W jaki sposób zautomatyzować post-processing dla wydruków 3D w technologii FFF?
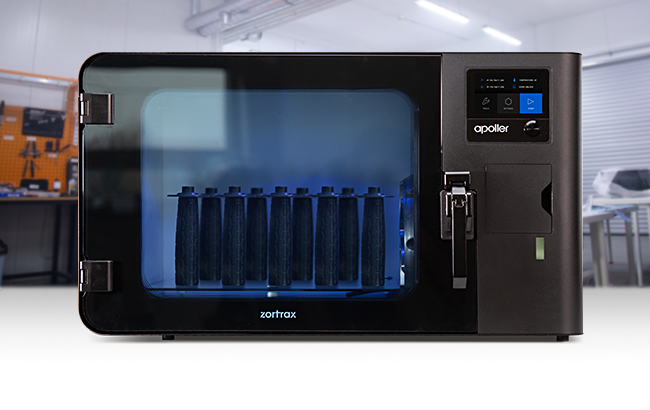
Głównymi zaletami technologii FFF, czyli druku 3D przy użyciu termoplastów w formie żyłki, są szybki czas tworzenia detali, relatywnie niska cena ich produkcji oraz możliwość używania tych samych tworzyw sztucznych co w technologii wtrysku, wykorzystywanej w produkcji seryjnej. Dzięki temu możemy szybko i tanio tworzyć jednostkowe prototypy rzeczy, które docelowo zostaną wyprodukowane w setkach tysięcy lub milionach sztuk. Równocześnie technika FFF ma jedną wadę, która bywa uciążliwa w przypadku detali o charakterze pokazowym lub wizerunkowym – na powierzchniach są widoczne tzw. prążki, czyli warstwy drukowanego modelu. Wychodząc naprzeciw temu problemowi Zortrax stworzył maszynę, która pozwala na całkowite wygładzenie ścianek detalu w sposób całkowicie zautomatyzowany!
W niniejszym poradniku znajdziecie szczegółowy opis działania Zortrax Apoller – inteligentnego urządzenia, pozwalającego na automatyczne wygładzanie modeli wykonanych na drukarkach 3D z wybranych tworzyw termoplastycznych. Dowiecie się, na czym polega kontrolowany proces wygładzania oparami acetonu lub butanonu (MEK), gdzie i kiedy warto go stosować oraz dlaczego w przeciwieństwie do innych, amatorskich metod, jest on bezwzględnie bezpieczny dla użytkownika.
Kiedy i dlaczego warto wygładzać wydruki 3D?
Praktycznie od samego początku istnienia drukarek 3D typu FFF, ich użytkownicy próbowali rozwiązać kwestię widocznych warstw na powierzchni modeli, które nadawały im charakterystyczną chropowatość w dotyku. O ile w przypadku detali użytkowych nie stanowiło to nigdy większej przeszkody (wydrukowany element miał przede wszystkim działać i spełniać powierzoną mu funkcję), o tyle przy detalach pokazowych – wszelkiego rodzaju figurkach, ale też finalnych prototypach o charakterze wizerunkowym, budziło to problemy natury estetycznej. Jednakże wygładzanie detali ma istotne znaczenie także przy tworzeniu mniej oczywistych aplikacji…
Detale o gładkich powierzchniach doskonale sprawdzają się we wszystkich ruchomych mechanizmach, gdyż są lepiej ze sobą spasowane i mają mniejsze tarcie. To z kolei prowadzi do mniejszej ilości wytwarzanego ciepła, co zwykle jest dobrą rzeczą z punktu widzenia inżynierii, gdzie kwestia rozpraszania ciepła jest często poważnym problemem.
Wygładzone modele można z powodzeniem wykorzystywać także jako gniazda do form odlewniczych. Jest to szczególnie ważne, ponieważ charakterystyczne warstwy, jakie są widoczne na detalach zaraz po zdjęciu ich ze stołu drukarki 3D, zostałyby odwzorowane na ściankach formy do odlewu.
Kolejna grupa aplikacji, to modele o wysokiej wodoszczelności, jaka jest uzyskiwana w procesie wygładzania, poprzez powierzchniowe topienie ich powierzchni.
Amatorskie sposoby na wygładzanie powierzchni wydruków 3D
Najbardziej oczywistym sposobem radzenia sobie z widocznymi warstwami, jest szlifowanie ścian detalu oraz szpachlowanie lub pokrywanie specjalnymi, dedykowanymi żywicami. Niestety wiąże się to zawsze z dużym nakładem czasu, a bywa że dany model ma na tyle skomplikowaną geometrię, że skuteczne wyszlifowanie go jest po prostu niemożliwe.
