Materiały do druku 3D dla zastosowań w przemyśle motoryzacyjnym
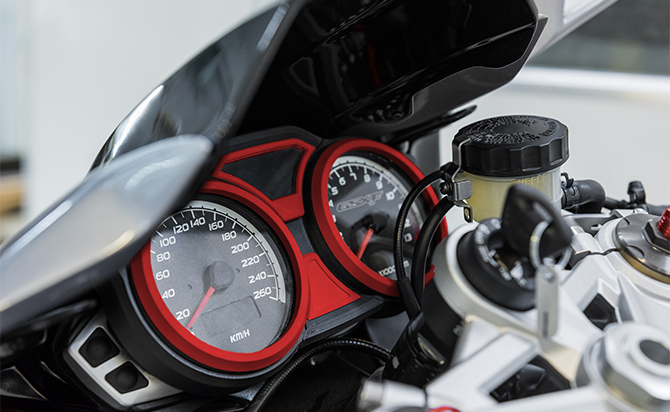
Technologia druku 3D jest powszechnie stosowana w przemyśle motoryzacyjnym – niemal wszyscy główni producenci posiadają już systemy wytwarzania addytywnego wdrożone w swoich fabrykach i centrach projektowych. Poniżej znajduje się krótki przegląd najpopularniejszych materiałów do druku 3D, wykorzystywanych zarówno na etapie prototypowania, jak i w cyklu wytwarzania produktów w motoryzacji.
Ekonomiczny materiał do druku 3D w motoryzacji: Z-ABS
Z-ABS to filament do druku 3D kompatybilny z niemal wszystkimi drukarkami 3D Zortrax, takimi jak M200 Plus, M300 Plus czy M300 Dual. Materiał bazuje na standardowym styrenie akrylonitrylowo-butadienowym, który jest jednym z najpopularniejszych tworzyw sztucznych będących obecnie w użyciu. Ponieważ materiał ten jest tak powszechny i może być przetwarzany przez niemal wszystkie drukarki 3D, jest to jedna z najbardziej opłacalnych opcji tworzenia części drukowanych w 3D. To dlatego wielu producentów samochodów, takich jak Toyota, drukuje swoje wczesne prototypy z Z-ABS. W ten sposób można wykonać wiele iteracji projektu w niskobudżetowy sposób.
Ponadto istnieją przypadki, w których właściwości termiczne i mechaniczne Z-ABS są wystarczające dla docelowych części. Jednym z przykładów zaczerpniętych z fabryki Toyoty w Polsce jest osłona dźwigni zaworowych, używana do utrzymania dźwigienek zaworowych na miejscu, kiedy silnik jest przenoszony z jednej linii montażowej na drugą. Według inżynierów Toyoty, żywotność tego dźwigni wykonanej z Z-ABS na drukarce 3D Zortrax M300 Plus może wynosić nawet 6 miesięcy.
