3D Printed Scale Models for Naval Industries
All aboard
Welcome to the busy harbour of La Spezia, where Italian company Superfici operates. It specializes in 3D printing high quality scale models for naval industry. Comapny was founded in 2016, by two yacht designers (Paolo Nazzaro and Davide Telleschi) and yacht engineer (Guido Zannoni). Although all of them got an industrial and transportation background, they had none previous experience with 3D printing. Their aim was to simply give life to their projects and ideas.
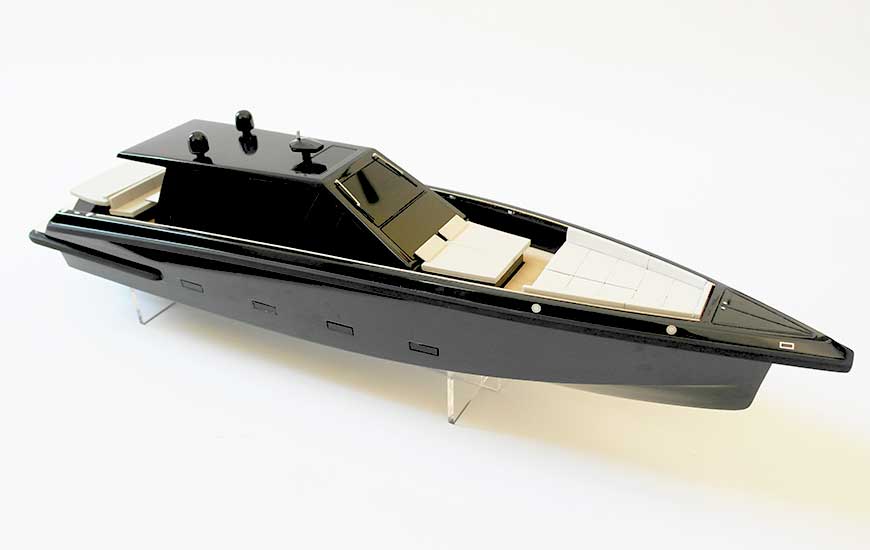
Yacht model 3D printed by Superfici
Their journey stared with local designers looking for basic models for conceptual stages. Later, clients realized 3D printing offers them more than shaped shell, so they asked for detailed models, which could be presented to end-customers. As they confirm themselves, at first it wasn’t obvious how to efficiently 3D print such objects, but in the end, the learning curve wasn’t too steep for the team. Keeping in mind required detail level and high demands of their clients, Superfici had to introduce a member to their team. They were looking for a precise device, which could print with wide range of materials. Moreover, they needed a reliable tool, one with complete control over printing parameters. Zortrax M200 satisfied and keeps satisfying their needs ever since.
Idea worth sharing
What’s striking about their approach to the 3D printing is how practically they look at the matter. It’s not enough that you can use the device to recreate existing object. They’d like to rely exclusively on 3D printing as a medium of their ideas, so other methods would become obsolete. The revolution is on its way, as they say, currently trying to reinvent design and production process to make it exclusive for AM devices. Italian team understands perfectly, that they cannot change the situation by themselves, so they are actively spreading the word about 3D printing. Luckily, company is located in La Spezia, Italy – city known for its ties with naval industry.
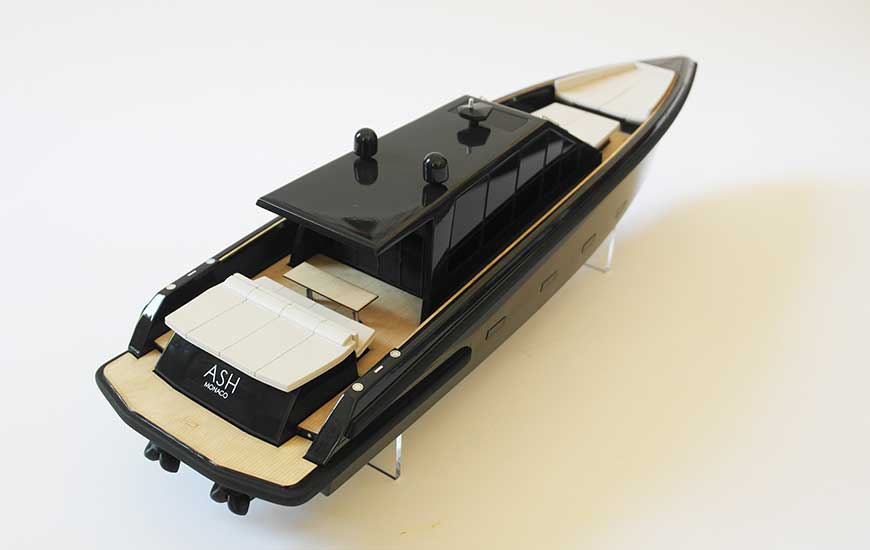
Back view of the 3D printed yacht model
The main aim of Superfici is to introduce the additive manufacturing technology to the yacht building industry. Therefore, making yacht scale models for local shipyards and naval architects is just the beginning. This is the best way to showcase advantages of 3D printing, because the models are done quickly, they are lightweight, yet durable, but most importantly, they catch client’s eye. High local demand for cost-effective rapid prototyping method facilities even greater interest. Additionally, Superfici offers its services and guidance to small local companies. They’ve also opened many collaborations with universities and high schools. Everything to spread the word about 3D printing and its capabilities.
