Produkcja seryjna lamp w australijskim LimeLite przy użyciu farmy 30 drukarek 3D
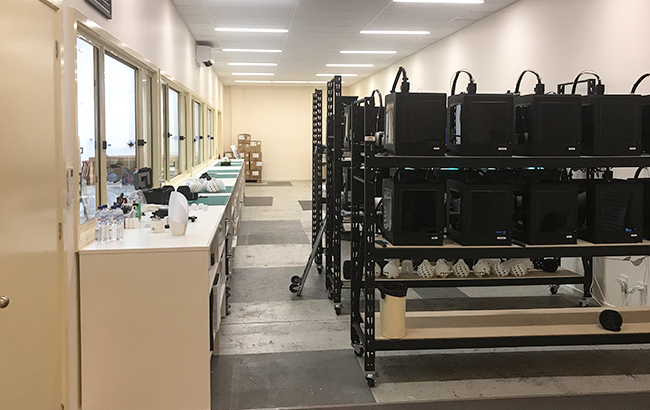
Technologie przyrostowe zostały powołane do życia jako metoda pozwalająca na dużo szybsze i tańsze wykonywanie prototypów nowych produktów. Dzięki drukarkom 3D przyspieszono prace koncepcyjne, skrócono testy, zoptymalizowano procesy produkcyjne. Chociaż nie zdajemy sobie z tego sprawy, druk 3D od wielu lat towarzyszy powstawaniu rzeczy, których używamy w codziennym życiu.
Równocześnie technologia druku 3D bardzo mocno ewoluowała na przestrzeni ostatnich lat. Drukarki 3D stały się szybsze, bardziej precyzyjne, a praca z nimi powtarzalna. Wraz z postępem technologicznym, technologie addytywne coraz częściej zaczęły być wykorzystywane w produkcji niskoseryjnej, tworząc finalne, gotowe produkty. Zortrax – jeden z europejskich liderów druku 3D, z powodzeniem wdraża swoje drukarki 3D w różnych gałęziach przemysłu. Najnowszym przykładem może być tutaj współpraca z australijską firmą LimeLite, która na potrzeby szybkiego prototypowania oraz produkcji seryjnej gotowych produktów, stowrzyła farmę 30 drukarek 3D, złożonych z modeli Zortrax M200 i M200 Plus.
LimeLite działa w branży oświetleniowej od 23 lat, specjalizując się w produkcji lamp oraz asortymentu oświetleniowego. W poszukiwaniu sposobów na obniżenie kosztów produkcji oraz optymalizacji procesów produkcyjnych, inżynierowie firmy zaczęli wpierw eksperymentować, a później wdrażać technologie przyrostowe. Drukarki 3D pozwoliły nie tylko zrezygnować w wybranych obszarach z formowania wtryskowego (proces wytrysku jest bardzo wydajny, ale wiąże się z produkcją bardzo kosztownych form, które z czasem ulegają zużyciu), ale pozwoliły także na tworzenie zupełnie nowych modeli lamp o spersonalizowanych kształtach i wzorach, dostosowanych do indywidualnych potrzeb klienta.
Naturalną konsekwencją zmiany podejścia do projektowania nowych produktów (możliwość tworzenia krótkich serii produkcyjnych, lub całkowicie indywidualnych i jednostkowych lamp), było uruchomienie nowego systemu produkcji lamp, będących spójnym dopełnieniem designu pomieszczeń klientów. Został on oparty o drukarki 3D drukujące w technologii FFF z termoplastów w formie żyłki. Wybór inżynierów LimeLite padł na urządzenia Zortrax – flagowe modele M200 i M200 Plus, z których stworzono farmę liczącą 30 urządzeń .
Jak oszacowali specjaliści LimeLite, czas produkcji nowych produktów za pomocą farmy Zortrax został diametralnie skrócony. Aktualnie wyrób nowej lampy – począwszy od szkicu do gotowego egzemplarza skrócił się nawet do trzech dni! Z kolei praca wszystkich 30 drukarek 3D pozwala na jednoczesne wykonywanie elementów nawet do kilkudziesięciu produktów na raz, co w pełni spełnia oczekiwania producenta. Dodatkową korzyścią jest skala produkcji dostosowana pod konkretne zamówienie co sprawia, że LimeLite nie musi borykać się z kosztami magazynowania swoich produktów.
W nowym systemie wszystko zaczyna się od klienta i jego wizji nowego produktu. Wystarczy zaledwie szkic, na bazie którego projektanci LimeLite przygotowują model 3D. Następnie jest on drukowany na drukarkach 3D Zortrax i przechodzi kolejne etapy konsultacji i testów. Gdy klient skończy nanosić poprawki i zmiany, model trafia do produkcji. Co ciekawe – powstaje dokładnie w ten sam sposób i na tych samych maszynach co pierwszy prototyp. Teoretycznie możliwa jest sytuacja, że już pierwszy prototyp jest finalnym modelem.
Pierwszą kolekcją powstałą przy użyciu farmy drukarek 3D Zortrax było “On track”. Do tej pory LimeLite stworzyło już trzy kolekcje lamp wyprodukowanych w ten sposób. Firma jest bardzo zadowolona z jakości wydruków realizowanych na M200 i M200 Plus, wskazując, że produkowane detale nie wymagają żadnych dodatkowych czynności z zakresu post-processingu. Producent planuje rozszerzenie farmy o kolejne drukarki 3D, gdyż produkowane na indywidualne zamówienia lampy cieszą się rosnącą popularnością, a ich ceny są niższe, niż w przypadku produktów powstałych z wykorzystaniem tradycyjnych metod wytwórczych.