Sprzęt wydrukowany w 3D umożliwił francuskiemu biathloniście trening pomimo kontuzji
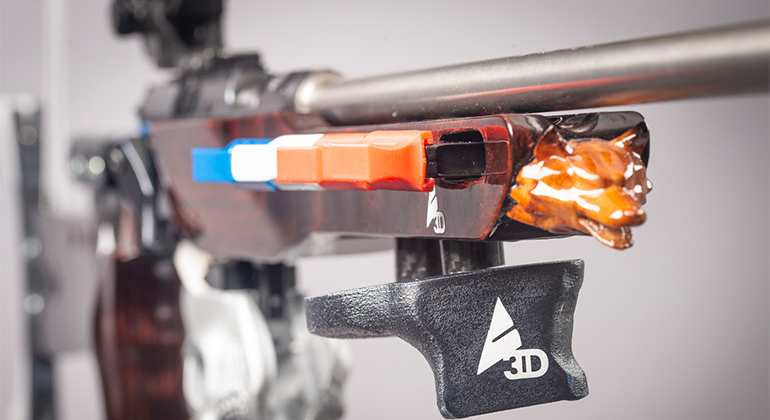
Jeden z najlepszych francuskich biathlonistów mógł trenować pomimo kontuzji nadgarstka dzięki spersonalizowanemu sprzętowi wydrukowanemu na drukarce 3D Zortrax M300 Dual z filamentu BASF Ultrafuse PP GF30.
Dlaczego sprzęt drukowany 3D ma znaczenie dla elitarnych sportowców
„W większości przypadków zawodowi sportowcy przychodzą do nas, ponieważ potrzebują sprzętu sportowego, który jest wykonany specjalnie dla nich, aby jeszcze bardziej poprawić swoje wyniki”, mówi Clement Jacquelin, szef i założyciel Athletics 3D, francuskiej firmy wykorzystującej drukarki 3D do budowy spersonalizowanego sprzętu sportowego.
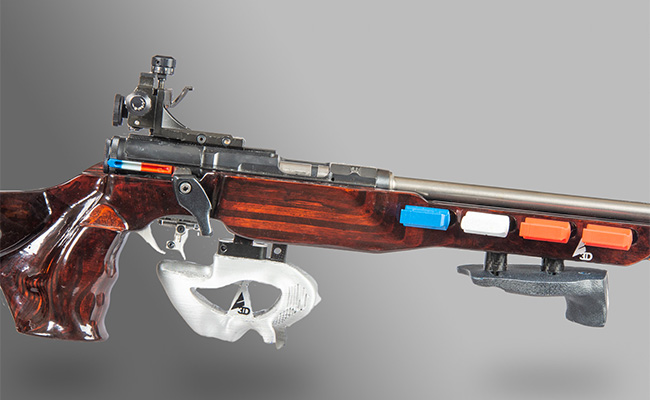
Profesjonalny karabin biathlonowy ze spersonalizowanym uchwytem pasa wydrukowanym z BASF Ultrafuse PP GF30 na drukarce 3D Zortrax M300 Dual.
Jednak w lipcu 2021 roku Athletics 3D musiało zmierzyć się z zupełnie innym wyzwaniem. Podczas zgrupowania francuskiej kadry narodowej w Norwegii jeden z najlepszych biathlonistów na świecie miał wypadek na rowerze szosowym. Upadł i uszkodził lewe ramię, które wyciągnął, aby zamortyzować upadek. Diagnoza w szpitalu, gdzie został natychmiast zabrany, wyglądała ponuro. Kości łokciowa i promieniowa uległy złamaniu.
Kości trzeba było chirurgicznie zabezpieczyć metalowym stabilizatorem. Oszacowano, że okres rekonwalescencji potrwa co najmniej kilka miesięcy, co nie wyglądało dobrze przed igrzyskami olimpijskimi. Aby mimo kontuzji możliwy był efektywny trening, Athletics 3D musiało zmodyfikować karabin biathlonisty.
