What Makes Zortrax Inkspire 2 The Most Refined Resin 3D Printer on the Market
The Inkspire 2 is the latest and most advanced resin 3D printer in Zortrax lineup. It builds upon years of experience with photopolymer printing technology to keep everything that was great about the first generation Inkspire and make it better in every way. The Inkspire 2 has larger workspace, can work with more advanced materials, and is easier to work with than ever. Here are a few highlights that make this machine truly special.
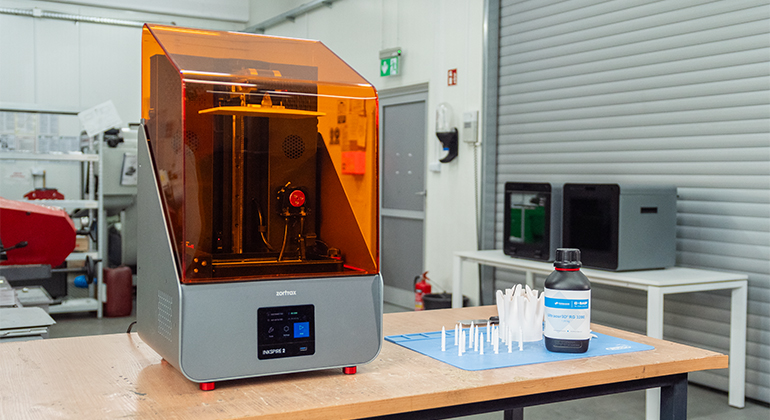
Zortrax Inkspire 2 – resin 3D printer working with a variety of professional resins.
Resin 3D Printer Compatible with Advanced BASF and Henkel Resins
A quality resin 3D printer should be able to work with best 3D printing resins on the market. That’s why Zortrax engineering team worked closely with world-leading resin manufacturers like BASF and Henkel/Loctite to make sure the Inkspire 2 would support their most advanced photopolymers. Since some of those resins had been originally designed for Digital Light Processing (DLP) industrial 3D printers which could cost north of 100k USD, the design goal set for the Zortrax R&D team was to make the Inkspire 2 capable of processing such materials while keeping the price affordable for a vast majority of customers. Below is a time-lapse of the Inkspire 2 working with Ultracur3D® RG 3280, a 3D printing photopolymer with ceramic filling, which is one of the most advanced resins made BASF.
UV Light Engine as Strong as DLP Projectors in an UV LCD 3D Printer
