3D Printed Boluses Help to Improve Radiotherapy Standards
BACKGROUND: Although the 21st century medicine seems to develop dynamically, there are still some areas that lack efficient solutions when it comes to fighting diseases. One of the most common diseases that causes suffering of millions of people in the world is cancer. Type of suggested treatment may vary among different cases, however the commonly applied method for curing cancer that appears on or just below skin often involves regular radiation. Unfortunately, during this procedure also the tissue that surrounds the affected area is exposed to X-rays. To avoid this, patients are applied special boluses, usually made of wax, but producing them is time and labor consuming and doesn’t guarantee producing a shape, which is precise enough to provide efficient protection from X-rays.
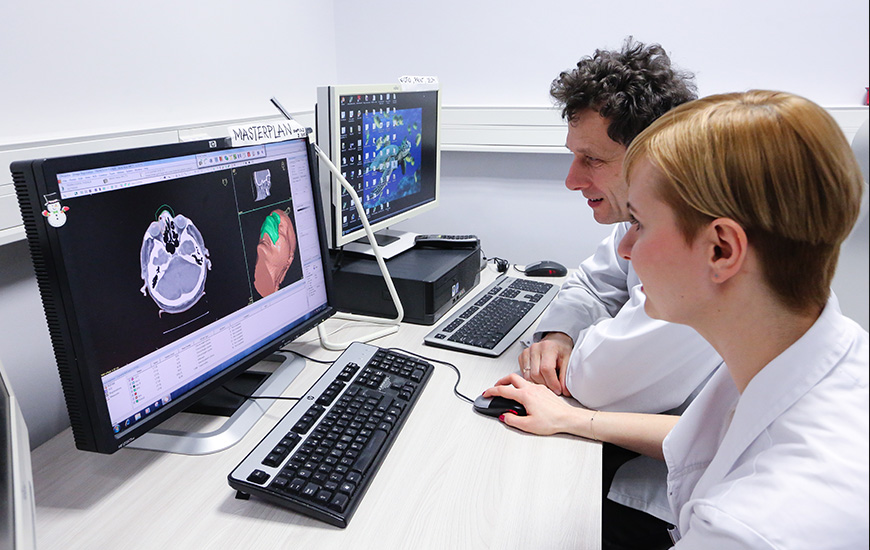
Doctors examining data for the model
GOAL: In one of the Polish hospitals, doctors who every day face the challenge of providing help to patients with cancer, Magdalena Łukowiak, Marek Boehlke and Marzena Więcko saw the so called ”spark” in 3D printing technology. This time the aim of the specialists from the West Pomeranian Center of Oncology in Szczecin was to create end-use products that can be used during the radiations to provide the exact dose of X-rays and protect the unaffected tissue. The whole process of production, involving 3D printing technique was expected to be highly precise, time-efficient and as hands-free as possible to save the time of oncologists and patients waiting for the treatment. Zortrax M200 was used to help the team of specialists to reduce the suffering of the patients and start reshaping the present medicine.
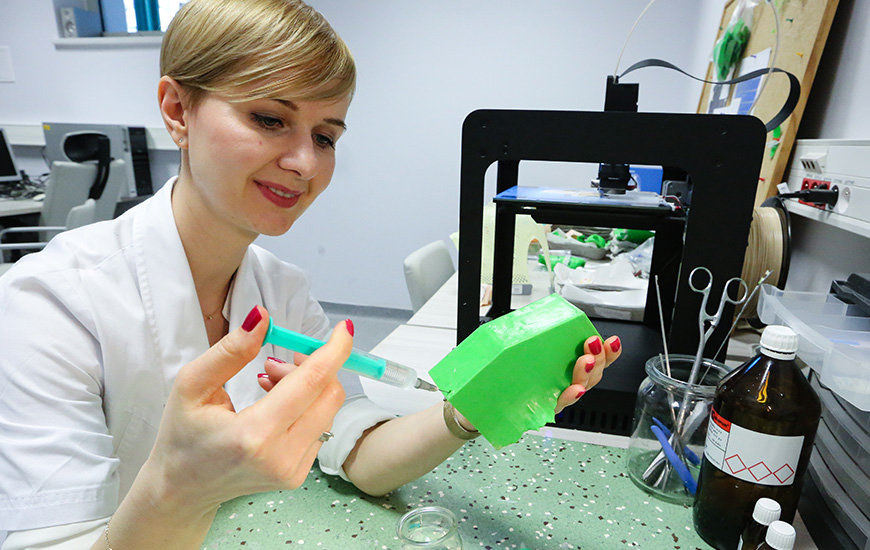
Doctor preparing the 3D printed bolus
PROCESS: Each bolus is unique and tailor made for a particular patient. Such personalization is possible thanks to the computer tomography that each of the patients undergo. During this procedure the dosage of X-rays is being calculated and the oncologists end up with a digital image and exact shape of a bolus. To get a 3 dimensional image of a bolus it is required to use special software to convert the DIOCOM data into files that a 3D printer can “read”, like .stl. Then the process of 3D printing can start. The time of the prototyping was reduced, comparing to the traditional methods, as 3D printing lasted a couple of hours, depending on the size of each bolus.