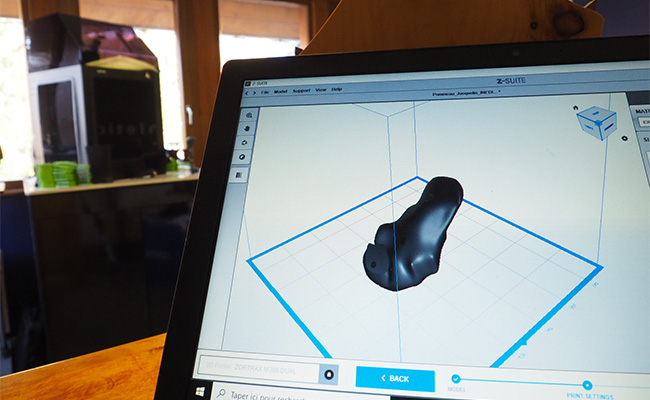
Cyfrowy model spersonalizowanego uchwytu pasa – wizualizacja w oprogramowaniu Z-SUITE przed rozpoczęciem druku 3D.
„Sprzęt sportowy wydrukowany w 3D można dostosować do ograniczonych ruchów, z którymi sportowiec musi sobie radzić w okresie rekonwalescencji po kontuzji. W tym przypadku nasz klient miał problem z supinacją przedramienia i bardzo ograniczoną mobilnością nadgarstka” – mówi Clement Jacquelin.
Przy takich ograniczeniach celowanie ze standardowego karabinu biathlonowego w pozycji leżącej było niemożliwe. Zamiast wstrzymać sesje strzeleckie na cały okres rekonwalescencji, francuska ekipa zdecydowała się na modyfikację broni.
Jak zmodyfikowano karabin
Celem projektu było umożliwienie biatloniście strzelania z ograniczonym kątem odchylenia nadgarstka. Aby to osiągnąć, zespół Athletics 3D zmodyfikował uchwyt do pasa, czyli część, w której pas jest przymocowany do dolnej części kolby karabinu.
Proces projektowania rozpoczął się od użycia skanera 3D firmy Zeiss do wykonania precyzyjnego cyfrowego modelu oryginalnego uchwytu. Gdy to zostało zrobione, zespół zaczął wprowadzać zmiany.
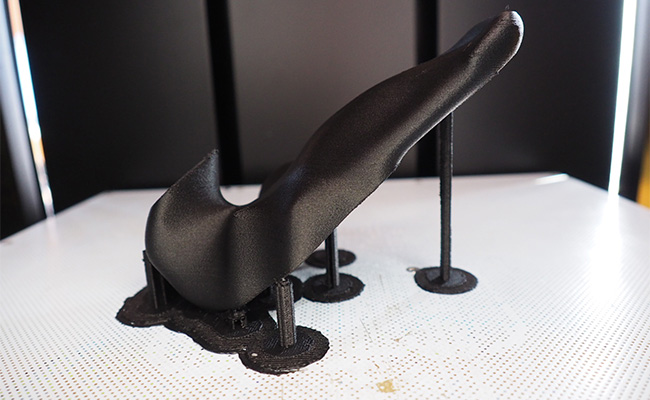
Uchwyt pasa został zmodyfikowany, aby zapewnić stabilność kontuzjowanej ręki podczas strzelania z pozycji leżącej. Model wydrukowany z BASF Ultrafuse PP GF30 tuż przed zdjęciem go z platformy roboczej drukarki 3D Zortrax M300 Dual.
„Pierwszą rzeczą, którą zmieniliśmy, był kąt, pod jakim można było trzymać uchwyt, aby umożliwić celowanie bez skręcania nadgarstka. W ten sposób rozwiązaliśmy problem ograniczonego kąta odchylenia nadgarstka. W drugim kroku zwiększyliśmy obszar kontaktu między uchwytem a dłonią, aby zapewnić większą stabilność. Ten krok był konieczny, ponieważ uzyskaliśmy pozycje, w której nasz klient wcześniej nie trenował”, wyjaśnia Clement Jacquelin.
