Jak fabryka Toyoty wykorzystuje drukarki 3D Zortrax
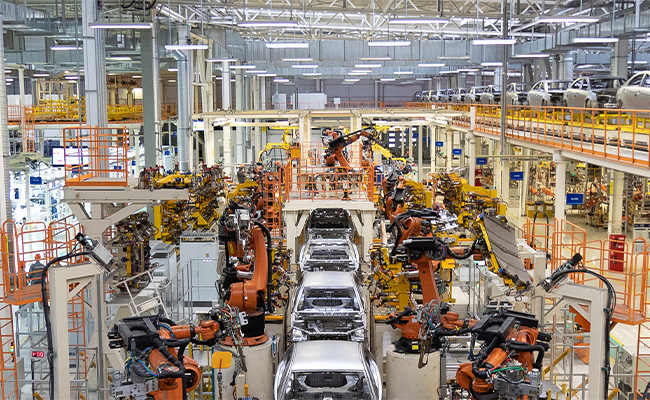
Fabryki Toyoty w Polsce specjalizują się w produkcji napędów hybrydowych i konwencjonalnych, które trafiają do montowni samochodów w całej Europie. Polskie fabryki zatrudniają ponad trzy tysiące osób i osiągają imponującą wydajność produkcyjną. Oto, w jaki sposób drukarki 3D Zortrax są wykorzystywane do optymalizacji kosztów i skrócenia czasu wykonania komponentów w jednej z największych fabryk motoryzacyjnych w Europie.
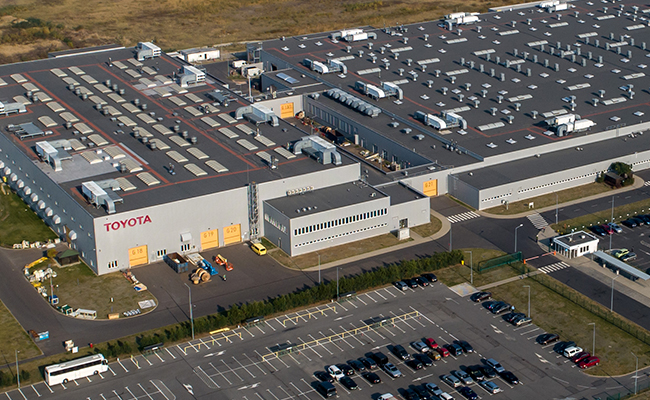
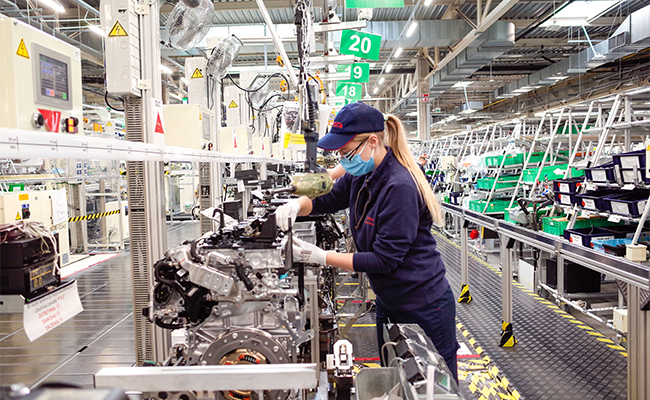
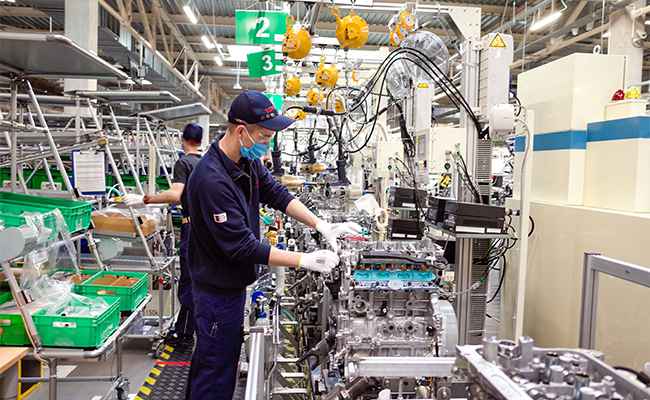
Do czego Toyota używa drukarek 3D Zortrax
„Zacznijmy od głównego zadania, za które odpowiadamy w Polsce. Toyota to ogromny, globalny producent, działamy więc w ramach większego systemu produkcyjnego z różnymi wyspecjalizowanymi zakładami zlokalizowanymi na całym świecie. Naszym zadaniem jest montaż silników i dostarczenie ich do montowni samochodów koncernu Toyota”, mówi Łukasz Kondek, inżynier odpowiedzialny za druk 3D w fabryce Toyoty. Silniki są montowane z części dostarczanych z fabryk w całej Europie.
