A small automotive workshop can benefit from a simple 3D printing configuration. To produce unavailable or one-off custom parts, the setup may include Zortrax M300 Plus or Zortrax M300 Dual 3D printers. Both machines support large-scale 3D printing with the most popular filaments, such as ABS, HIPS, PETG or NYLON. ABS and HIPS are best for economical prototypes, frames, dashboard parts, or decorative elements. PETG and NYLON, on the other hand, can be used to 3D print parts that require slightly more durability and resistance to temperatures and chemicals.
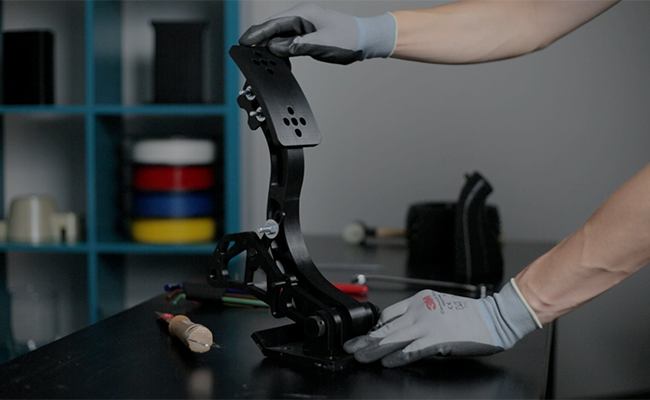
A gas pedal prototype 3D printed in Zortrax M300 Plus with Z-NYLON.

A gas pedal prototype 3D printed in Zortrax M300 Plus with Z-NYLON.
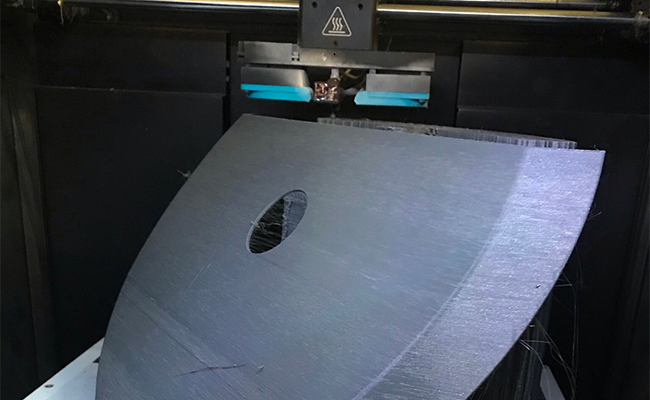
A scooter front wheel cover 3D printed on Zortrax M300 Plus 3D printer.
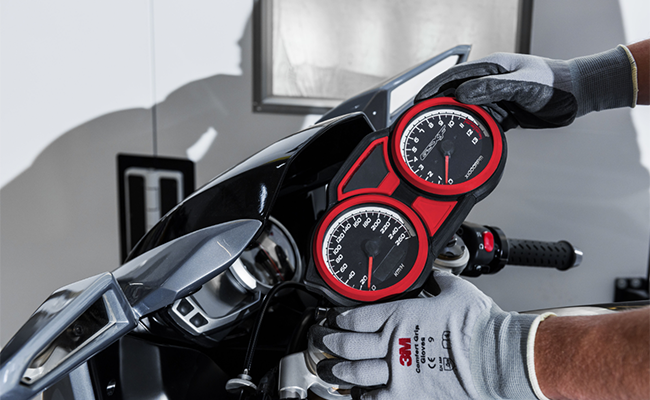
3D printed prototypes of a speedometer frames for a motorcycle.
What’s more, Zortrax M300 Dual 3D printer allows an automotive workshop to go for even more technical filaments. BASF Ultrafuse® PP GF30 and BASF Ultrafuse® PAHT CF15 materials are reinforced with glass fiber (PPGF 30) and micro-carbon fibers (PAHT CF15), which make them a perfect fit for prototypes tested in harsh conditions or end-use parts working in unfavorable environments close to heat, UV light, or chemicals. Both machines can, in fact, 3D print with a wide range of filaments and you can freely adjust the printing settings in Z-SUITE, the free software which comes with each Zortrax printer.
