Druk 3D rozwiązaniem problemów z dostępnością części w sektorze motoryzacyjnym
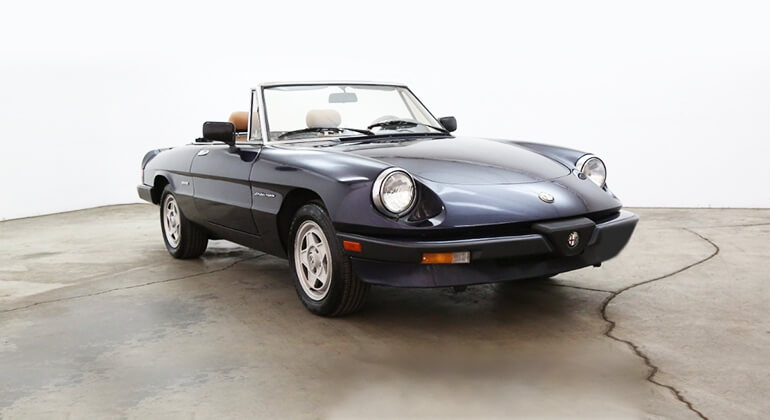
Przemysł motoryzacyjny od wielu lat korzysta z technologii wytwarzania przyrostowego. Druk 3D usprawnia procesy projektowania i budowy samochodów, dając producentom większą swobodę projektowania i lepsze możliwości wydajnego prototypowania. Jednak w niektórych przypadkach drukarki 3D są wykorzystywane w branży motoryzacyjnej w nieco inny sposób. Oto przykład firmy, która modeluje w 3D i odtwarza uszkodzone lub niedostępne części pojazdów, używając do tego celu drukarkę 3D Zortrax.
Druk 3D w inżynierii odwrotnej: od projektów CAD do części funkcjonalnych
Alfa Project to polska firma należąca do braci Mateusza i Przemysława Dziwiszów, którzy interesują się włoską motoryzacją, w szczególności samochodami marki Alfa Romeo. Po wielu latach użytkowania samochodów tej marki zdecydowali się na zakup klasycznej Alfy Romeo Spider z 1988 roku. Zgodnie z przewidywaniami wnętrze auta nosiło znaczne ślady zużycia: „Wiele plastikowych elementów uległo uszkodzeniu. Części zamienne dostępne na rynku były bardzo drogie i nadal posiadały wady. Nawet kiedy znaleźliśmy dobrze zachowane elementy, wiedzieliśmy, że plastik użyty do ich produkcji z pewnością stał się bardzo kruchy po tylu latach”. – zaznacza Mateusz.
Mateusz i Przemysław zdecydowali się samodzielne odtworzyć uszkodzone części poprzez zaprojektowanie ich w 3D i zlecenie ich druku zewnętrznym wykonawcom. Następnie, gdy pokazywali efekty swojej pracy innym entuzjastom samochodów zabytkowych, dostrzegli rosnące zapotrzebowanie na tworzenie elementów wyposażenia wnętrz samochodów niedostępnych komercyjnie. Z tego względu postanowili zakupić swoję pierwszą drukarkę 3D Zortrax M300 Plus i rozwinąć projekt polegający na odtwarzaniu części dla innych właścicieli samochodów.
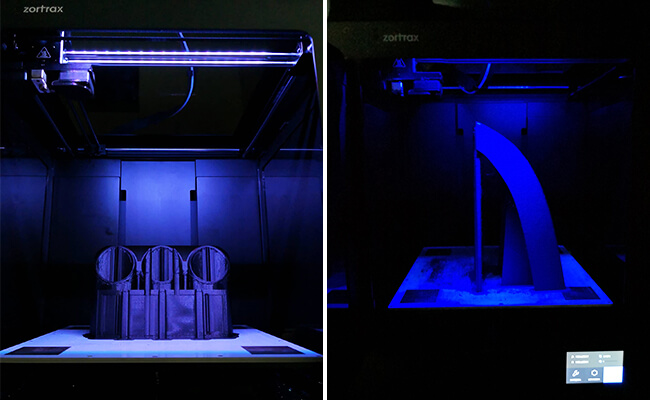
Druk 3D części zaprojektowanych przez Alfa Project na drukarce Zortrax M300 Plus.
Zlecenia, które otrzymywali, bardzo często dotyczyły elementów zbyt deformowanych, by można je było zeskanować w 3D. Tak więc zespół Alfa Project uznał, że jedynym sposobem na odtworzenie danej części jest ręczne zaprojektowanie jej w programie do modelowania 3D. Zespół pracuje w technice inżynierii odwrotnej i używa drukarki 3D do protypowania, a czasem nawet produkcji końcowego elementu. Jak zazwyczaj Alfa Project rozpoczyna swoją pracę? Najpierw dzielą zamówioną część na poszczególne komponenty, aby zebrać niezbędne dane do stworzenia modelu 3D w oprogramowaniu CAD. Reszta prac odbywa się przy użyciu drukarki 3D: „Druk 3D to narzędzie, które pozwala w łatwy sposób przenieść projekt prosto z programu CAD do rzeczywistości. To znacznie ułatwia pracę w inżynierii odwrotnej dla przemysłu motoryzacyjnego”. – mówi Mateusz.
