The Key Factor of Innovation – 3D Printed Prototypes of DICSA
BACKGROUND: Spanish company DICSA is a leading manufacturer of stainless steel fittings as well as distributor of hydraulic components and fluid flow connectors. Since 1983, when it was founded, DICSA is successively upgrading every aspect of their operations. Implementation of 3D printing to the production cycle at the beginning of 2017 marks a new stage of the company’s development.
Among many other products, DICSA manufactures multicouplers. The purpose of the devices is to easily and securely connect various hydraulic and pneumatic components. They are mostly used in agricultural and construction applications. Therefore, their designs must be thoroughly tested, to provide dependable service in every situation.
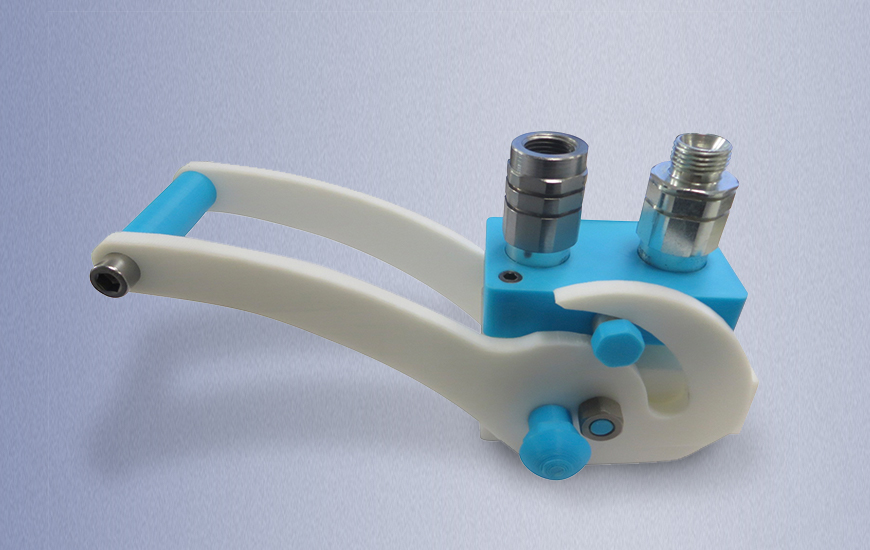
3D printed prototype of multicoupler
GOAL: To stay ever competitive and to guarantee the highest quality possible, the technical department decided to look for new methods of prototyping. Requiring a fast and dependable solution, they turned to 3D printing. Their aim was to improve mechanical system of the multicouplers, readjust connectors and to reduce construction costs.
Chosen initially because of its excellent performance-price ratio, Zortrax M200 has quickly proven to be a more than designing tool. By using economical Z-ABS material the engineers were empowered with a reliable mean of testing. The material characteristic ensures durable and flawless surfaces, excellent for the prototyping purposes.
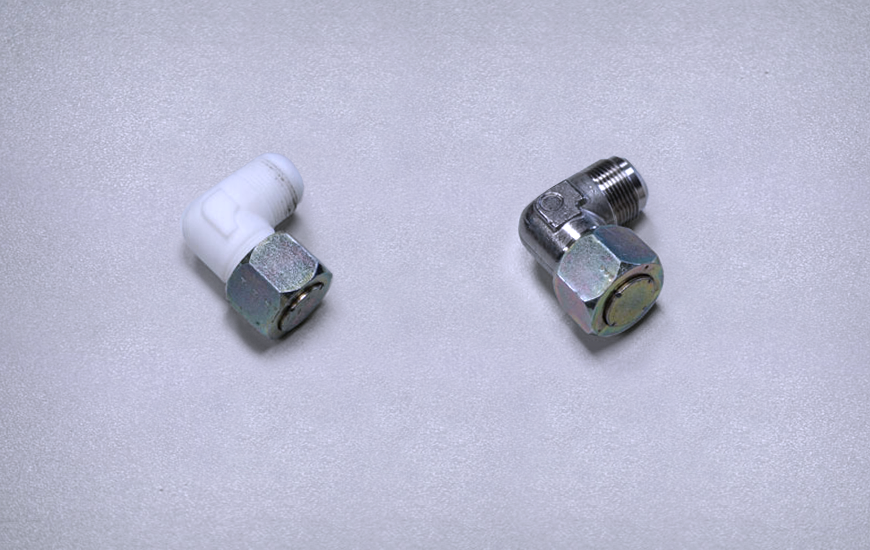
3D printed prototype and final part comparison
PROCESS: Furthermore, comparison of traditional methods of making test models and 3D printing confirms the undeniable superiority of the latter. DICSA estimates that prototyping became 80% cheaper after introducing the 3D printer. Savings are even greater, if you take into consideration all the issues resolved during the process. Once available only on the computer screen, 3D models became accessible for a closer examination. The 3D printed prototype can reveal otherwise hidden flaws of design.
According to DICSA, prototypes are ready for testing 3 times faster than before. Cost-efficient and quick, 3D printing serves as a viable alternative for previous, high-cost methods. Additionally, Zortrax 3D printer requires no start-up preparation and little to no maintenance.
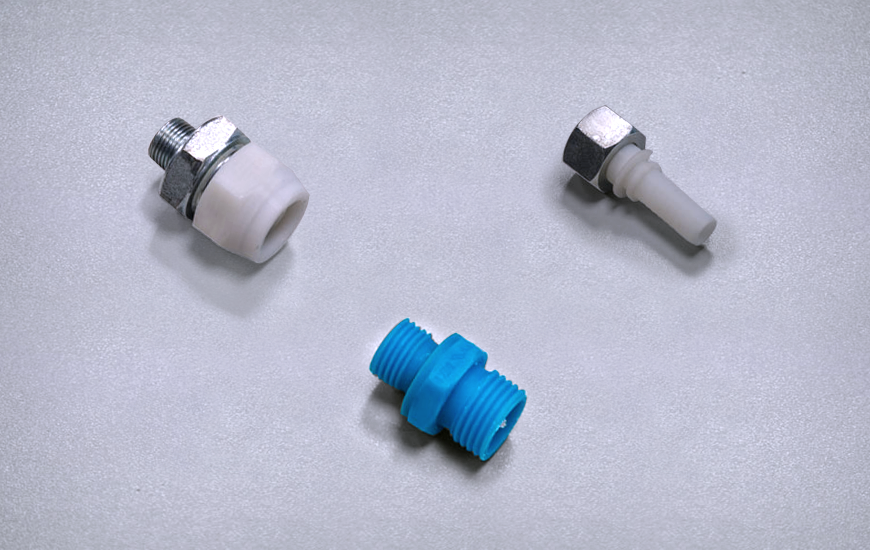
Various 3D printed prototypes
RESULT: Zortrax M200 not only allows to redesign and improve existing products, but also provides solution for initial test of custom pieces ordered by clients. Low volume production of highly specialized items requires thorough check of their designs. While inspection in 3D modeling software can pinpoint problematic areas, only a tangible object provides a chance to put the concept into a real test. These initial quality controls and low-cost visualizations became invaluable assets to the company’s clients.
CONCLUSION: Consequently, reliability of Zortrax M200, its speed and overall performance allowed DICSA to make the production cycle even more efficient. Engineers and designers can spot problems quicker and easier. Rapid changes to the designs are fast and effortless, as they require only to 3D print specific parts. What used to consume up to 120 hours of work of highly specialized machine, now it’s completed in less than two days by a single robust device.