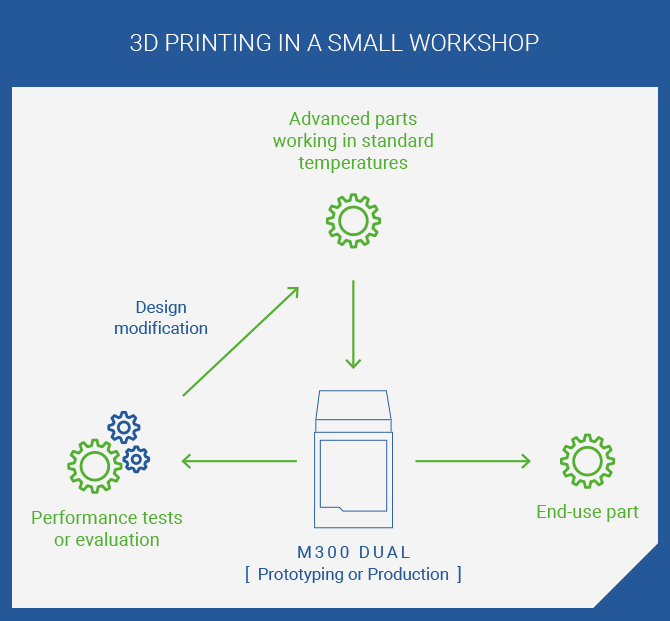
Recommended 3D Printing Cluster Configurations for Large Automakers
For large automakers, additive manufacturing technologies can cover almost all stages of product development. A majority of automotive facilities, from design studios to R&D centers worldwide, employ 3D printing equipment on a day-to-day basis.
Design and Prototyping
Before a new vehicle reaches the production level, a basic hardware configuration, consisting of Zortrax M300 Plus or M300 Dual, allows the engineering teams to quickly test ergonomics, mechanical properties, or performance of engine components, suspension structures, chassis, or dashboard elements. The design team can implement their ideas and test multiple iterations before the final project has been validated and refined. With the Z-SUITE slicer, which leaves plenty of room to conveniently adjust the settings to a specific project, the extensive prototyping stage is further enhanced. We discussed the importance of 3D printing during new vehicle’s development in the article: Why Modern Car Designers Use 3D Printers.
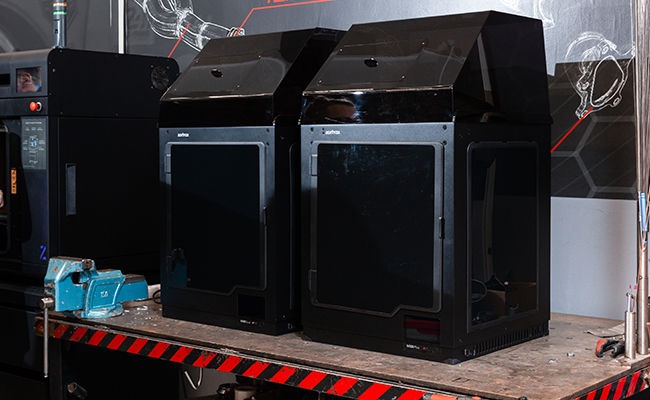
Zortrax M300 Plus 3D printers working in a large automaker.
Manufacturing
During the ongoing work in an automotive factory, the same machines can produce custom tooling, such as positioning jigs, seals, and covers, required in highly specific manufacturing processes on production lines. A very good example of how such tools improve the work on assembling car engines on a daily basis is Toyota’s factory in Poland, which we covered in the article: How Toyota Factory Works with Zortrax 3D Printers. The engineers are able to make necessary design adjustments in 3D printed parts without the need to build specialized molds or outsource this work to an external company.
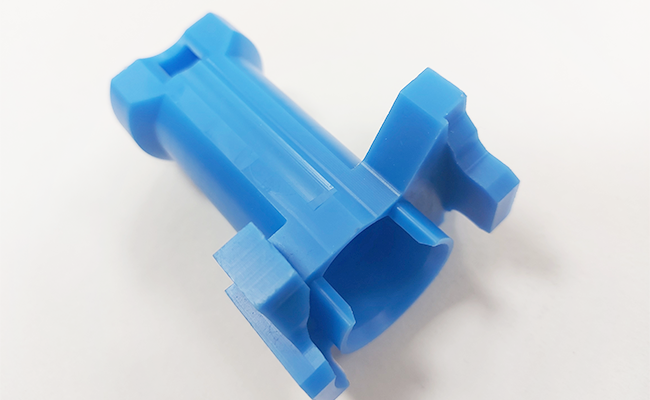
3D printed engine valve lever cover custom-designed for an assembly line in Toyota factory in Poland.
In addition, introducing 3D printers in a manufacturing plant is a way of flexibly responding to problems that cannot be predicted in advance. New tools or special covers can be designed and 3D printed on the spot. What’s more, some post-processing procedures extend the lifespan of such 3D printed tools. For this purpose, they can be smoothed in the Zortrax Apoller device and thus become watertight and less prone to damage. All of this enables the factory to maintain the workflow and speed of manufacturing, while keeping relatively low operating costs.
