Surfing the 3D Printing Wave with Cold Hawaii Shaping Bay
Imagine a beach in Hawaii. There are probably some palms, pristine sand and rainforest in the distance. All true, but what about plains covered with a carpet of shrubs, dunes and conifer woods? If it sounds out of place, it means you probably aren’t surfing. Welcome to Cold Hawaii, where wave catching and 3D printing go in pair!
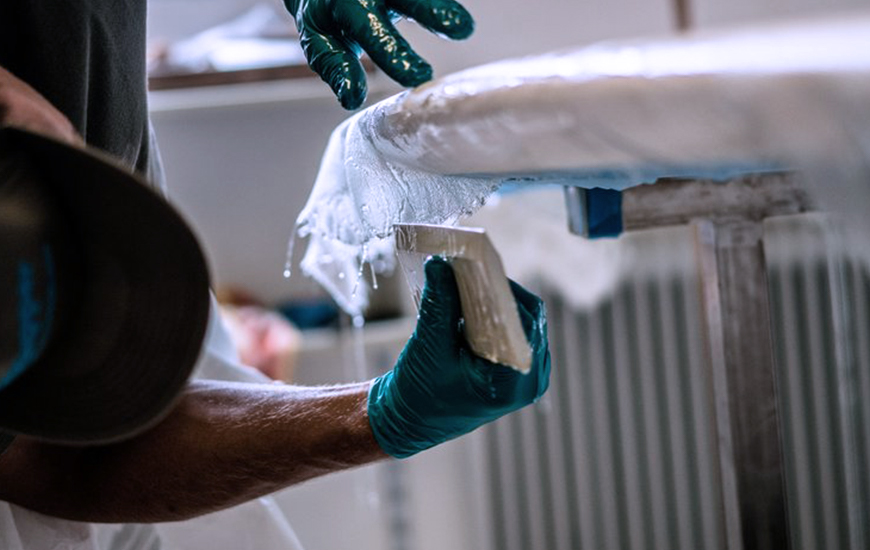
Surfing board glassing at Cold Hawaii Shaping Bay
Open Waters
Meet our host, Mads Ring from Cold Hawaii Shaping Bay located, contrary to your guess, in Vorupør, Denmark. Although, not so warm and widely advertised, the region of Thisted is one of the European capitals of surfing. Mads Ring have got a very specific set of skills, he makes things float. To be more precise, he constructs surfing boards and other equipment for water sports. In the workshop, genuine craftsmanship collides with the newest technologies. While most of the gear is handmade, some parts are 3D printed to reduce both time and costs.
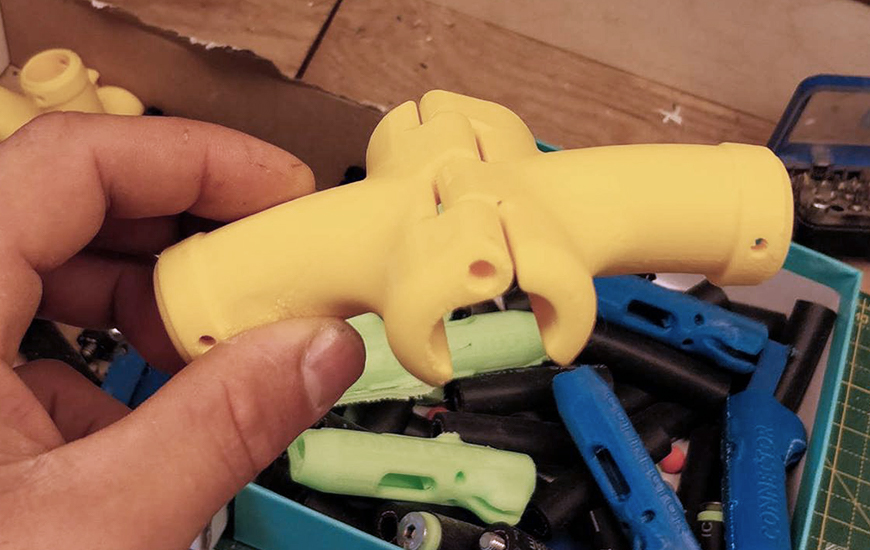
Boom head casted with 3D printed molds
His passion for water has started early, but at the time it was impossible to buy a proper gear in Denmark. So, he made it himself. After carving his first paddle for SUP board, he realized that water sports like surfing, windsurfing, SUP (stand up paddle) and kitesurfing can be essentially cheaper and much more accessible. Thus, the second passion emerged.