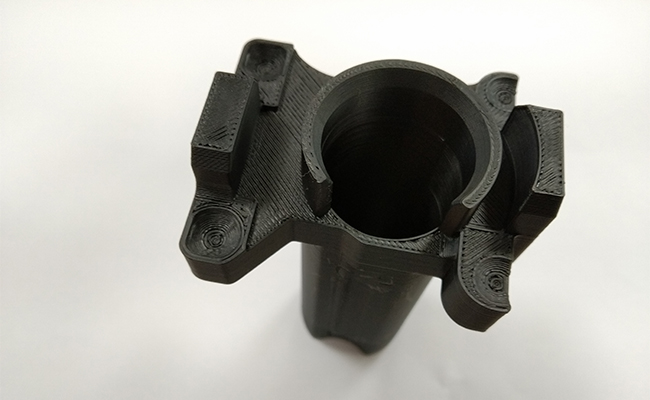
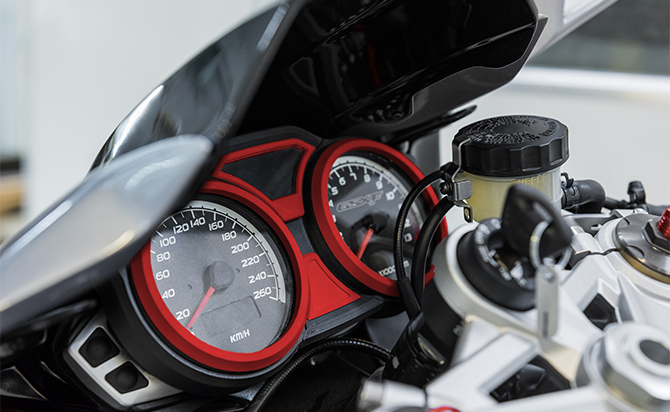
Wysokotemperaturowy filament do zastosowań motoryzacyjnych: BASF Ultrafuse® PP GF30
BASF Ultrafuse® PP GF30 to polipropylen wzmocniony w 30% włóknem szklanym. Jest to jeden z najczęściej używanych polimerów w samochodach – elementy z niego wykonane znajdziemy pod maską niemal w każdym pojeździe. Aby zapewnić możliwość druku 3D z PP GF30, Zortrax nawiązał współpracę z BASF, jedną z największych, wiodących firm chemicznych na świecie, w celu skalibrowania filamentu BASF Ultrafuse® PP GF30 na drukarce 3D Zortrax M300 Dual. Części drukowane w 3D na drukarce Zortrax M300 Dual z użyciem filamentu BASF Ultrafuse® PP GF30 mogą pracować w tym samym zakresie temperatur, co formowane elementy PP GF30 instalowane jako zapasowe w większości samochodów. Materiał ten zachowuje swoje właściwości w mrozie przekraczającym -20 ºC i w upale sięgającym 120 ºC. Dlatego część samochodowa wydrukowana z BASF Ultrafuse® PP GF30 może bezpiecznie wytrzymać w pojeździe pozostawionym na zewnątrz w zimie bez nadmiernej kruchości, a także wytrzymać wysokie temperatury pod maską, gdy silnik pracuje.
Takie właściwości umożliwiają wykorzystanie części drukowanych 3D z BASF Ultrafuse® PP GF30 do wielu zastosowań. Na etapie prototypowania takie części mogą być wykorzystywane w samochodach demonstracyjnych, a nawet w krótkoseryjnych, przedprodukcyjnych pojazdach używanych do testów długodystansowych i środowiskowych. Na etapie produkcji materiał BASF Ultrafuse® PP GF30 może być wykorzystywany do drukowania w technologii 3D przyrządów i uchwytów produkcyjnych, które muszą zachować wysoką sztywność w szerokim zakresie temperatur. Mniejsze warsztaty mogą również wykorzystać ten materiał do drukowania zapasowych elementów pod maską, które nie są już produkowane lub są z innych powodów są niedostępne na rynku.
Elastomerowa żywica do druku 3D w branży automotive: BASF Ultracur3D® EL 60
Żywice elastomerowe są stosowane w przemyśle motoryzacyjnym głównie na etapie produkcji. Gumopodobne komponenty służą jako zastępcze chwytaki ramion robotów i zderzaki zapobiegające uszkodzeniu przez maszyny powierzchni produkowanych części. Drukowanie z żywicy elastomerowej w 3D takich części jak chwytaki robotów stanowi wydajną i szybką metodę produkcji.
