Zortrax wspiera budowę respiratora open-source we Włoszech
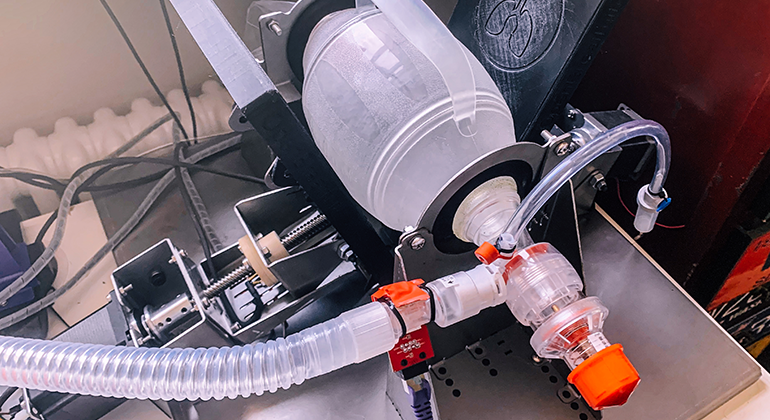
Open Breath to projekt stworzony przez zespół włoskich inżynierów z Turynu, mający na celu zbudowanie w pełni funkcjonalnego, szpitalnego respiratora. „Nie próbujemy zbudować zautomatyzowanej torby resuscytacyjnej. Budujemy w pełni profesjonalne urządzenie medyczne, ze wszystkimi niezbędnymi czujnikami i obsługą wielu zaawansowanych trybów pracy dostępny w respiratorach komercyjnych. Taki sprzęt jest zdolny do wentylowania pacjenta przez około miesiąc, bez przerwy, co jest często konieczne przy bardziej zaawansowanych przypadkach COVID-19”, mówi Simone Iannucci, jeden z założycieli Open Breath. Zortrax, w ramach wsparcia dla projektu, przekazał inżynierom zaawansowaną, wielkoformatową drukarkę M300 Dual działającą w technologii LPD Plus oraz niezbędne materiały do druku.
Niedostępne części
„Obecnie wygląda na to, że jesteśmy we Włoszech nieco za szczytem pandemii COVID-19”, mówi Iannucci. Statystyki potwierdzają jego słowa. Do tej pory, pandemia pochłonęła w Italii ponad 24 tysiące ofiar, a liczba nowych zachorowań potwierdzanych każdego dnia oscyluje wokół 3 tysięcy. „Dlatego nie możemy sobie pozwolić na stratę nawet jednego dnia. Druk 3D pozwala nam oszczędzić czas”, dodaje.
Niestety projekt Open Breath w ostatnich tygodniach zmagał się z opóźnieniami. Respirator, początkowo, miał być wykonany z blachy. Bardziej skomplikowane części miały być frezowane ze stali. „Ale pandemia rozwinęła się do punktu, w którym rząd zdecydował się na drastyczne ograniczenie funkcjonowania gospodarki, aby ludzie pozostali w domach. Firmy, które miały dostarczyć nam części i materiały, zostały z dnia na dzień zamknięte”, wyjaśnia Iannucci.Według niego, frezowanie CNC, jako technologia produkcji, zaczęła opóźniać prace, ponieważ części trzeba było zamawiać, a następnie oczekiwać przez co najmniej kilka dni aż zostaną dostarczone do warsztatu, w którym zespół montował pierwszy prototyp. „Wtedy Massimiliano D’Amario, inżynier z wielkim doświadczeniem w technologiach produkcji addytywnej, który pracował z nami od początku, zaproponował wykorzystanie druku 3D. Po prostu zaczęliśmy drukować wszystkie części, jakie wstępnie miały być frezowane. Zaoszczędziliśmy na tym mnóstwo czasu”, mówi Iannucci. Ten czas został wykorzystany na udoskonalanie samego urządzenia.
Projektowanie respiratora
Respirator, który budują inżynierowie z Open Breath, to zaawansowany, skomplikowany sprzęt. Musi taki być, aby spełniał swoją funkcję. „Jest wiele innych zespołów, które próbują budować respiratory poprzez automatyzację torby resuscytacyjnej”, mówi Iannucci. Taka torba to proste, obsługiwane ręcznie urządzenie do wentylacji będące standardowym wyposażeniem karetki pogotowia. „Przy odrobinie inwencji można ją zautomatyzować przez podłączenie jej do silniczka od wycieraczek samochodowych. Ale lekarze, z którymi na ten temat rozmawialiśmy, zapewnili nas, że takie urządzenie mogłoby działać tylko przez kilka godzin”, twierdzi inżynier.Dlatego respirator Open Breath ma zapewniać bardziej zaawansowane funkcjonalności. Przykładowo, lekarzy mogą za jego pomocą precyzyjnie kontrolować tempo pompowania i ciśnienie trafiającego do płuc pacjenta powietrza. Zespół uwzględnił też możliwość pracy w trybie SIMV (synchronizowanej przerywanej wentylacji obowiązkowej), który przyzwyczaja pacjenta do samodzielnego oddychania przed planowanym odłączeniem od urządzenia.
