcjonalnych i ozdobnych trwałby znacznie dłużej i nie byłby tak precyzyjny. Dzięki zeskanowaniu głównego korpusu skutera i zmierzeniu poszczególnych komponentów, możliwe było wymodelowanie w 3D wszystkich elementów zewnętrznych. Docelowy skuter z elementami drukowanymi w 3D wyszedł tak dobrze, że po jego zaprezentowaniu Falectra zyskała zainteresowanie klientów z całego świata i obecnie zajmuje się produkcją kilku kolejnych egzemplarzy Be-e na potrzeby nowo otrzymanych zleceń. Projekt “Be-e” zrobił również ogromne wrażenie na prezesie firmy CD PROJEKT RED, twórcy serii gier Wiedźmin i Cyberpunk 2077, który postanowił zaangażować się w jego stworzenie. Klasyczny skuter już wkrótce ozdobi wnętrza jednej z siedzib jego firmy.
Dowiedz się więcej o desktopowych drukarkach 3D Zortrax M300 Plus i Zortrax M200 Plus wykorzystanych w najnowszym projekcie Falectry.
Po inne ciekawe historie użytkowników z branży motoryzacyjnej i wiele innych zapraszamy na nasz blog Zortrax.
Jeśli chcesz porozmawiać o najlepszej konfiguracji druku 3D dla Twojej firmy, napisz do nas na adres: sales@zortrax.com. Nasi specjaliści chętnie doradzą w tej kwestii.
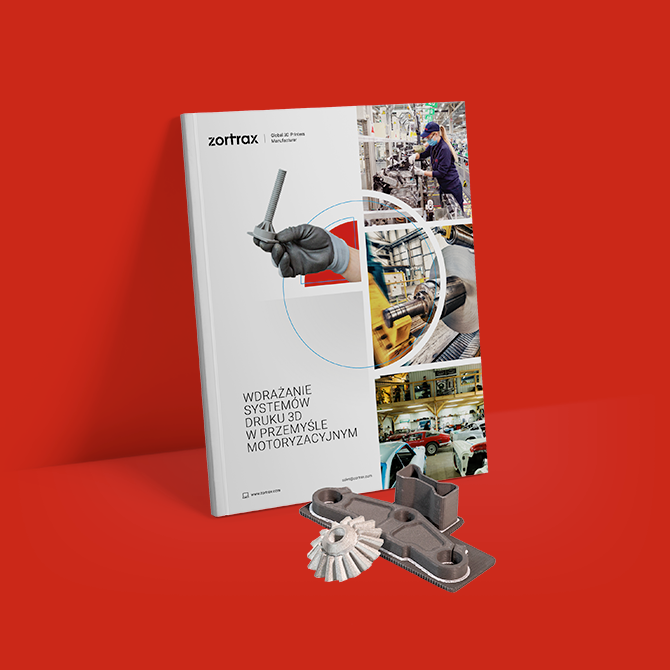