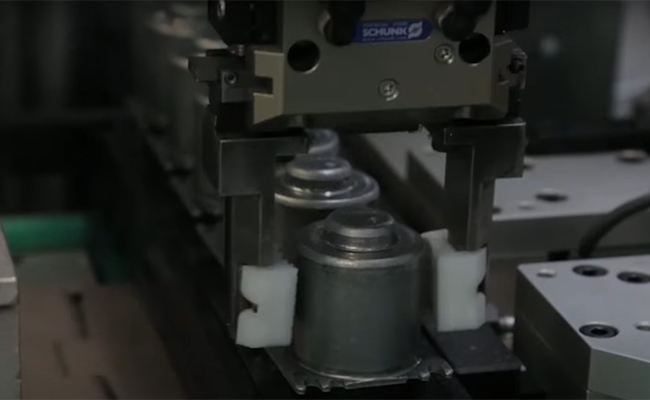
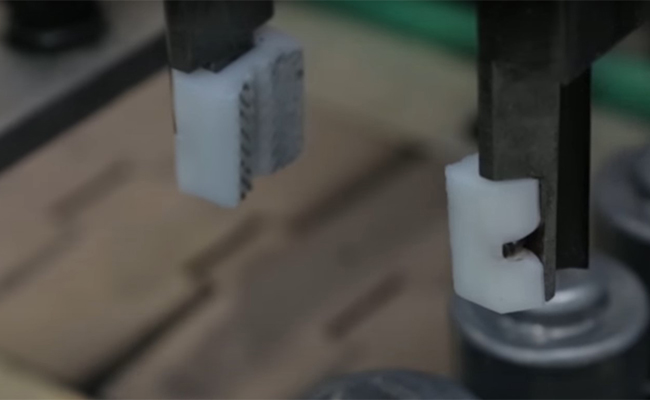
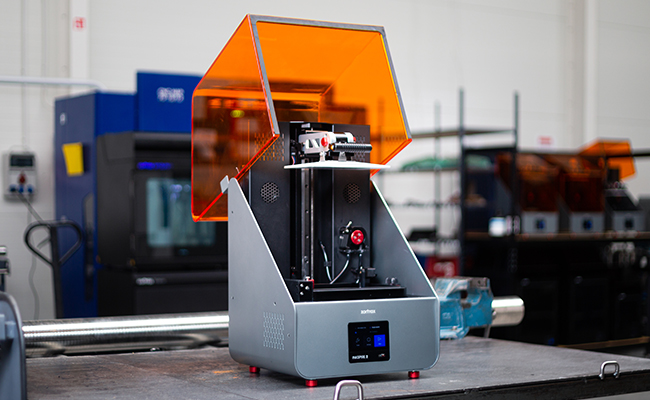
Materiał charakteryzuje się sprężystością odbicia mierzoną na poziomie 21% i niską twardością Shore’a wynoszącą 75 A. Kluczową zaletą materiału BASF Ultracur3D® EL 60 jest to, że wykazuje on bardzo niski stopień kompresji w czasie, co oznacza, że drukowane w 3D chwytaki i zderzaki na dłużej zachowują swoją geometrię.
BASF Ultracur3D® EL 60 jest skalibrowany na drukarce 3D UV LCD Zortrax Inkspire 2, a jakość drukowanych na niej części została potwierdzona w rygorystycznym, dwuetapowym procesie przez inżynierów BASF. Takie połączenie umożliwia wytwarzanie elastycznych, gumopodobnych komponentów z wysoką precyzją i dużą szybkością oferowaną przez Inkspire 2.
Wysokowydajny filament do druku 3D: VICTREX PAEK AM™ 200
VICTREX AM™ 200 to jeden z najbardziej innowacyjnych wysokowydajnych polimerów na rynku. Należy do tej samej rodziny poliaryleterketonów (PAEK) co Z-PEEK, niewiarygodnie odporny materiał wykorzystywany w przemyśle kosmicznym i został zaprojektowany od podstaw do druku 3D. Dzięki temperaturze ciągłego użytkowania (CUT) bliskiej 260 ºC, doskonałej odporności na chemikalia i wytrzymałości na rozciąganie przekraczającej 70 MPa, AM™ 200 może być stosowany w wielu wymagających środowiskach. Jego kluczową zaletą w porównaniu z innymi wysokowydajnymi polimerami jest wyjątkowo dobra przyczepność międzywarstwowa, która znacząco zmniejsza anizotropię części drukowanych w 3D. Wytrzymałość na rozciąganie mierzona w osi Z, która zawsze jest najsłabsza w częściach wykonanych na drukarkach 3D opartych na ekstruzji, osiąga 60% wytrzymałości na rozciąganie mierzonej w najmocniejszej osi XY w częściach drukowanych w 3D z VICTREX AM™ 200.