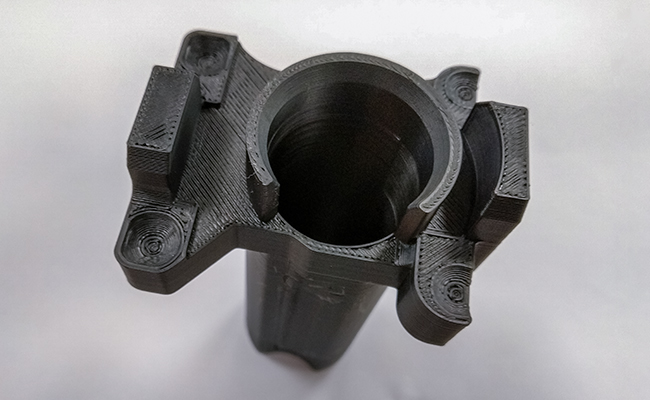
Osłona dźwigni zaworu wydrukowana w fabryce Toyoty na drukarce 3D Zortrax M300 Plus.
„Ten profil produkcji przekłada się bezpośrednio na to, do czego używamy druku 3D w motoryzacji. Zdecydowana większość modeli, które drukujemy, to różne przyrządy i osprzęt”, mówi Kondek, który następnie wyjaśnia, w jaki sposób przyrządy są klasyfikowane w jego zakładzie. W Toyocie drukuje się:
- Przyrządy, które służą do potwierdzenia, że montowane części znajdują się we właściwych pozycjach względem siebie.
- Przyrządy montażowe, które służą do łatwiejszego, szybszego i powtarzalnego montażu różnych części.
- Narzędzia montażowe, które służą do wykonywania określonych zadań podczas montażu, takich jak nakładanie smarów na określone części śrub, przy pozostawieniu innych części bez smarowania.
- Uszczelnienia i osłony, które służą do zapobiegania przedostawaniu się drobnych części i innych przedmiotów do otworów technologicznych w częściach silnika podczas montażu oraz przenoszenia ich z jednego stanowiska roboczego na drugie.
„Oczywiście druk 3D w motoryzacji to nie jedyne rozwiązanie produkcyjne i często używamy różnych technologii do wykonania pojedynczego przyrządu lub narzędzia. Na przykład są części, które mają korpusy drukowane w 3D na maszynach Zortrax, ale punkty styku z metalowymi powierzchniami są wykonane w tradycyjny sposób z materiałów szczególnie odpornych na ścieranie. W ten sposób możemy zachować szybkość i opłacalność druku 3D oraz uzyskać najwyższą trwałość”, mówi Kondek. Poniżej znajdują się trzy wybrane przykłady przyrządów i narzędzi wydrukowanych w 3D w fabryce Toyoty.