To achieve such results Zortrax team from the ground-up developed a cutting-edge proprietary light engine which is 7 times more powerful that the one used in the first-gen Inkspire. This new light engine can process nearly all high-end DLP resins at a fraction of a cost of digital projectors. Additionally, the light distribution was made 40% more uniform which means the same resin 3D prints quality can be achieved, regardless of whether the models are placed in the center or on the edges of the build platform.
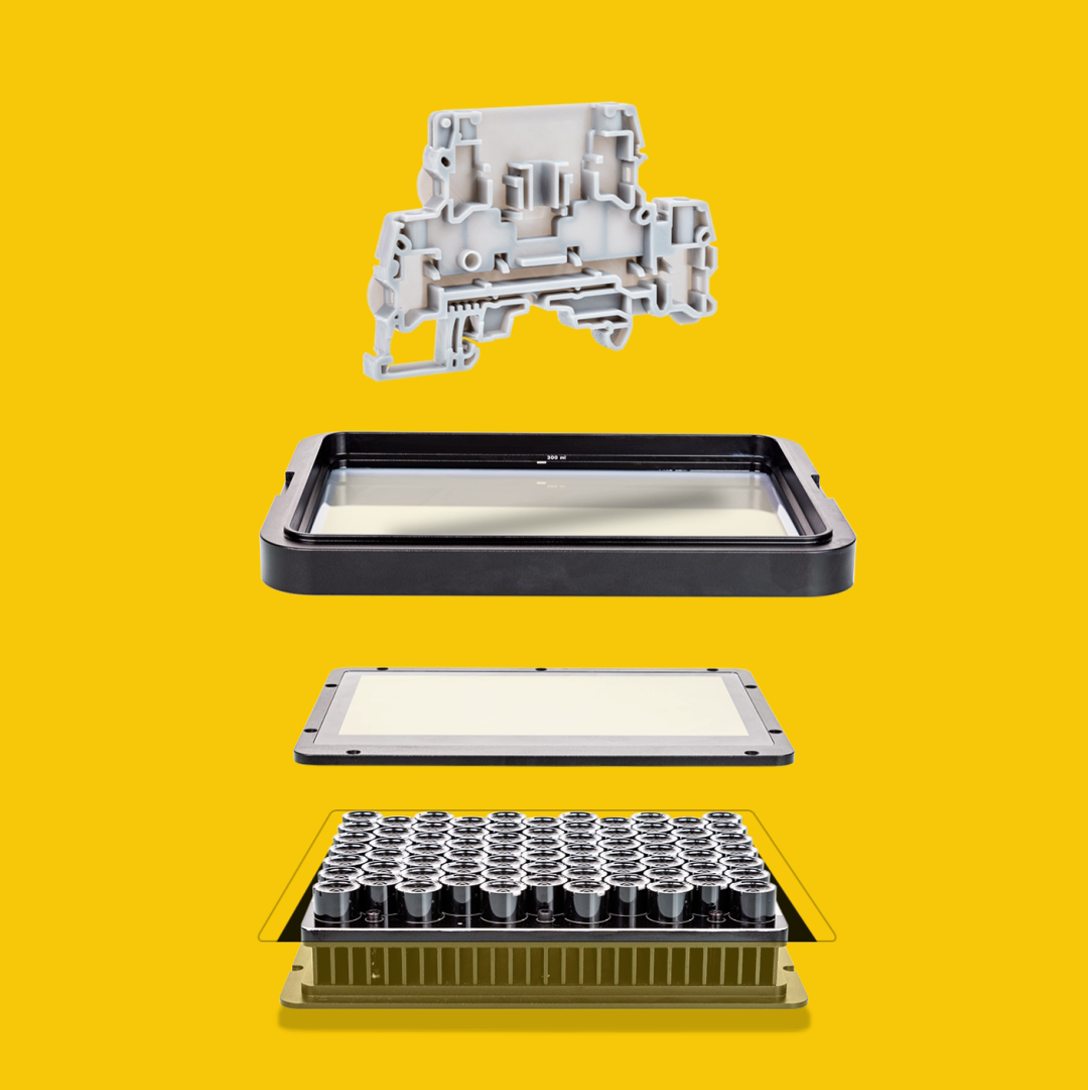
The proprietary UV light engine made by Zortrax engineers allows users to achieve the highest quality of resin 3D prints.
Large Industrial-Class Workspace
Moreover, the Inkspire 2 resin 3D printer was made 4x larger than in the last-gen Inkspire and measures 192 x 120 x 280 mm. Despite this relatively large volume, resin 3D printing with the Inkspire 2 ensures amazing precision. The XY resolution of the system is just 50 x 50 µm with a minimal layer height of just 25 µm. It also retains high speed of printing found in UV LCD 3D printers since the entire layer is solidified all at once with no need for a laser dot to draw it on a resin vat. And all this comes with outstanding ease of use.
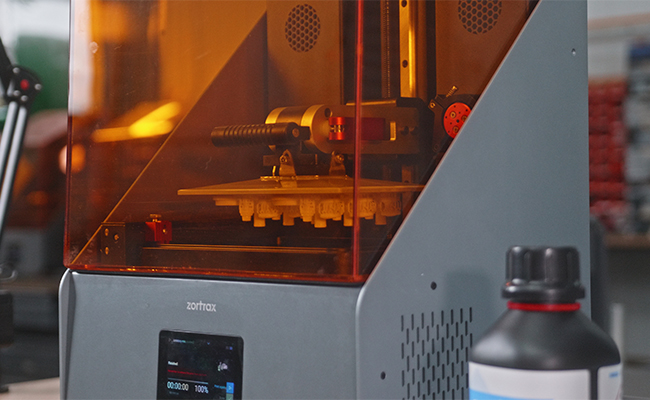
The large working space of Zortrax Inkspire 2 allows users to 3D print several models at once.
Factory-Calibrated Build Platform
The Inkspire 2 is made to automatically take care of as many aspects of the resin 3D printing process as possible. This design philosophy beings with build platform calibration which is usually the very first step a user takes after setting up a new 3D printer. The build platform in the Inkspire 2 is factory-calibrated to make the machine ready for work with best 3D printing photopolymers out of the box, so it doesn’t need to be calibrated at all. If calibration becomes necessary at some point in the future, the process is simple and boils down to following clear instructions displayed on the built-in screen.