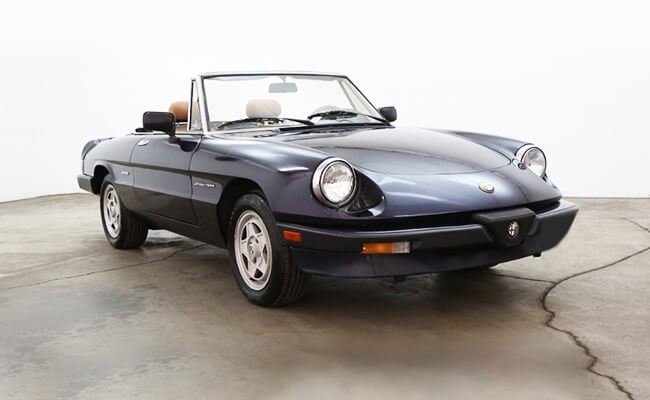
Alfa Romeo Spider, należąca do Mateusza i Przemysława z Alfa Project.
Udoskonalanie części końcowych dzięki szybkiemu prototypowaniu
Mateuszowi i Przemysławowi bardzo zależy na dostarczaniu niezawodnych produktów, które mogą zastąpić te montowane w samochodach i zachować te same funkcjonalności. Zespół modeluje i odtwarza w 3D spojlery, zderzaki, gałki zmiany biegów, osłony mechanizmów skrzyni biegów, uchwyty lusterek oraz wiele elementów deski rozdzielczej, takich jak ramki zegarów, nawiewy, panele sterowania klimatyzacji i zaślepki. Jednak ze względu na to, że oryginalne części są podatne na uszkodzenia wskutek regularnego użytkowania, zespół koncentruje się na tym, aby ulepszyć projekt i zwiększyć wytrzymałość finalnego produktu: „Projektując część, dodajemy elementy, takie jak żebra, które wzmacniają wydruk 3D, zwłaszcza w miejscach szczególnie narażonych na uszkodzenia lub tam, gdzie oryginalny element został uszkodzony.” – wyjaśnia Przemysław.

Osłona mechanizmu skrzyni biegów wydrukowana w 3D przez Alfa Project dla jednego z klientów, który także posiada Alfa Romeo Spider.
Po wstępnym modelowaniu 3D zespół przechodzi do druku 3D prototypu. Wydrukowana część jest następnie porównywana z oryginałem i dopasowywana do miejsca, w którym zostanie ostatecznie osadzona. W ten sposób zespół Alfa Project sprawdza, czy część spełnia kryteria wymiarowe i geometryczne. Jak podkreśla Mateusz, Zortrax M300 Plus jest niezbędnym narzędziem na tym etapie pracy zespołu: „Dzięki drukowi 3D możemy szybko i łatwo wprowadzać zmiany w projekcie i tworzyć elementy w krótszym czasie. Jednocześnie możemy znacznie poprawić dopasowanie drukowanych elementów do już istniejącego sprzętu”. Po zaakceptowaniu prototypu Mateusz i Przemysław kontynuują prace nad finalną częścią. Ponieważ zwykle wytwarzają pojedyncze elementy, drukarka Zortrax M300 Plus stała się główną maszyną produkcyjną w ich warsztacie, dzięki której wytwarzanie elementów jest bardziej opłacalne w porównaniu z innymi metodami, jak frezowanie czy odlewanie.
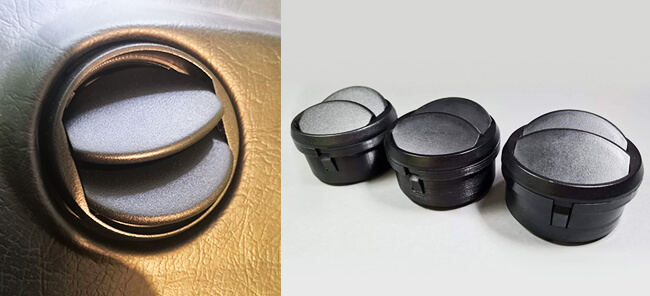
Nawiew powietrza z Alfa Romeo Spider, wydrukowany w 3D, zainstalowany w desce rozdzielczej (po lewej). Oryginalny nawiew w porównaniu z modelami 3D odtworzonymi przez Alfa Project (po prawej).
Modele 3D jako zamienniki części fabrycznych
Zespół Alfa Project ocenia każdy projekt indywidualnie pod kątem środowiska, warunków i sił, które będą oddziaływać na wytwarzany element. Pomaga im to odpowiednio ustawić geometrię podczas druku 3D, tak by gotowa część była poddawana siłom zginania, a nie cięcia, które osłabiałyby model. Mateusz i Przemysław wybierają do swoich projektów jeden z najpopularniejszych filamentów stosowanych w branży motoryzacyjnej – Z-ABS.