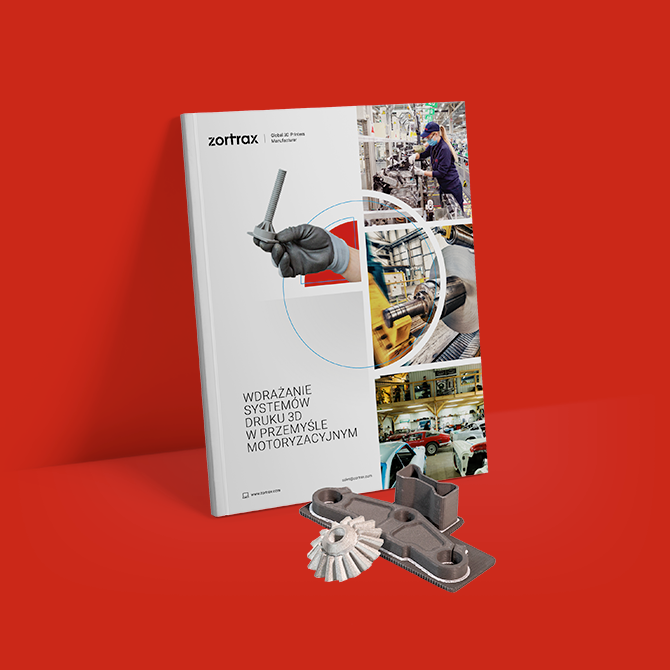
Poznaj rozwiązania druku 3D dla branży motoryzacyjnej
Pobierz darmowy ebookOsłony dźwigni zaworów
Kiedy silnik jest transportowany z jednego stanowiska montażowego na drugie, dźwignie zaworów silnika muszą być utrzymywane w jednym położeniu. Dlatego inżynierowie Toyoty używają specjalnie zaprojektowanych osłon, aby utrzymać te dźwignie w stałym położeniu. Po przybyciu na właściwe stanowisko, osłony montażowe są zdejmowane.
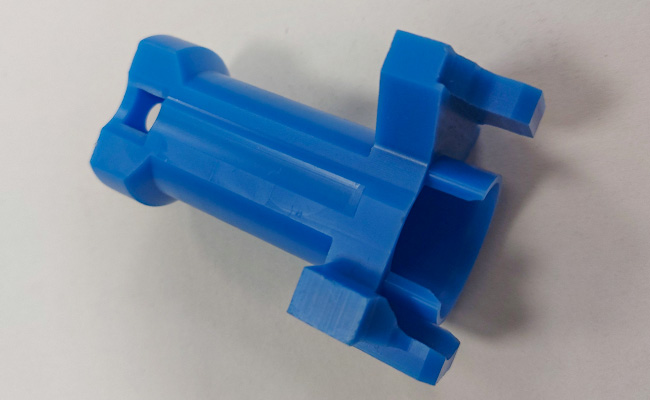
Prototyp osłony dźwigni zaworu wykonany w fabryce Toyoty na drukarce 3D Zortrax M300 Plus z filamentu Z-ABS.
„To świetny przykład tego, co można osiągnąć za pomocą druku 3D w motoryzacji”, mówi Kondek. Zespół inżynierów szybko wydrukował i sprawdził 12 różnych projektów tych osłon, aby zoptymalizować je pod względem geometrii i wagi. Podczas jednej zmiany, inżynierowie Toyoty mogli wykonać trzy różne zmiany geometrii i wydrukować w 3D dwie kolejne wersje tego przyrządu na drukarce 3D Zortrax M300 Plus.
„Osłony dźwigni zaworów pokazują przewagę technologii druku 3D w motoryzacji, jeśli chodzi o szybkie zmiany geometrii i wprowadzanie zmian konstrukcyjnych ad hoc.” – mówi Kondek.
Przyrządy do pozycjonowania drukowane w 3D
Inną kategorią przyrządów drukowanych przez Toyotę na Zortrax M300 Plus są przyrządy pozycjonujące. „Używamy ich na linii montażowej, aby potwierdzić prawidłowy montaż części”, mówi Kondek.
