Welcome to the Shipyard of 3D Printed Miniatures
Making scale models is fun, but first of all, it’s a hard work. Especially, if you are doing it all by yourself. Constructing the parts, assembly, polishing and painting are all enormous tasks. However, 3D printing can make it a lot easier, while preserving high level of creativity. Let the works of Antonio Eduardo Martins Palmeira be the example!

Boat scale model on a beach
Frames, Hulls and Keels
Traditionally, to make a scale model, one would have to carve its shape in desired material. Then add smaller features and paint it. If someone is looking for a more detailed way of constructing the miniatures, creating each part separately is a way to go. The method got the advantages of higher precision and overall trueness of the design. Nevertheless, making those tiny components might turn out to be problematic. Among many available methods, carving each part separately in metal or wood seems the most plausible, but that’s just the beginning of the process. Every part must fit perfectly or you are risking the additional work. Antonio understands all of it. After all, he got years of practice in making scale models. What he also knows, is how to optimize the process.
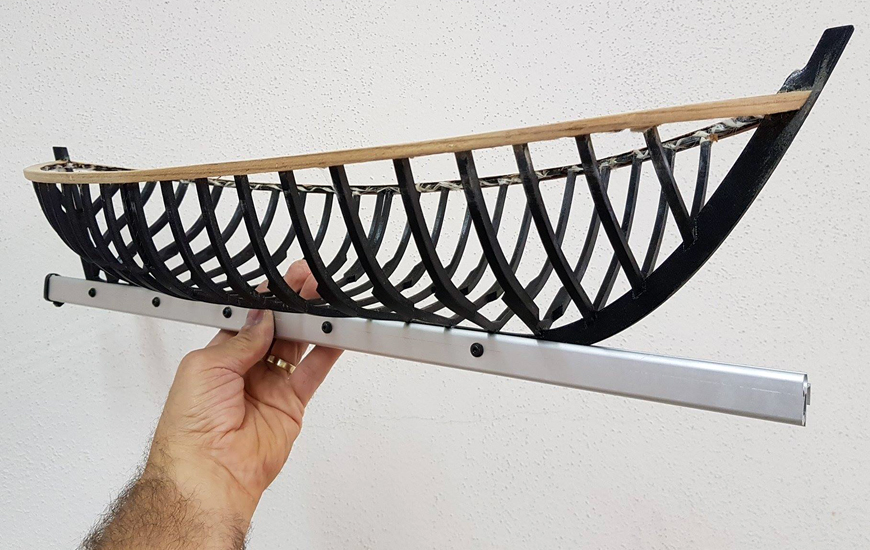
3D printed frame made with Z-ULTRAT
High Tide
It all began with Zortrax M200 3D printer. Now, most of the tedious manual labor has been eliminated. As Antonio confirms, 60% of work is solved with few clicks in Autodesk Inventor and Z-SUITE. While parts are 3D printed, the artist got time to concentrate on design phase and fine details. Furthermore, precision of the device ensures millimeter level accuracy, making all 3D printed parts fit to each other flawlessly. With the introduction of Zortrax M200, Antonio has achieved three important goals: lower construction time, lower involvement in construction process and higher dimensional accuracy of created parts.
Smart Solutions
Antonio’s 3D printer of the choice is Zortrax M200. The reason was simple, he was looking for a top performance machine at the affordable price. Excellent 3D printing quality and unyielding reliability are the core values of every Zortrax 3D printer. Furthermore, the artist is delighted by how self-sufficient the device is, as he said, “no babysitting” is required. Automatic adjustments and calibration makes 3D printing even more convenient.