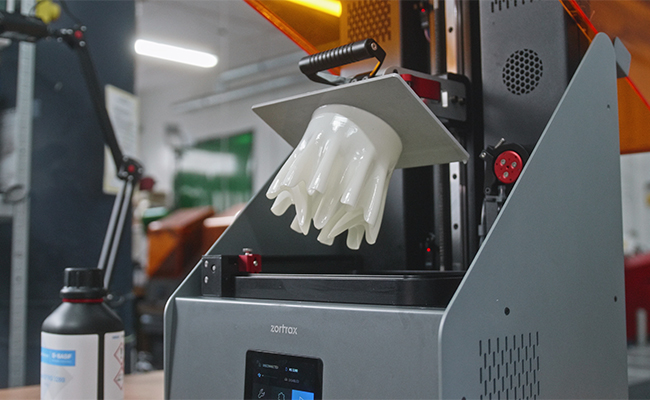
Pre-calibrated build platform allows you to start working with Zortrax Inkspire 2 3D printer almost immediately after unpacking.
Clean and Efficient Handling of 3D Printing Resins
Then there is the way the Inkspire 2 resin 3D printer handles the chosen resin. When working with supported materials, all that needs to be done is unscrewing the resin bottle, fitting it in a holder placed in the back of the printer, and choosing the right profile in Z-SUITE software that comes free with the Inkspire 2. The holder has a weight sensor so the Inkspire 2 knows exactly how much resin is in a bottle. This helps when larger, more material-intensive prints are scheduled. A user is informed if the printer has enough resin to complete the current print. Moreover, if the Inkspire 2 runs out of material it just pauses the print and resumes when the resin is refilled without ruining the model.
Once the printing process is started, a peristaltic pump automatically transfers the resin from the bottle to the resin vat. When the print is done, the same pump transfers the resin back from the resin vat to the bottle to prevent exposure to ambient UV light. To prevent sedimentation, which can happen with more advanced materials that are often a mixture of many different chemical compounds, the Inkspire 2 stirs the resin in the vat automatically. Stirring is done by a resin wiper that crosses the vat at speed and intervals predefined in the printing profile for each specific resin. This way, even extremely time-consuming prints can be done without any user supervision.
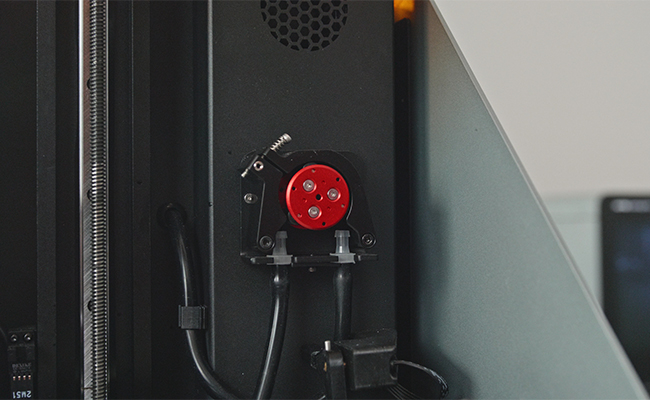
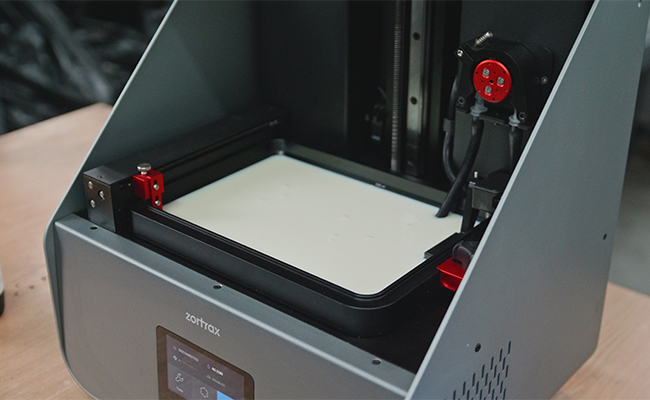
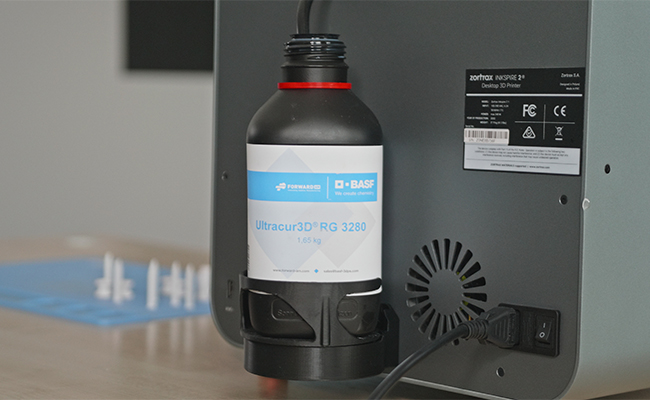
Intelligent Build Platform Hinge
Finally, there are multiple quality-of-life improvements in the Inkspire 2 achieved through clever engineering. The build platform can be attached and detached with a simple mechanism. It can also be positioned and locked at an angle to make the remaining resin drip down do the resin vat when the printing process is done. The same hinge is also compatible with Zortrax Cleaning Station, a post-processing device for cleaning resin 3D printed models, to make cleaning possible without taking the model off the build platform.