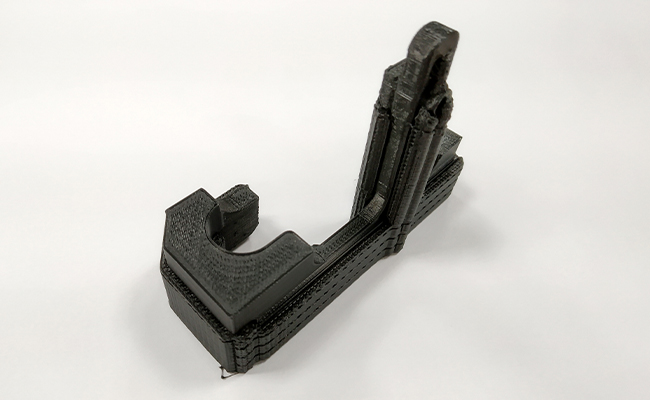
Przyrząd pozycjonujący wydrukowany w fabryce Toyoty na drukarce 3D Zortrax M300 Plus.
Główną zaletą używania takich narzędzi drukowanych w 3D jest ich zaskakująco długa żywotność i możliwość wykorzystania w projekcie innych technologii produkcyjnych.
W przedstawionym poniżej modelu CAD szare elementy zostały wykonane z metalu, a żółte wałki ze stali metodą CNC. Korpus części w kolorze czerwonym powstał na drukarce 3D Zortrax.
„Ciekawostką w tym konkretnym przyrządzie jest to, że został on dostarczony zespołom pracującym na linii montażowej jako prototypowa część testowa, która miała przejść dalsze poprawki” – mówi Kondek. Według niego na tym etapie procesu prototypowania korpus przyrządu w całości bazował na technologii druku 3D i brakowało w nim odpowiednich łożysk ślizgowych. Mimo to był używany codziennie przez pół roku, zanim się złamał.
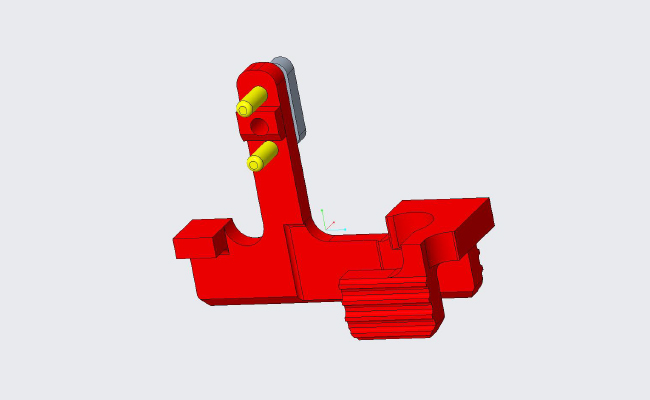
Projekt przyrządu pozycjonującego przeznaczonego do druku w fabryce Toyoty na drukarce 3D M300 Plus. Złożony przyrząd ma najbardziej narażone na zużycie części wykonane z nylonu (zaznaczone na projekcie kolorem żółtym).
„A kiedy do tego doszło, mogliśmy użyć tej samej drukarki 3D Zortrax M300 Plus do zapewnienia przyrządu zapasowego w zaledwie 7 godzin. Wymiana w takim tempie byłaby niemożliwa bez drukarek 3D” – podkreśla Kondek.
Prototypowanie dużych osłon
Osłona bloku silnika to element pokazujący bardziej zaawansowany sposób pracy z drukarkami. Docelowa osłona jest większa niż dostępna przestrzeń robocza drukarki. Co więcej, oddzielne drukarki 3D są używane do prototypowania i wytworzenia końcowego komponentu.
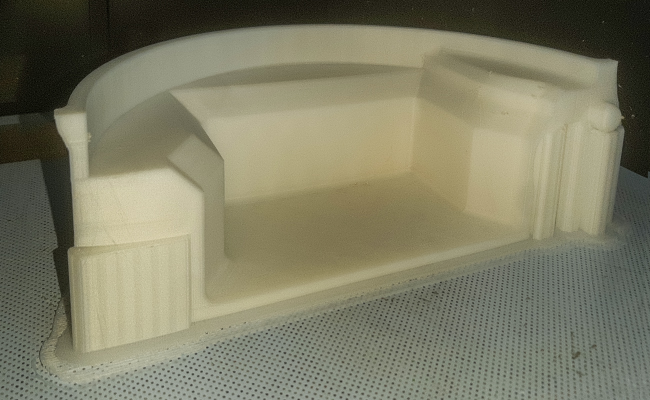
Część osłony silnika wydrukowane w fabryce Toyoty przed zdjęciem jej z platformy roboczej drukarki 3D dla motoryzacji – Zortrax M300 Plus.