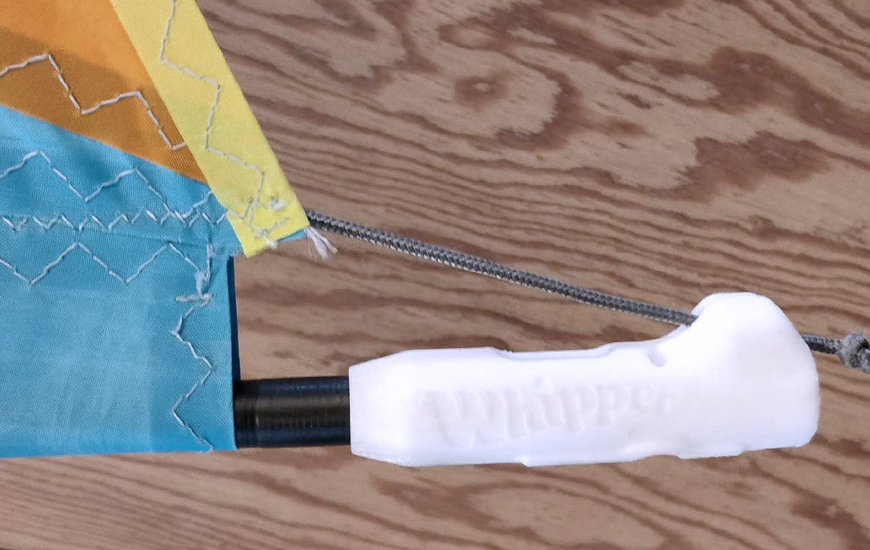
Mast base casted with 3D printer molds
The Shaper
To fulfil this mission Mads Ring has opened WhipperKids – small company aimed at delivering affordable windsurfing gear for kids. Designed with children in mind, the equipment is exceptionally lightweight and safe. With clients on 4 continents, the star-up phase seems to be drawing to an end. Mads Ring seeks solutions for scaling up the production. Furthermore, he runs Cold Hawaii Shaping Bay. The place is unique, as it is the first and only surfboard design school in Northern Europe. The bay is open to all who wants to make or learn how to craft their own surfing gear or to pick up glassing skills. He is a true entrepreneur, as he also owns a design and prototyping studio called Catalyst focusing on medical devices and short-cycle projects.
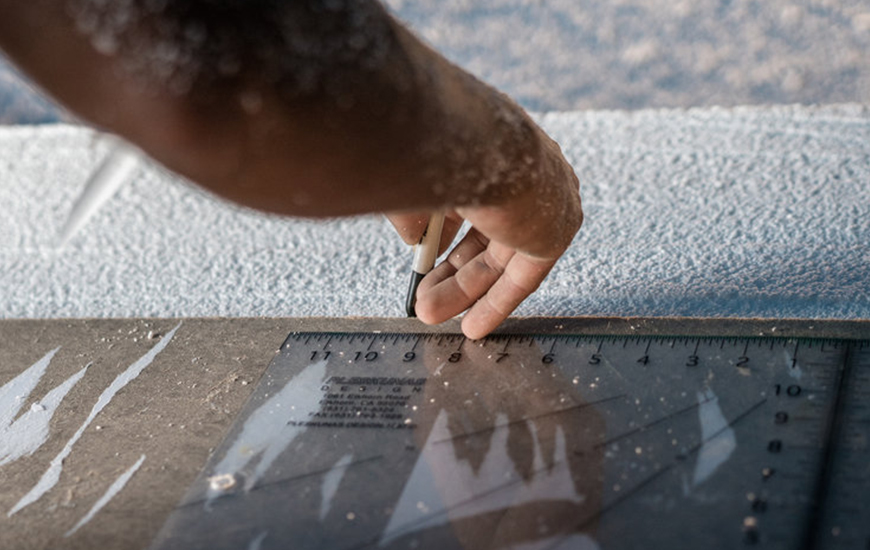
Mads working in his workshop
New School of Surfing
In all three, Zortrax M200 has a pivotal role during designing phase and final production. Although, the manufacturing scale of either of the enterprises is developing, benefits and cost savings resulting from using of the 3D printer are enormous. Let’s put the production efficiency aside, Zortrax M200 makes the ambitious projects possible without investment of large sums into tooling and testing. Additionally, the whole process can be completed in days, instead of weeks. Unyielding reliability and high quality of prints were the reasons for choosing Zortrax M200 and it lived to the expectations.