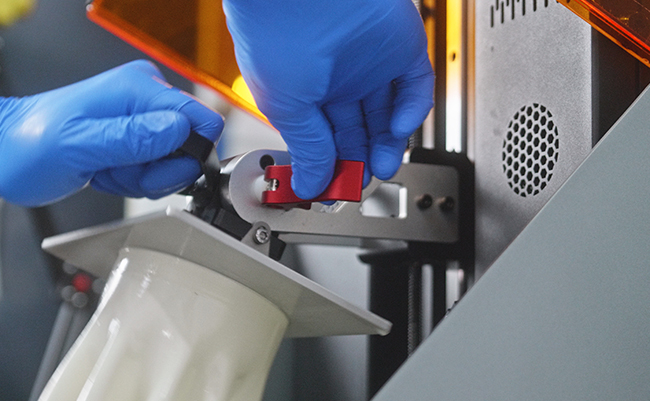
Smart build platform hinge helps you save the resin after 3D printing process.
Easy Post-Processing of Resin 3D Prints
All resin prints need post-processing once the printing is done. The two most commonly applied post-processing steps are cleaning, which is needed to remove the remnants of liquid resin off the model’s surfaces, and UV curing, which provides additional UV light exposure to the printed part to achieve the target mechanical properties of the material. Both those steps are taken care of by Zortrax peripherals – Zortrax Cleaning Station and Zortrax Curing Station.
Both Cleaning Station and Curing Station are stand-alone automatic post-processing devices which can work with nearly all resin 3D printers available on the market. This is why they are discussed in more detail in their own articles: Resin 3D Prints Cleaning Made Easier with Zortrax Cleaning Station, and Zortrax Curing Station: An Industrial Grade UV Curing Device for Resin 3D Prints. In this entry it suffices to say that specific settings for the Cleaning Station and Curing Station are suggested by Z-SUITE software for every print done on the Inkspire 2 with a supported resin. All a user needs to do once the printing is over, is to put the 3D printed resin model in the Cleaning Station, punch in these suggested settings and then, when the cleaning is done, do the same thing with the Curing Station.
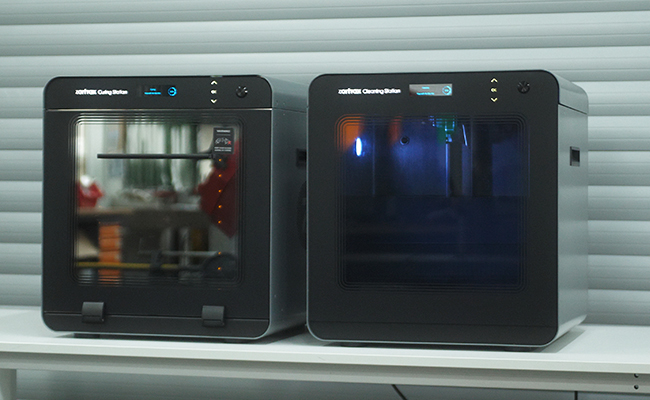
Zortrax Cleaning Station and Zortrax Curing Station – automatic post-processing devices for resin 3D prints.
The Inkspire 2, the Cleaning Station, and the Curing Station working together are a complete resin 3D printing system enabling a user to make excellent prints with a wide range of resins over and over again, getting rock-solid quality each time.
Go ahead and get in touch with Zortrax sales team: sales@zortrax.com to discuss your business case and learn how the Inkspire 2 can make your 3D printing operation better, faster, and more profitable.