„Zadaniem tego przyrządu jest uszczelnienie otworów technologicznych w bloku silnika podczas procesów montażowych. Zapobiega to przedostawaniu się ciał obcych w otwory technologiczne, co jest absolutnie krytyczne dla pracy silnika”, mówi Kondek.
Prototypy zostały wykonane na drukarce 3D Zortrax M300 Plus. Każdy z nich został wydrukowany w 3D z kilku części, które następnie zostały zmontowane. Korzystanie z M300 Plus było najbardziej opłacalnym sposobem dopracowania projektu i zbudowania wielu prototypów do kontroli geometrii.
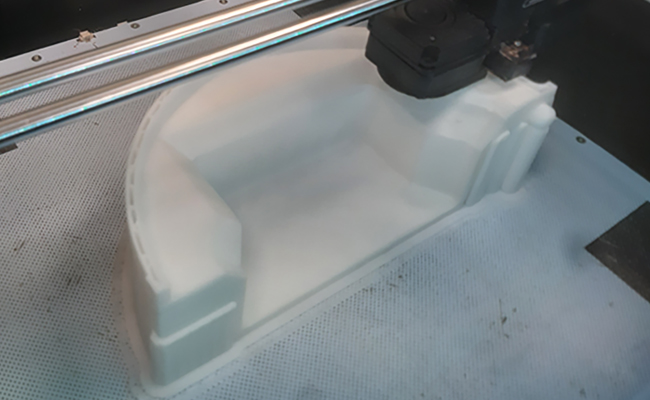
Osłona silnika jest zbyt duża by wydrukować ją w całości nawet na oferującej sporo przestrzeni roboczej drukarce Zortrax M300 Plus. Dlatego Toyota drukuje osłony w częściach i montuje je po zakończeniu druku.
Wreszcie, finalna osłona została wydrukowana w 3D na maszynie przemysłowej z wysokowydajnego materiału, którego M300 Plus nie obsługuje ze względu na otwartą architekturę. „Do takich zastosowań potrzebujemy większych drukarek 3D z zamkniętą architekturą, zapewniających stabilną temperaturę w komorze drukowania. To pozwala uniknąć wypaczania i kurczenia się modelu, co ma szczególne znaczenie przy dużych wydrukach”, mówi Kondek.
Oszczędność czasu i kosztów
„Używamy drukarek 3D w motoryzacji od dawna. Były już tutaj, kiedy trzy lata temu zacząłem pracę w Toyocie”, mówi Kondek. Twierdzi, że przyrządy, które są dziś drukowane w 3D, były kiedyś wykonywane przez oddzielny dział wyposażony w maszyny CNC i inne subtraktywne narzędzia produkcyjne. Wykonywanie bardziej wymagających projektów było po prostu zlecane zewnętrznym podwykonawcom.
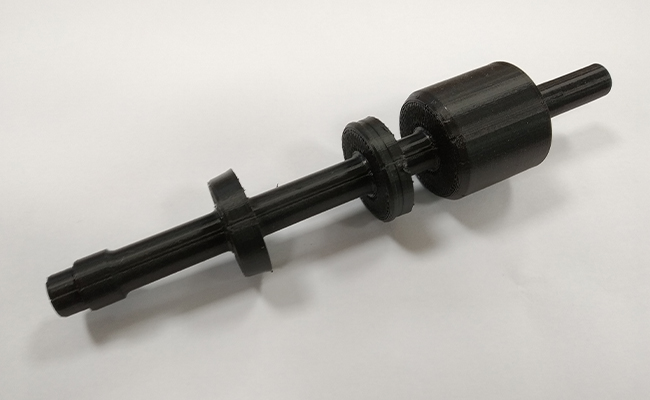
Część przyrządu do smarowania części motoryzacyjnych wydrukowane w fabryce Toyoty na drukarce Zortrax M300 Plus.