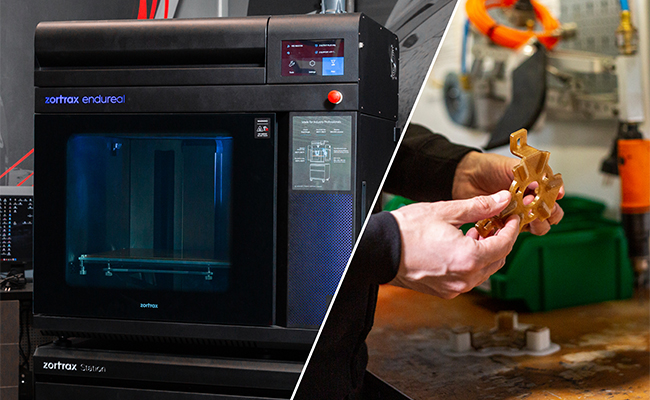
Zortrax Endureal oraz wydruki 3D wykonane z użyciem wysokowydajnego filamentu VICTREX PAEK AM 200.
AM™ 200 jest skalibrowany do pracy z Zortrax Endureal, największą przemysłową drukarką 3D produkowaną przez Zortrax. Chociaż możliwość drukowania 3D przy użyciu AM™ 200 jest większą inwestycją niż przy użyciu maszyn i materiałów klasy desktop, to z pewnością się opłaca, jeśli przypadek użycia wymaga wyższego poziomu wydajności. Co więcej, drukarka Zortrax Endureal 3D umożliwia również drukowanie 3D elementów metalowych, o których więcej szczegółów poniżej.
Druk z metalu w motoryzacji: BASF Ultrafuse® 316L
Druk 3D z metali w przemyśle motoryzacyjnym może służyć wielu celom. Najbardziej ekstremalnym z nich jest drukowanie w 3D końcowych części do pojazdów klasy high-end, takich jak Bugatti, które z powodzeniem przetestowało topologicznie zoptymalizowany zacisk hamulcowy wydrukowany w całości z tytanu. Bardziej powszechne zastosowania druku 3D z metali obejmują jednak części do prototypów samochodów demonstracyjnych i przyrządów do produkcji końcowej.
Po profesjonalnej obróbce końcowej, części drukowane w 3D z BASF Ultrafuse® 316L zamieniają się w standardową, litą stal nierdzewną 316L. Stal ta może być polerowana, spawana i w inny sposób przetwarzana jak standardowy metal. Ponieważ stal 316L jest często używana do produkcji elementów dekoracyjnych we wnętrzach samochodów, materiał ten może być wykorzystywany do produkcji prototypowych elementów wnętrz pojazdów na wczesnym etapie rozwoju. Jest ona również wystarczająco wytrzymała dla elementów mechanicznych. Na etapie produkcji materiał może być wykorzystany do druku 3D niestandardowych narzędzi lub przyrządów używanych na linii montażowej. Szczególnie w przypadku niewielkich rozmiarów, skomplikowanych części, technologia druku 3D okazuje się bardziej opłacalna niż stosowanie 5-osiowych maszyn CNC.