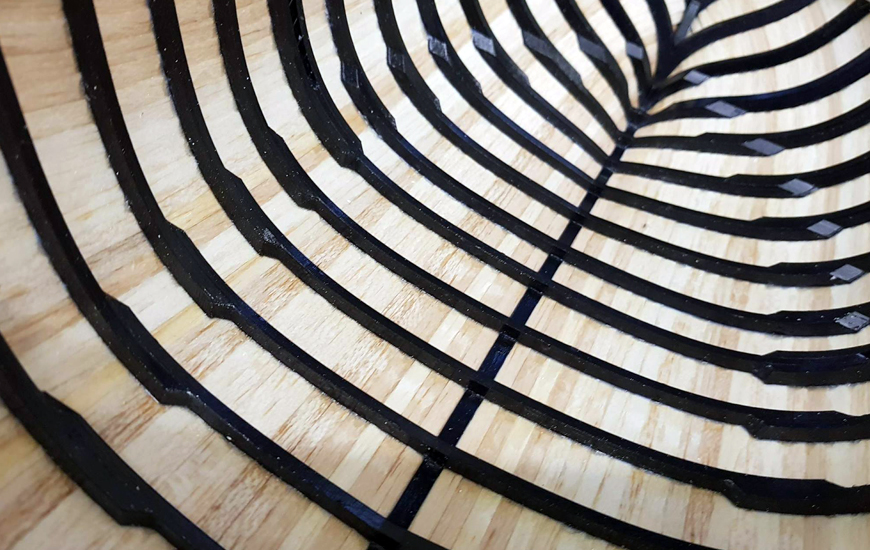
Hull with the 3D printed frame
As for 3D printing material, technical characteristics were the deciding factor. Strong and durable, Z-ULTRAT is ideal for any kind of model. After removing the supports and basic sandpapering, parts are ready for assembly. What’s even more important to Antonio, the material works well with balsa wood. All he needs is to apply a little of glue and after couple of seconds, parts are securely joined. That’s a considerable advantage over regular method of locking the pieces together. Just to compare, finishing the hull’s planking used to take 50 hours, now it’s ready in four.
Setting Sails
Works of Antonio Eduardo Martins Palmeira were displayed in museums in Povoa de Varzim and Esposende in Portugal. He is currently working on “Our Lady of the Martys” – Portuguese ship from 1616. The construction of this massive scale model, began years ago, but now with Zortrax M200 at his disposal, the artist is sure to finish the job. Thanks to the 3D printer, making tiny details will become significantly simplier and quicker. Can’t wait to see it finished!
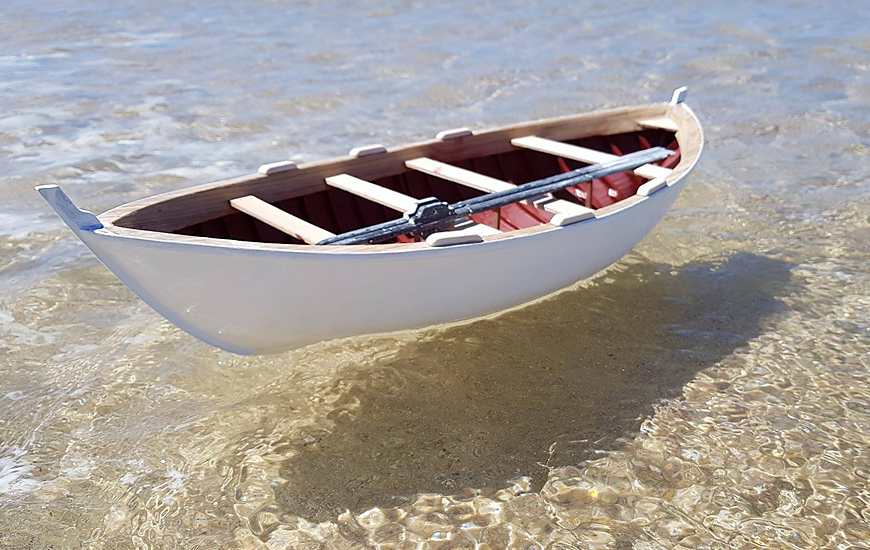
But does it float?
If you are interested in the subject, be sure to read our blog entry on 3D printed scale models for naval industry.