„Oczywiście korzystanie z takich narzędzi poważnie ograniczało nasze możliwości projektowe. Za każdym razem, gdy myśleliśmy o nowym przyrządzie, musieliśmy dwa razy zastanowić się, czy można go wyprodukować, czy nie. Drukarki 3D w motoryzacji rozwiązują ten problem”, wyjaśnia Kondek. Dodaje, że obecnie ponad 95% ze wszystkich druków w fabryce Toyoty powstaje w technologii LPD. Reszta jest również drukowana, ale przy użyciu innych technologii.
Jak twierdzi Kondek, cała inwestycja w sprzęt do druku 3D wykorzystywany w fabrykach Toyoty w Polsce zwróciła się w ciągu jednego roku. „W druku 3D nie chodzi tak bardzo o szybkość produkcji. Nie jest to najszybsza technologia na rynku, ale z pewnością jest najbardziej elastyczna. Nie musimy magazynować części zamiennych, ponieważ można je wydrukować w 3D na żądanie. Możemy optymalizować projekty w dowolny sposób, ponieważ drukarki 3D w motoryzacji są w stanie wyprodukować prawie wszystkie możliwe geometrie. W końcu, możemy rozpocząć drukowanie, kiedy tylko pojawi się taka potrzeba. Nie musimy czekać, aż dział narzędzi lub zewnętrzny podwykonawca będzie miał wolne moce przerobowe, by zająć się naszymi zleceniami. Czas oczekiwania na potrzebne oprzyrządowanie skrócił się z tygodni do dni, a czasem nawet godzin”, mówi Kondek.
Systemy druku 3D dla fabryk motoryzacyjnych
Drukarka 3D Zortrax M300 Plus używana obecnie przez Toyotę zapewnia możliwość podstawowego druku 3D do zastosowań produkcyjnych. Jednak w połączeniu z innymi rozwiązaniami Zortrax może działać jako element bardziej zaawansowanych systemów wytwarzania addytywnego. Poniżej kilka przykładów.
Dodanie urządzenia Zortrax Apoller do warsztatu druku 3D w fabryce umożliwia powtarzalne wygładzanie dużej liczby wydrukowanych przyrządów. Wygładzanie za pomocą oparów MEK lub acetonu sprawia, że drukowane modele są mniej przepuszczalne – stają się wodoodporne. Ta mocno ograniczona przepuszczalność ma kluczowe znaczenie przy wykonywaniu elementów, które napełnia się olejami lub innymi smarami. Apoller został zaprojektowany z myślą o dużej przepustowości, dlatego podczas jednej sesji wygładzania trwającej około 3 godzin jest w stanie wygładzić wiele różnych modeli. Posiada również certyfikat ATEX i może być bezpiecznie wdrażany na hali produkcyjnej.