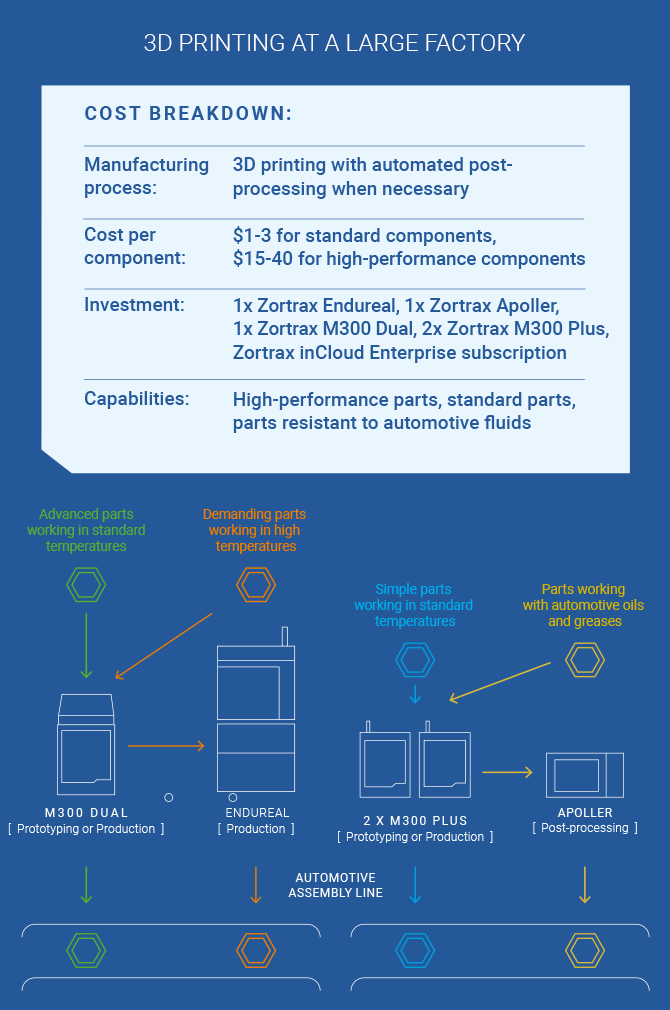
By adding the Zortrax Endureal 3D printer to the machine park in an automotive factory, the same flexibility of 3D printing can be sustained when working on high-performance parts with more demanding applications. The Endureal can produce end-use shock resistant mounts, heavy-duty gears, components working with automotive fluids, or parts intended to operate in areas with elevated fire risks.

An example 3D printing configuration in an automotive factory, consisting of desktop 3D printers – Zortrax M300 Plus and M300 Dual, and an industrial 3D printer – Zortrax Endureal.
After prototyping with more economical filaments, the target parts can be made from high-class engineering materials, such as Z-PEEK, Z-PEI 9085, VICTREX AM™ 200, and metallic powder filaments that can be processed into fully functional steel — BASF Ultrafuse® 316L and BASF Ultrafuse® 17-4 PH.

3D printed metal part during standard polishing.
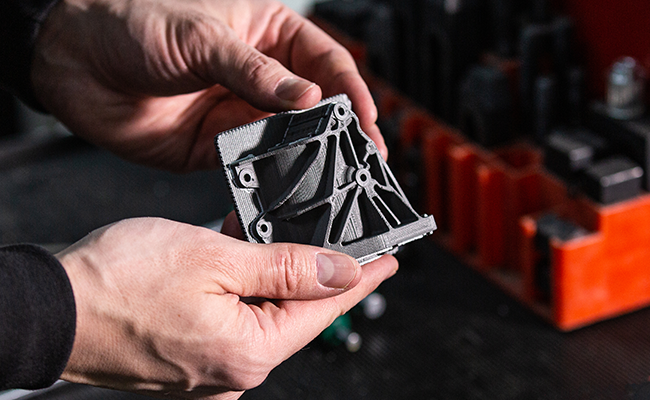
A sleeve cover 3D printed with BASF Ultrafuse® 17-4 PH metallic filament.
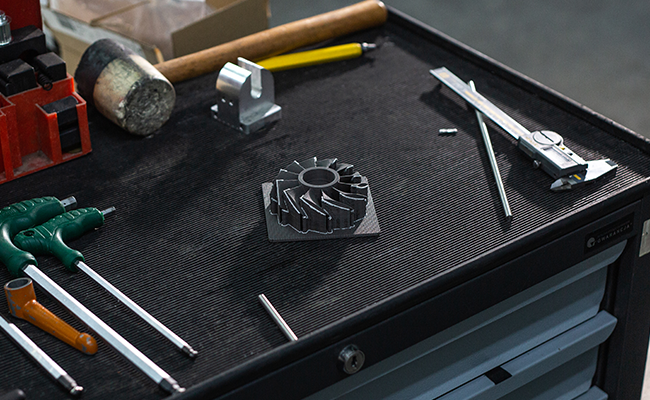
A turbine rotor prototype 3D printed on Zortrax Endureal using BASF Ultrafuse® 316L metallic filament.