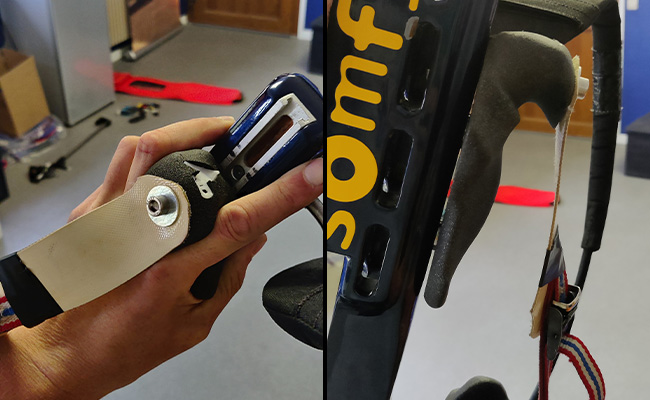
Wydrukowany uchwyt pasa został zmodyfikowany tak, aby umożliwić pewny chwyt bez rotacji nadgarstka.
Wyniki osiągnięte dzięki przeprojektowanemu, wydrukowanemu w 3D uchwytowi były, zważywszy na okoliczności, imponujące. Pierwszy trening strzelecki po wypadku miał miejsce już we wrześniu 2021 r. Poszkodowany biathlonista wrócił do strzelania w niecałe dwa miesiące. Inżynierowie Athletics 3D i trenerzy francuskiej drużyny stwierdzili, że strzały oddawane z nowym uchwytem były jeszcze bardziej precyzyjne niż przy użyciu standardowego. Spadła jednak szybkość strzelania.
Strzelanie z wydrukowanym w 3D ogranicznikiem dłoni było celniejsze, ale wymagało więcej czasu.
Dlaczego Athletics 3D wybrał BASF Ultrafuse PP GF30
Według Clementa Jacquelina wiele uwagi poświęcono doborowi odpowiedniego materiału na uchwyt. Oto dlaczego ostatecznie wybrano produkt z oferty BASF Forward AM.
„Nie mogliśmy po prostu użyć popularnych materiałów do druku, takich jak standardowy ABS czy PLA. Część musiała wytrzymać znaczne naprężenia, być odporna na uderzenia i mieć doskonałą jakość powierzchni. Samo to ograniczyło nasz wybór do zaledwie kilku materiałów. Wreszcie, tym, co naprawdę przechyliło szalę na korzyść BASF Ultrafuse PP GF30, była jego stabilność termiczna”, mówi Clement Jacquelin.
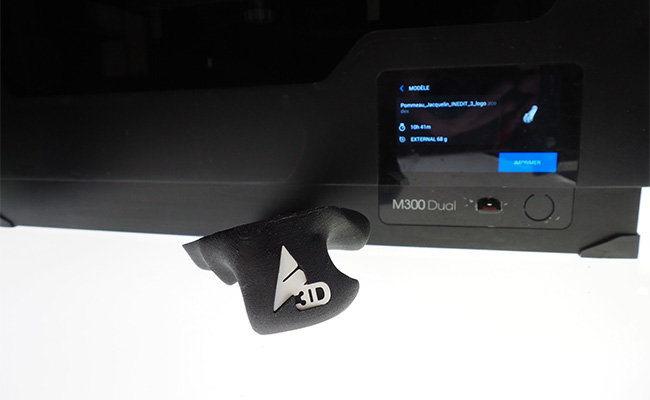
Modele wydrukowane z BASF Ultrafuse PP GF30 na drukarce Zortrax M300 Dual mają lekko chropowatą powierzchnię, dzięki czemu uchwyt pasa zapobiega wyślizgiwaniu się broni z ręki.
Stabilność termiczna oznaczała w tym przypadku zachowanie doskonałych właściwości mechanicznych w szerokim zakresie przeważnie niskich temperatur. Według Athletics 3D wyścigi biathlonowe, w zależności od lokalizacji, odbywają się w temperaturach sięgających -25 °C.