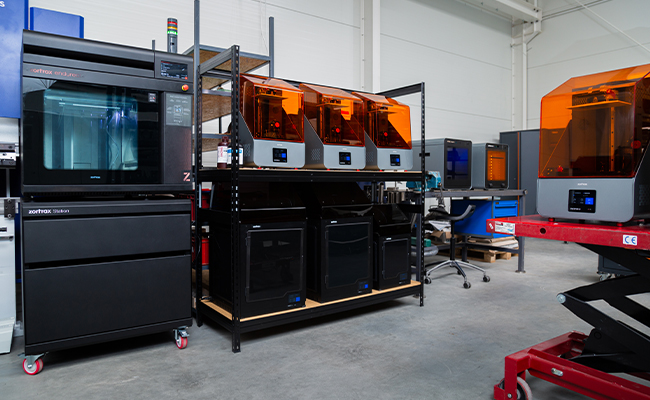
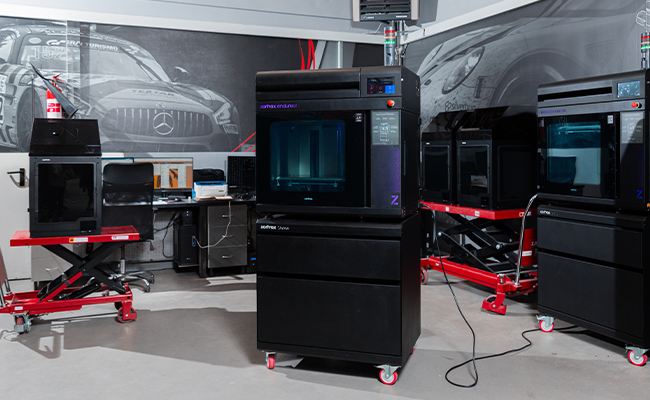
Standardowe filamenty polimerowe, takie jak ABS, mogą czasami okazać się zbyt słabe dla części przeznaczonych do pracy pod dużymi obciążeniami lub w bardzo wysokich temperaturach. Ten problem można rozwiązać za pomocą Zortrax Endureal, przemysłowej drukarki 3D dla motoryzacji, która została zaprojektowana do pracy z polimerami o wysokiej wydajności, takimi jak Z-PEEK czy VICTREX AM™ 200, które zachowują swoje właściwości w temperaturach przekraczających 300 stopni Celsjusza i osiągają wartości wytrzymałości na rozciąganie powyżej 90 MPa.
Wreszcie, gdy wymagania termiczne i mechaniczne danego projektu wykraczają daleko poza możliwości nawet najmocniejszych polimerów, Endureal może wytwarzać części ze stali. Konkretnie, Endureal jest kompatybilny z BASF Ultrafuse® 316L i BASF Ultrafuse® 17-4 PH, filamentami zawierającymi proszki metaliczne, które po dwuetapowej obróbce końcowej opracowanej przez BASF i przeprowadzanej przez Elnik Systems GmbH stają się pełnowartościową stalą nierdzewną 316L lub utwardzaną wydzieleniowo stalą 17-4. Materiały te są dostępne w ramach Zortrax Full Metal Package 316L i Zortrax Full Metal Package 17-4 PH, czyli zestawów zawierających wszystko, co niezbędne do wykonania części stalowych na drukarce 3D Zortrax Endureal.
Zapraszamy do kontaktu z naszym zespołem sprzedaży pod adresem sales@zortrax.com. Z przyjemnością polecą odpowiedni system druku 3D dla Twojej firmy.
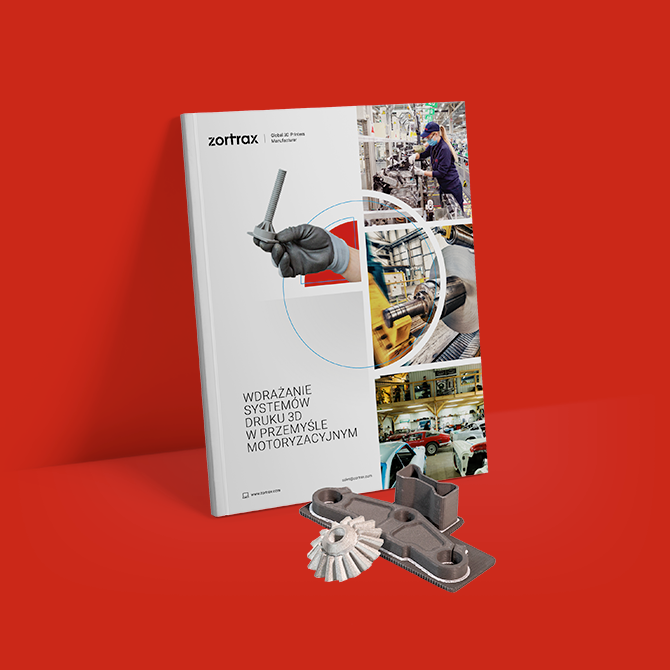