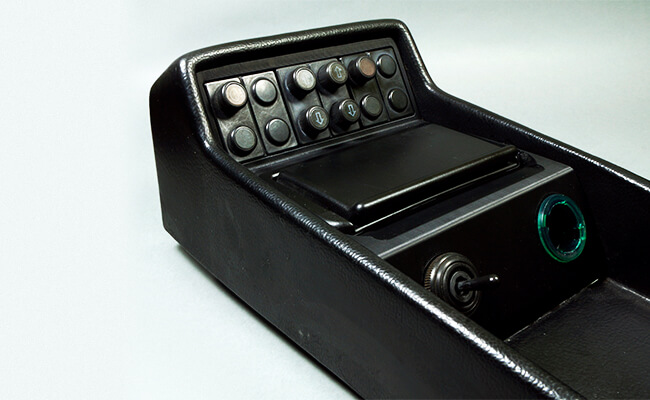
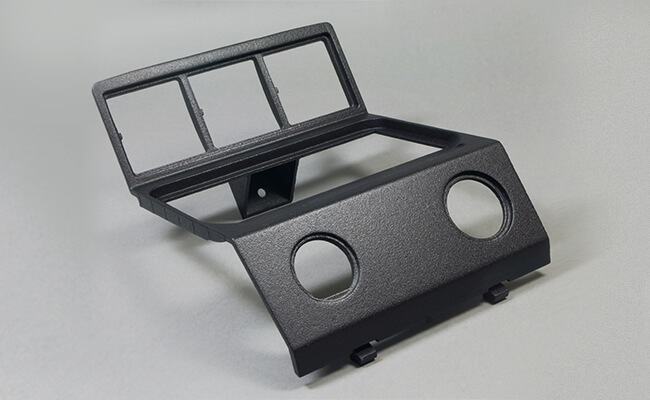
Według zespołu Alfa Project odpowiednio dobrany filament pozwala na tworzenie elementów tak wytrzymałych, jak części fabryczne: „W drukowanych elementach Z-ABS daje zadowalającą odporność na temperaturę i zginanie. Może być stosowany w modelach 3D z łącznikami lub elementami kotwiącymi”. Na koniec wydruki 3D są szlifowane i lakierowane, aby jak najwierniej odzwierciedlały oryginalne części.
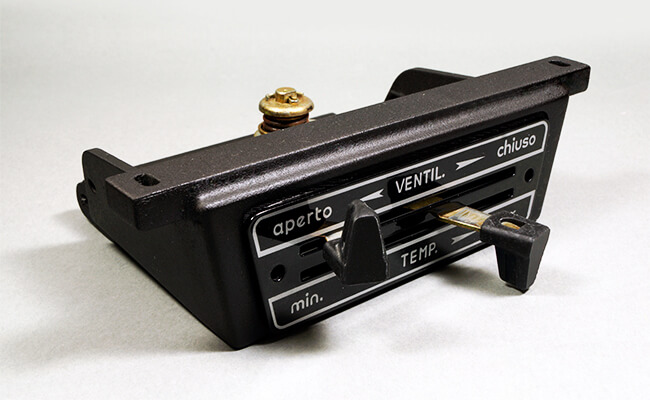
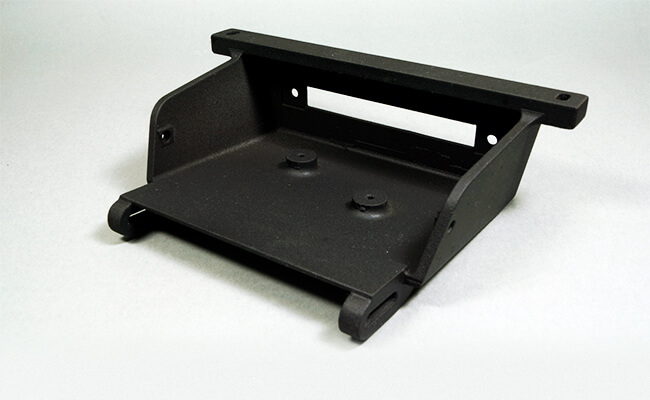
Działalność Alfa Project pozwoliła Mateuszowi i Przemysławowi rozwiązać problem dostępności elementów plastikowych w pojazdach, które nie są już produkowane. Korzystanie z drukarki 3D Zortrax M300 Plus pomaga im dostarczać wysokiej jakości części 3D z pełnym zakresem funkcjonalności. W rzeczywistości produkty Alfa Project trafiły do innych posiadaczy samochodów zabytkowych: „Obecnie nasze części są używane w pojazdach na całym świecie, a co dla nas najważniejsze – klienci są zadowoleni z naszej pracy”. W przyszłości Mateusz i Przemysław planują poszerzyć swoję ofertę o druk 3D z nowych typów filamentów, zwłaszcza tych wzmacnianych włóknem szklanym lub węglowym.
Dowiedz się, jak drukarka Zortrax M300 Plus została wykorzystana w innych projektach: Dancer Bus, ML System.