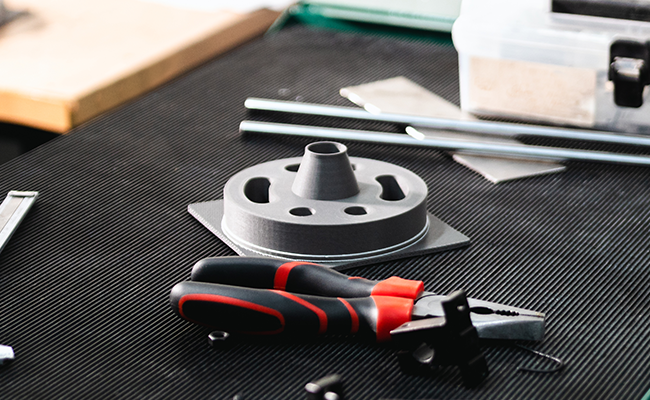
A steel part 3D printed with a metal filament for the automotive industry.
Other group of parts that can be incorporated on assembly lines to perform specific tasks in automotive can be produced with photopolymer resins on a UV LCD 3D printer. Zortrax Inkspire 2 works with a variety of resins with different properties such as transparency or flexibility. It is possible to 3D print, for example, highly precise, transparent covers that function as protection, and at the same time, provide the engineers with a clear view of a component’s interior.
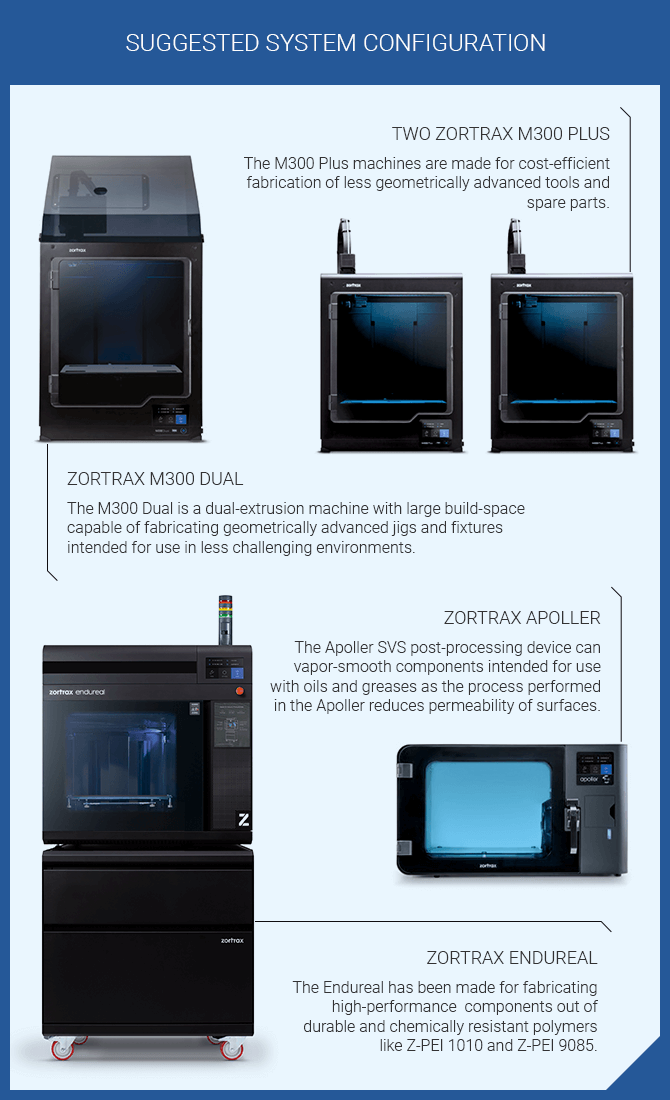
3D Printing Farm Management
The 3D printing setup can be run by the factory’s maintenance department and deliver components for multiple workstations. Even though the automotive factory is usually a large area, its employees can manage the 3D printing processes from any place in the facility thanks to Zortrax inCloud. It is a system based on a cloud which gives the staff access to 3D printers and the possibility to start the printing process remotely. Whenever the assembly line supervisors notice that a crucial 3D printed jig or cover may soon be worn out, they can choose the proper file from the online folder and send a command to the printer to start production. A 3D printing farm with a few desktop and industrial machines allows the engineers to independently make elements that would have to be outsourced, and in turn, suspend further production.
Learn more about the impact of additive manufacturing technologies on the entire automotive sector. Go to the article 7 Examples of 3D Printing Applications in Automotive Industry to see the real-life designs from both small workshops and large factories.
Don’t hesitate to contact us at sales@zortrax.com for assistance in building a 3D printing setup in your automotive company.