Alternatywnym rozwiązaniem jest chemiczne wygładzanie ścianek w oparach acetonu lub butanonu (MEK). W zależności od rodzaju użytego filamentu powierzchnie stają się błyszczące lub matowe, a same warstwy niewidoczne. Amatorskie wygładzanie polega na tym, że detale są wkładane do pojemnika (np. słoika) z nalanym do wnętrza środkiem chemicznym, zamykane i pozostawiane na kilka godzin, podczas których opary wydzielane przez chemikalia wygładzają krawędzie delikatnie je rozpuszczając. Niektórzy użytkownicy posuwają się do dużo bardziej ekstremalnych rozwiązań – gotują aceton w naczyniach kuchennych na ogniu, a następnie zawieszają nad nimi wydruki 3D i eksponują je na powstałe w procesie gotowania opary. Jest to skrajnie nieodpowiedzialna i niebezpieczna metoda, grożąca samozapłonem rozpuszczalnika (co w niektórych przypadkach zostało nawet udokumentowane na amatorskich filmach video)!
Bez względu na wariant wyżej opisanej metody, proces chemicznego wygładzania wydruków 3D w wydaniu amatorskim jest zawsze bardzo ryzykowny z uwagi na wysoką lotność stosowanych chemikaliów oraz powiązanym z tym ryzykiem zatrucia. Dodatkowo trudno jest uzyskać równomiernie wygładzony model, gdyż opary acetonu lub MEK nigdy nie pokrywają detalu w taki sam sposób.
Wady i zagrożenia wynikające z wygładzania wydruków 3D:
- rezultaty nigdy nie będą powtarzalne, ponieważ utrzymanie tych samych warunków wygładzania za każdym razem jest praktycznie niemożliwe
- powierzchnia wydruku 3D nie będzie równomiernie wygładzona, z uwagi na niekontrolowaną cyrkulację oparów
- zbyt duża ilość oparów, rozprowadzanych w niekontrolowany i nierównomierny sposób może spowodować przypadkowe rozpuszczenie lub deformację wydruków 3D wyposażonych w małe detale
- ryzyko zatrucia oparami chemikaliów lub samozapłonu w przypadku ich podgrzewania / gotowania.
Zortrax Apoller i profesjonalne wygładzanie powierzchni wydruków 3D
Mimo wyżej wymienionych niedoskonałości, efekt końcowy procesu, czyli detal o wyglądzie zbliżonym do idealnie gładkiego detalu stworzonego metodą formowania wtryskowego jest na tyle intrygujący i pożądany, że wielu użytkowników drukarek 3D cały czas poszukuje mniej lub bardziej profesjonalnych sposobów na to aby go osiągnąć. W 2018 roku zespół badawczo-rozwojowy Zortrax postanowił ostatecznie zmierzyć się z tym wyzwaniem prezentując maszynę, która nie tylko w pełni usystematyzowała i zautomatyzowała cały przebieg chemicznego wygładzania wydruków 3D, ale uczyniła go także całkowicie bezpiecznym.
Główną zasadą przyświecającą konstruktorom Zortrax tworzącym urządzenie było to samo co w przypadku wszystkich drukarek 3D firmy – Apoller miał być przede wszystkim intuicyjny i prosty w obsłudze, równocześnie gwarantując najwyższą jakość pracy. W efekcie użytkownik po prostu otwiera drzwiczki komory produkcyjnej, wkłada do jej wnętrza modele, uruchamia proces wygładzania jednym przyciskiem, a po jego zakończeniu po prostu wyjmuje gotowe, smukłe detale.
Istotą całego procesu jest autorska technologia Smart Vapor Smoothing (SVS), opracowana przez inżynierów Zortrax. Apoller posiada przestronną komorę roboczą o wymiarach 300 x 250 x 250 mm, która jest w stanie pomieścić znakomitą większość detali drukowanych na najpopularniejszych, desktopowych drukarkach 3D typu FFF. Komora jest hermetyczna i podwójnie uszczelniona, co niweluje jakiekolwiek ryzyko przypadkowego wydostania się chemicznych oparów na zewnątrz. W pracy wykorzystuje aceton lub MEK, które są przechowywane w zbiornikach wbudowanych wewnątrz urządzenia.