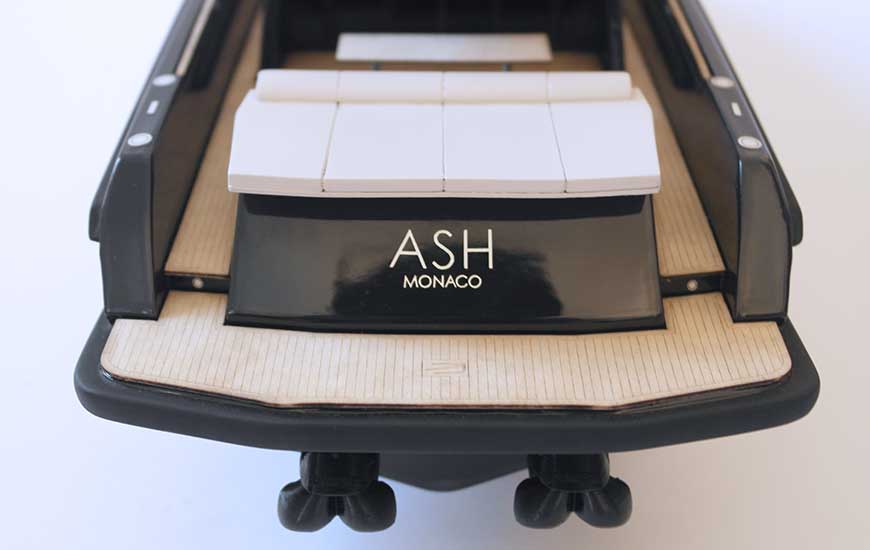
Details of the model
Uncharted waters
Team is mostly focused on the prototyping for naval industry, but they are also testing 3D printing in other fields. For example, by constructing temporary parts casted in molds for FRP yachts. Those elements need to be light, smooth, possibly with metallic thread insertions. Their particular shapes, which are hard to obtain with traditional technologies, can be easily 3D printed. The 3D printed part is lighter compared to wood and cheaper than machined foam. Moreover, the polymerization process requires a material which can withstand 60-70°C with no deformation, hence the choice of Z-ABS and the other Zortrax Materials, to suit perfectly this kind of applications. Superfici is also providing shipyards with non-structural parts for yacht’s interior and exterior.
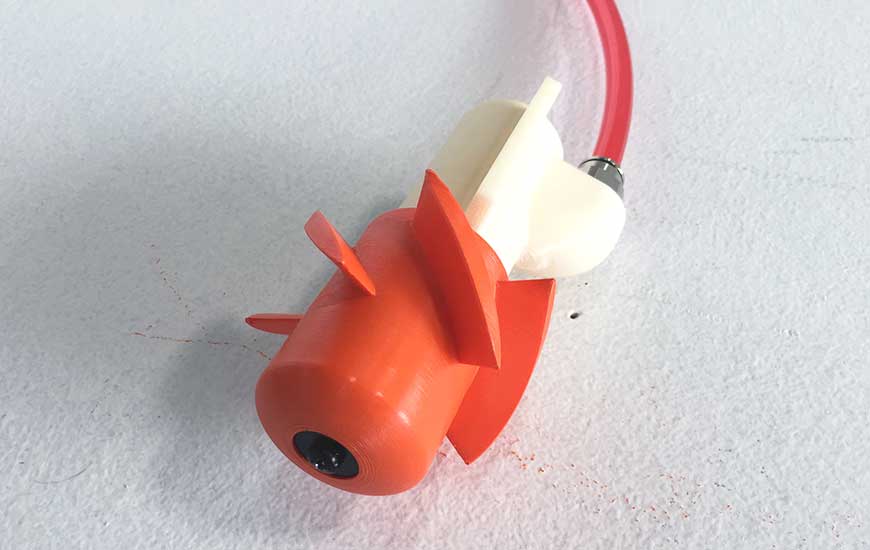
Working 3D printed miniature of a part
The first step of model design is to analyse the 3D model given by customer. It is very important to correctly cut the parts of the model and to choose the right direction of printing, as it saves up a lot of work during post-processing and painting. Later model is scaled and prepared for 3D printing with an extra care for thickness, detail level and joint tolerances. Detailed parts are always adapted separately to ensure their quality. After performed simulation, designer selects proper printing parameters and the 3D printer does the rest.
Miniature shipyard
With the parts printed and supports removed, parts are sanded, then painted. If the part does not require a mirror-like surface, team would print it already in its final colour. Broad colour palette provided by Zortrax is truly helpful, as native colours of Z-ULTRAT or Z-ABS eliminate need of heavy post-processing and painting. Windows and other glass parts of the model are usually done with Z-GLASS. Last step consists of assembling the model and adding final details. Since the team likes to push 3D printers to their technical limits, they try to avoid any traditional methods. Of course, some parts are required to be manufactured in other ways to make the yacht miniature lifelike. If you are interested in other scale models, check out architectural mock-ups and model of the off-road car.