„Patrząc z medycznego punktu widzenia, ten tryb jest niezwykle ważny ponieważ celem terapii jest umożliwienie pacjentom samodzielnego funkcjonowania, bez aparatury sztucznie podtrzymującej funkcje życiowe”, wyjaśnia Iannucci. Szczegółowe parametry pracy respiratora mogą być też ustawiane zdalnie, aby ograniczyć czas jaki lekarz musi spędzić przy łóżku pacjenta.Aby to wszystko stało się możliwe, zespół Open Breath musiał zaprojektować cały urządzenie od początku, poczynając od sprzętu, a kończąc na systemach kontroli i algorytmach zapewniających samodzielną pracę. „To było ogromne wyzwanie, ale otrzymaliśmy ogromne wsparcie ze strony firm i uniwersytetów. Swój wkład w ten projekt mieli nawet inżynierowie, którzy na codzień pracują w instytucie CERN w Genewie. Ludzie z CERN okazali się ogromnie pomocni. Mogliśmy liczyć na największe umysły na Ziemi”, mówi Iannucci. Przy tym wszystkim, respirator miał pozostać prosty w produkcji, montażu i obsłudze.
Przewaga podwójnej ekstruzji
Drukarka Zortrax M300 Dual, którą zespół Open Breath otrzymał w ramach wsparcia od Zortrax, to urządzenie o dużym polu roboczym zdolne pracować naprzemiennie z dwoma materiałami: jednym, z którego powstaje model i drugim, z którego powstają rozpuszczalne w wodzie struktury podporowe. Brak konieczności mechanicznego usuwania podpór sprawia, że M300 Dual jest w stanie drukować względnie duże części o bardzo złożonej geometrii. Obie te cechy okazały się w projekcie Open Breath istotne.„Projekt Open Breath rozdzielił się na dwa warianty. Pierwszy, ten nad którym pracowaliśmy od początku, zakłada wykorzystanie części stalowych. W tym wariancie, wykorzystujemy drukarki 3D w ich najbardziej tradycyjnej roli, czyli jako narzędzie do szybkiego prototypowania”, mówi Massimiliano D’Amario, inżynier Open Breath odpowiedzialny za obsługę drukarek 3D. Jednak kiedy pozyskanie metalowych części zaczęło stawać się coraz bardziej problematyczne, D’Amario doszedł do wniosku, że problem da się obejść produkując na drukarkach docelowe części, a nie tylko prototypy.
„Oczywiście, przestawienie się na druk 3D wymagało wprowadzenia pewnych zmian w projekcie. Dlatego dzisiaj, prace nad dwoma wariantami”, mówi D’Amario. W wariancie przystosowanym do druku 3D, na drukarkach Zortrax wykonane są m.in. obudowy silników i części elektronicznych. W obu tych zastosowaniach wydrukowana część pracuje jako izolator oraz konstrukcja pochłaniająca drgania. „W takich wypadkach podwójna-ekstruzja jest nieoceniona w połączeniu z dużym polem roboczym”, twierdzi D’Amario. „Drukowane przez nas części przekraczają rozmiarami obszar pola roboczego w mojej własnej drukarce Zortrax M200. Używanie mniejszej drukarki wymusiłoby zmiany w projekcie, których chcieliśmy uniknąć. Komponenty musiałyby być drukowane w dwóch częściach z uwzględnieniem elementów ułatwiających ich późniejszy montaż”.Jednak M300 Dual zapewnia znacznie więcej niż tylko duży pole robocze. „Drukujemy części, które mają zaawansowaną architekturę wewnętrzną. To oznacza, że są w nich trudno dostępne punkty, z których nie moglibyśmy usunąć standardowych podpór. Specjalny, rozpuszczalny w wodzie materiał podporowy rozwiązuje ten problem. Płukanie wydrukowanego komponentu w wodzie usuwa podpory z miejsc, do których nie moglibyśmy sięgnąć narzędziami bez uszkodzenia całej konstrukcji”, wyjaśnia D’Amario. Jego zdaniem, części drukowane na M300 Dual są bardziej precyzyjne i wytrzymałe niż ich odpowiedniki drukowane na mniejszej drukarce działającej w trybie w pojedynczej ekstruzji.
Wyścig z czasem
„To naprawdę wojna. Lekarze i pielęgniarki w całych Włoszech walczą na pierwszej linii i ponoszą ciężkie straty”, mówi Iannucci. „Dlatego nie ma czasu do stracenia. Staramy się jak najszybciej udostępnić nasz sprzęt. Przez kilka ostatnich tygodni pracowaliśmy prawie 24 godziny na dobę. Zaczynamy być naprawdę zmęczeni”, dodaje.
Obecnie, zespół Open Breath ma w pełni złożone prototypy respiratorów w obu wariantach: z częściami stalowymi oraz ten przystosowany do wykonania w technologii druku 3D. Cały czas trwają ostatnie testy sprawdzające, czy urządzenie działa poprawnie w bardziej zaawansowanych trybach pracy takich jak SIMV. Jak wszystko pójdzie dobrze, projekt zostanie każdemu udostępniony za darmo.„Nawet jeśli nasza praca nie pomoże Włochom, na pewno skorzystają na niej inne, dotknięte pandemią kraje. Najważniejsze jest jednak chronienie, za wszelką cenę, personelu medycznego. Jeśli zabraknie lekarzy i pielęgniarek, możemy mieć całą masę respiratorów. Bez wykwalifikowanych ludzi, żaden sprzęt nie spełni swojej roli”, podkreśla Iannucci.