Zortrax Apoller jest bardzo wydajny – jedna butelka rozpuszczalnika o pojemności 300 ml wystarcza na wiele sesji wygładzania. Równocześnie, w ciągu jednego dnia Apoller może wygładzić tygodniową wydajność czterech typowych, desktopowych drukarek 3D typu FFF.
Koniec z ekspozycją użytkownika na opary
Modele są układane wewnątrz komory roboczej na szklanym stole. Po ich zamknięciu można uruchomić proces wygładzania przy pomocy kolorowego panelu dotykowego. Apoller wpompowuje powietrze z komory, dzięki czemu obniża się ciśnienie poniżej poziomu otoczenia. Zapobiega to wydostawaniu się oparów na zewnątrz oraz utrzymuje komorę w stanie zamkniętym, nawet w przypadku przerwy w zasilaniu. Przez cały czas trwania procesu, użytkownik nie ma styczności z oparami emitowanymi przez chemikalia.
Automatyczne wygładzanie
Gdy w komorze Apollera zostanie osiągnięte odpowiednie ciśnienie, ściany zostają podgrzane i do wnętrza zostaje wprowadzony rozpuszczalnik. Jest on wlewany do zbiornika umieszczonego pod szklanym stołem, na którym są ułożone detale. Urządzenie zaczyna w kontrolowany i bezpieczny sposób zmieniać temperaturę w komorze – najpierw na tyle aby odparować chemikalia, a następnie za pomocą autorskiego systemu cyrkulacji wynosi opary ku górze, aby w równomierny i dokładny sposób pokryły modele.
Powierzchnia modeli ma niższą temperaturę niż parujący rozpuszczalnik, co powoduje, że opary skraplają się na ich powierzchni. Cienkie ścianki oraz drobne detale nagrzewają się szybciej od większych, dzięki czemu są pokryte mniejszą ilością rozpuszczalnika. Dzieje się tak, ponieważ wyższa temperatura zapobiega kondensacji oparów na tego typu miejscach. W konsekwencji drobne szczegóły są wygładzane, ale nie ulegają deformacji. Autorski system cyrkulacji SVS pozwala także na skuteczne wygładzenie elementów ruchomych bez ryzyka przypadkowego sklejenia się ze sobą powiązanych części.
Po zakończeniu procesu wygładzania, krążące opary chemikaliów zostają wprowadzone do systemu kondensacji gdzie są skraplane. Skroplony rozpuszczalnik zostaje odprowadzony do zbiornika i może być użyty ponownie. Ostatni krok to ponowne podgrzanie komory roboczej urządzenia w celu wysuszenia wygładzonych modeli.
Proces jest w pełni zautomatyzowany i trwa łącznie trzy godziny. Wygładzone modele są gotowe do użycia bezpośrednio po wyjęciu z komory i nie wymagają absolutnie żadnej dodatkowej pracy post-processingowej.
Ciągłe bezpieczeństwo użytkownika i wiele poziomów redundancji
Aceton i MEK to chemikalia lotne i maszyna pracująca z nimi musi być zaprojektowana z myślą o bezwzględnym bezpieczeństwie w miejscu pracy. Zortrax Apoller został wyposażony w szereg systemów bezpieczeństwa z wieloma poziomami redundancji. Doskonałym przykładem obrazującym tego typu podejście może być np. kwestia zastosowania dwóch zestawów uszczelek w drzwiach do komory roboczej maszyny. Uszkodzenie uszczelki spowoduje rozszczelnienie komory i dostanie się do jej wnętrza powietrza. Aby uniknąć tego ponad wszelką wątpliwość – Apoller został wyposażony w drugi zestaw uszczelek. Mimo że zbędny z punktu widzenia funkcjonalności urządzenia, został dodany na tzw. „wszelki wypadek”…
Ten poziom redundancji został wdrożony we wszystkich krytycznych obszarach konstrukcji Apollera. Np. w przypadku wystąpienia przerwy w zasilaniu, komora robocza pozostanie zamknięta. Po przywróceniu zasilania oprogramowanie Apollera będzie wiedziało, co się stało i automatycznie oczyści komorę z chemikaliów, zanim ktokolwiek będzie mógł ją otworzyć.
Certyfikat bezpieczeństwa ATEX
Wszystkie komponenty, w tym przewody elektryczne, mogące wejść w kontakt z chemicznymi oparami, posiadają certyfikat zgodności z dyrektywą ATEX 2014/34 / UE, regulującą normy bezpieczeństwa niezbędne dla urządzeń działających w atmosferach wybuchowych. Dzięki temu, Apoller może być używany nawet w środowisku biurowym.