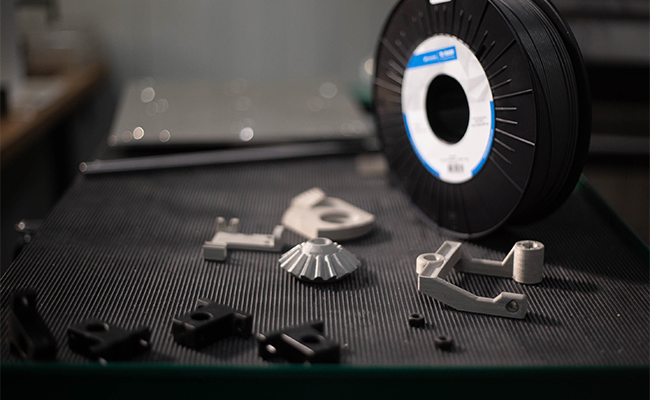
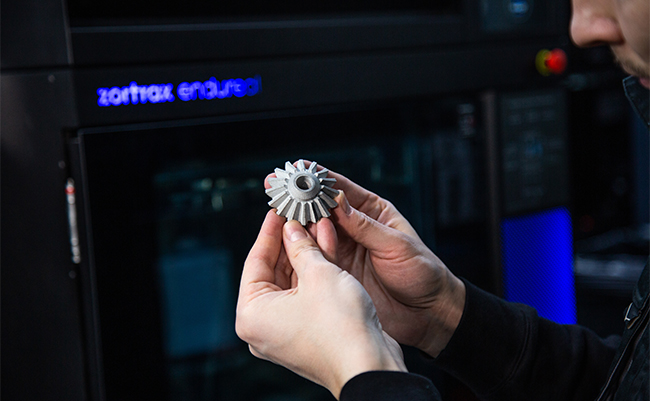
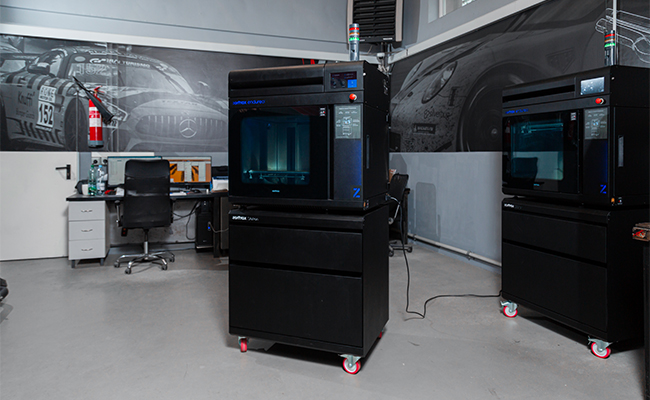
Podejście Zortrax do druku 3D metali polega na wykorzystaniu urządzenia Zortrax Endureal do drukowania filamentu wykonanego w 20% z wypełniacza polimerowego i w 80% z proszku metalicznego. Takie części, po wykonaniu druku 3D, są następnie wysyłane do wyspecjalizowanych usługodawców, którzy przeprowadzają je przez dwa etapy skomplikowanej obróbki końcowej. Pierwszy etap zwany debindingiem wykorzystuje wysoką temperaturę i środki chemiczne do usunięcia wypełniacza polimerowego z wydrukowanej w 3D części. Drugi etap to spiekanie, którego celem jest stopienie pozostałego proszku metalicznego w litą stal. Choć proces ten wymaga nieco dłuższego czasu realizacji niż w przypadku polimerów, które mogą być poddane obróbce na miejscu, to w większości przypadków i tak jest szybszy i bardziej opłacalny niż zlecanie produkcji części zewnętrznym dostawcom korzystającym z 5-osiowych maszyn CNC.
W ofercie Zortrax znajduje się znacznie więcej materiałów, które można wykorzystać w zastosowaniach motoryzacyjnych, a których nie sposób tu wymienić. Skontaktuj się z naszym przedstawicielem, aby omówić swoje potrzeby, a my zaproponujemy najbardziej optymalne rozwiązania w zakresie druku 3D, dostosowane specjalnie do Twojego biznesu.
Jeśli chcesz porozmawiać o najlepszej konfiguracji druku 3D dla Twojej firmy, napisz do nas na adres: sales@zortrax.com.