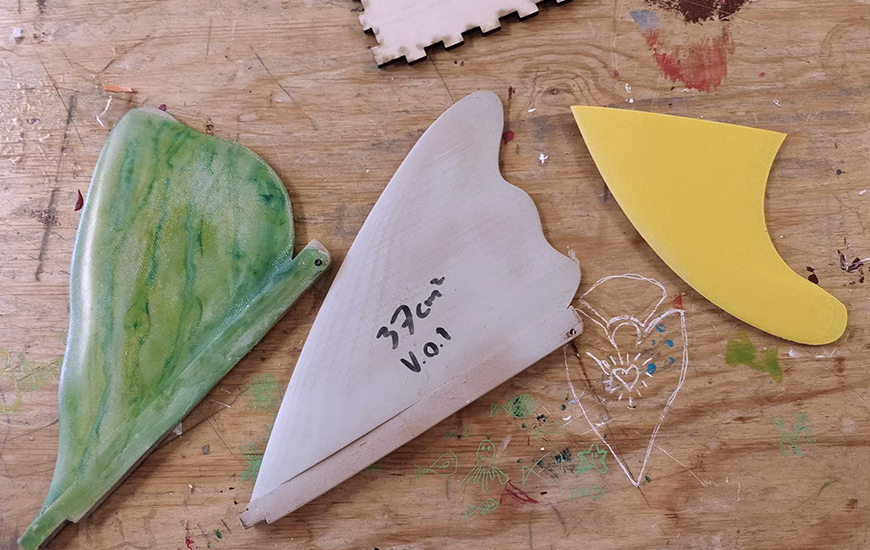
3D printed prototypes of fins
Economical Z-ABS material is used mostly during the first stages, where iteration after iteration optimal form is searched and found. Later, it can be replaced with sturdier Z-ULTRAT or Z-HIPS materials. Moreover, all of them can be easily processed, but as Mads Ring confirms, there’s little need for that. In most of the cases some putty and paint seal the deal. The range of the 3D printed items is spectacular indeed, from mast bases, elements of booms through end-use fins of surfboards to cases for the diabetes treatment devices. The growing demand forces the search for new methods of providing the supply. One of such is urethane casting. With it, Mads Ring sees the opportunity to scale up the production. Thus, Zortrax M200 helps to transition from small to medium scale manufacturing model.
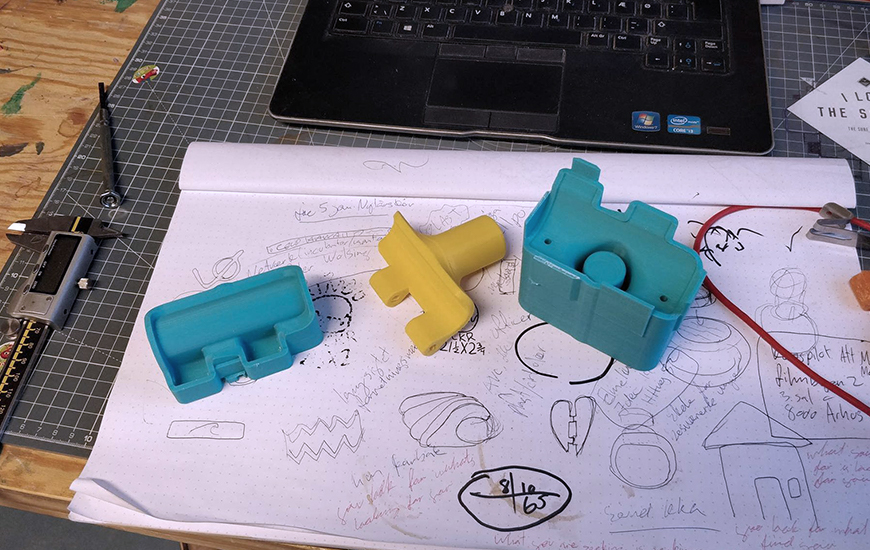
3D printed molds and part of boom head
If you are interested in 3D printing projects connected with water, make sure to ready about the yacht miniatures 3D printed by Superfici and the scale models of Antonio Eduardo Martins Palmeira. All photos courtesy of Mads Ring.