„Większość polimerów nie działa dobrze w tak niskich temperaturach. Materiały takie jak PLA czy nawet ABS stają się kruche podczas silnego mrozu. Dlatego francuscy trenerzy nalegali na wybór materiału, który sprawdzi się w niskich temperaturach. Dzięki BASF Ultrafuse PP GF30 nie mieliśmy z tym problemu. Materiał wykazał te same, doskonałe właściwości zarówno na mrozie, jak i w stosunkowo łagodnych temperaturach tuż poniżej 0°C”, twierdzi Clement Jacquelin.
Co wniosła drukarka 3D Zortrax M300 Dual
Po wybraniu odpowiedniego materiału firma Athletics 3D wykonała projekt na swojej drukarce 3D Zortrax M300 Dual, która korzystała z fabrycznie kalibrowanego profilu do pracy z BASF Ultrafuse PP GF30.
„Drukarki 3D często mają problemy z dokładnym odwzorowaniem nieregularnych, organicznych kształtów. Jakość druku w takich modelach pozwala od razu odróżnić przeciętne drukarki 3D od tych naprawdę dobrych. Ergonomiczne kształty, których używamy w naszym sprzęcie sportowym są zawsze trudne w realizacji. Do uzyskania odpowiednich rezultatów potrzebna jest wysoka precyzja drukarki. Dlatego wybraliśmy Zortrax M300 Dual”, mówi Jacquelin.
Według niego były dwa główne powody wyboru Zortrax M300 Dual do tego projektu.
- M300 Dual to maszyna wyposażona w technologię podwójnej ekstruzji. Może drukować rozpuszczalne struktury podporowe, które można usunąć z drukowanej części bez uszkadzania powierzchni.
- Oprogramowanie Z-SUITE zawiera predefiniowane profile drukowania dla obsługiwanych materiałów, co oznacza, że wszystkie ustawienia dla filamentu BASF Ultrafuse PP GF30 zostały dokładnie przetestowane przez inżynierów Zortrax.
„To przełożyło się na doskonałe drukowane części. Co więcej, oznaczało to również, że mogliśmy spodziewać się powtarzalnych wyników, gdyby potrzebne były zapasowe uchwyty”, twierdzi Clement Jacquelin.
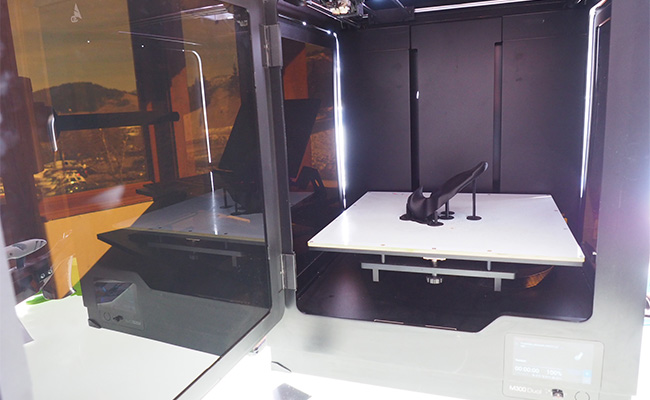
Drukarka 3D Zortrax M300 Dual pracując z osłonami bocznymi oraz urządzeniem HEPA Cover zapewnia stabilną temperaturę w komorze druku, co przekłada się na wysoką, powtarzalną jakość wydruków z BASF Ultrafuse PP GF30.
Sesje treningowe z uchwytem wydrukowanym w 3D rozpoczęły się we wrześniu i trwały do końca grudnia 2021 roku. Gdy w nadgarstku przywrócono pełną mobilność, zespół postanowił jednak wrócić do standardowego uchwytu.
„Głównym powodem było to, że trenerzy wraz z naszym klientem uznali, że zwiększona celność nie zrekompensuje wolniejszego tempa strzelania. Celem projektu było jednak stworzenie rozwiązania pozwalającego ograniczyć wynikającą z kontuzji przerwę w treningach. Powrót do strzelania i rywalizacji w wyścigach Pucharu Świata był dzięki naszej pracy możliwy co najmniej dwa miesiące wcześniej”, mówi Clement Jacquelin.