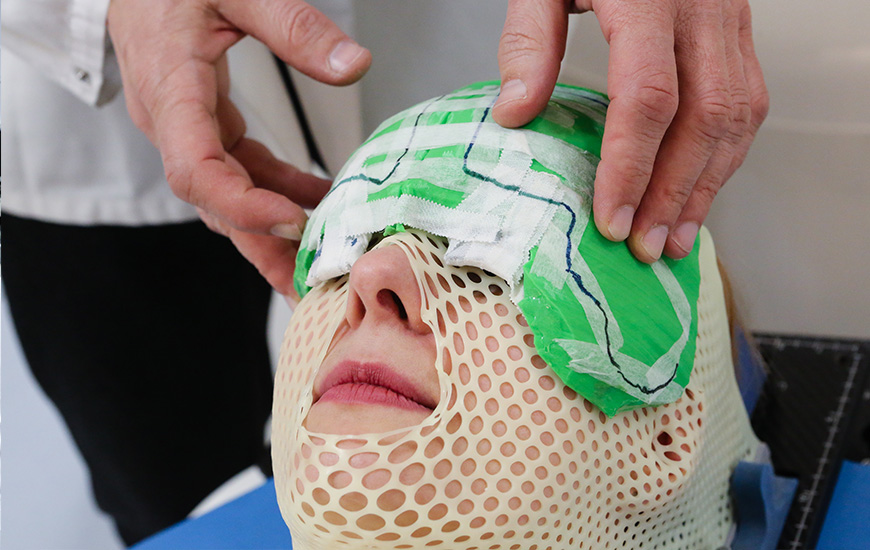
3D printed bolus on patient’s head
RESULT: The use of 3D printing technique resulted in creating precise shapes of boluses, which were able to reduce the radiation of unaffected tissue by 30%. The 3D printed boluses are similar to those designed at the planning stage from 83 up to 100%. When it comes to the dispersion of the radiation the differences are not bigger than 2%. Achieving such results is more than satisfying, bearing in mind that this level of precision wouldn’t be possible using the traditional methods. Thanks to the high dimensional accuracy and precision the boluses fitted the patients’ body well, which provided the part from displacing during the radiation.
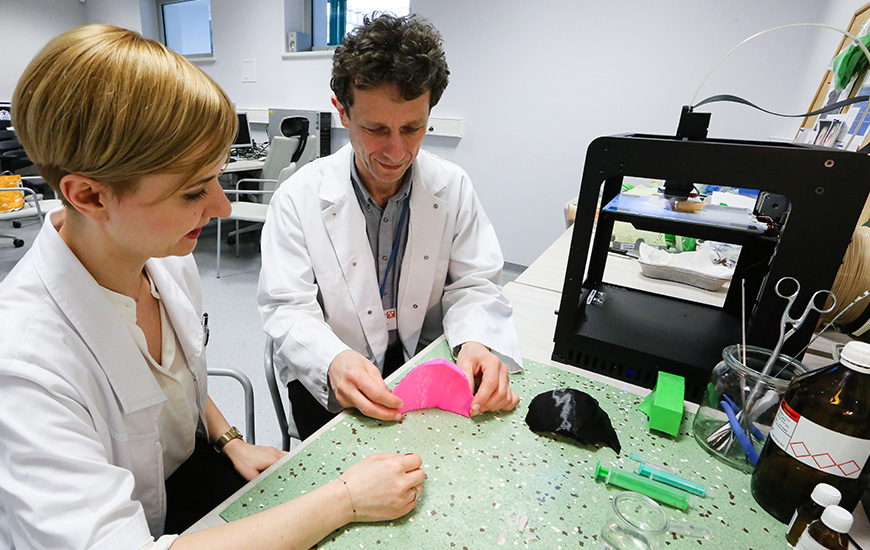
3D printed bolus for radiotherapy
CONCLUSION: Application of the 3D printing technology in the area of healthcare is not a fancy daydream. Instead, on the basis of the provided example, we can forecast that this technology will be playing a bigger role in the future development of medicine. As the convenience and health of the patients are the major points we should always focus on, we cannot overestimate the factors as precision and cost-efficiency of the whole process. It is commonly known that nowadays many hospitals have limited financial resources and sometimes they have to struggle to stay within the budget. Because of that fast and cheap method of producing medical equipment, by minimizing the trial and error process and reducing the labor of doctors, seems more than necessary. We hope this case will serve as inspiration for all those of you who have been working on improving the medicine, but were limited by the financial constrains. If you are interested in other medical cases, see our 3D printed heart or medical winch – all fully working and made in the additive manufacturing technology.
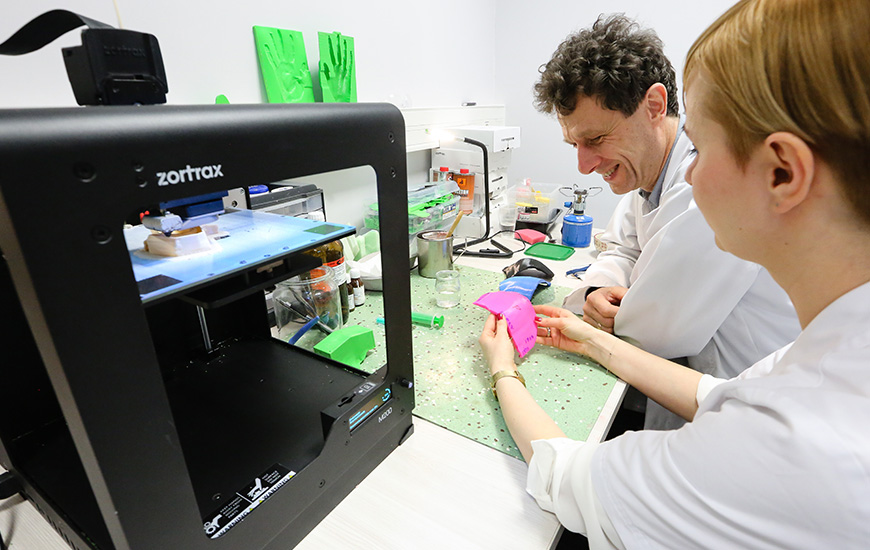
3D printed bolus and Zortrax M200 3D printer