Setting up the Zortrax Resin 3D Printing Ecosystem
Quandum found the unboxing and setup procedure of the new Zortrax 3D printing ecosystem easy and clearly explained. The Inkspire 2 arrived with the pre-calibrated build platform and practically assembled besides the resin wiper and the resin Zortrax arrived assembled with the need to install the washing basket and the support for the build platform. The device also needed to be filled with IPA (isopropyl alcohol) before first use. Zortrax Curing Station, made for providing additional UV exposure to resin 3D printed parts, needed no assembly whatsoever.
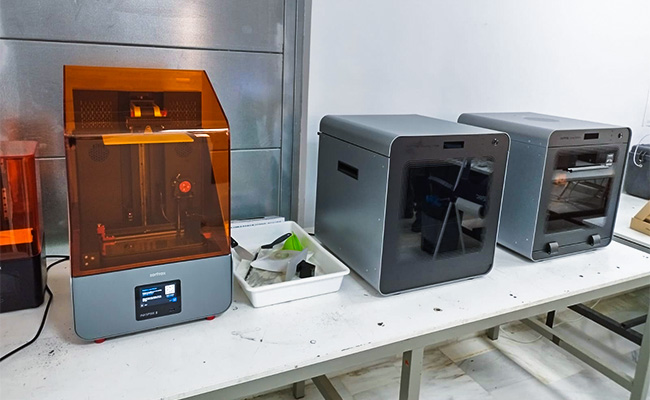
Zortrax Inkspire 2 3D printer, Zortrax Cleaning Station and Zortrax Curing Station all set up at Quandum Aerospace headquarters.
The team was ready to work with all three devices in under an hour.
The project chosen for 3D printing first end-use parts was a medical device manufactured for one of the Quandum customers. The Zortrax 2 and accompanying post-processing devices were used to build two components.
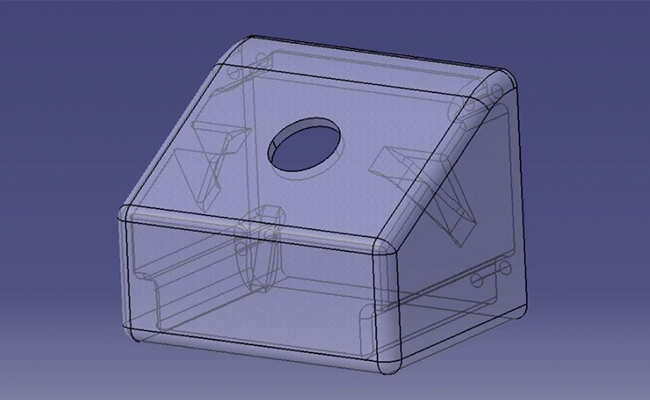
CAD design of the medical device control module part made by Quandum Aerospace.
The first one was part of the device’s control system, a relatively large design, measuring 96 mm x 70.6 mm x 75 mm, with holes included to host thermally installed threaded inserts.
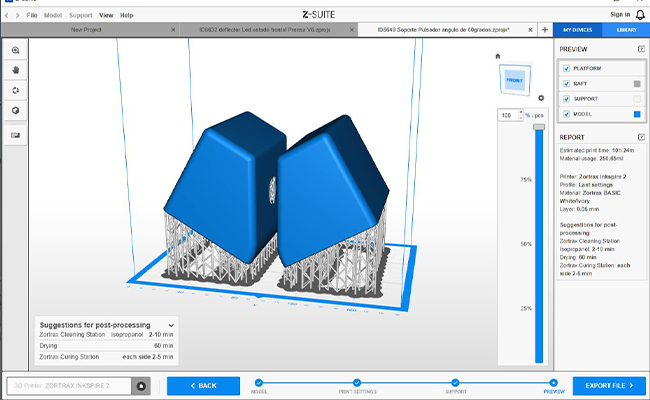
A part of the medical device control system design uploaded to Z-SUITE software. Due to large workspace it was possible to fit two units on the Zortrax Inkspire 2 build platform to 3D print them in one go.
The team used Zortrax Loctite PRO 410 resin to fabricate the component and achieved excellent results using default settings for this material available in Z-SUITE software that came free with the printer. This is one of many new professional materials the Inkspire 2 has been designed to work with from the ground up.
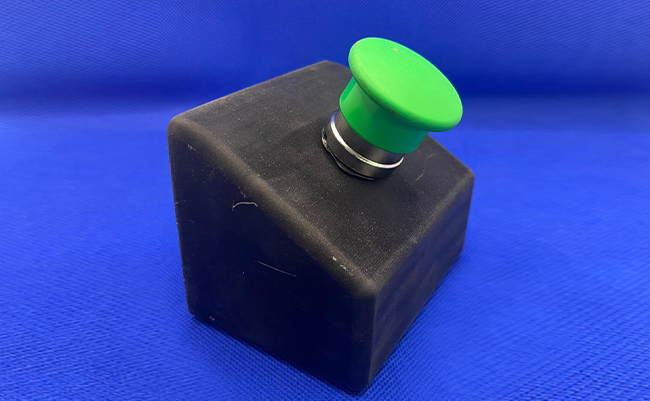
One of the first prototypes of the medical device control units with a rotating knob attached.
“We engaged with Zortrax a few years ago when they decided to open their system to industrial focused materials and re-design their system more towards the engineering and industrial users. It is worth mentioning that Zortrax focuses on, in addition to print performance, an integrated solution including post-processing. They were taking a new approach, and we wanted to be a part of that process as a high-performance material provider.”, says Maarten Adolf, Senior Business Development Manager – 3D printing Europe at Henkel AG & Co. KGaA.
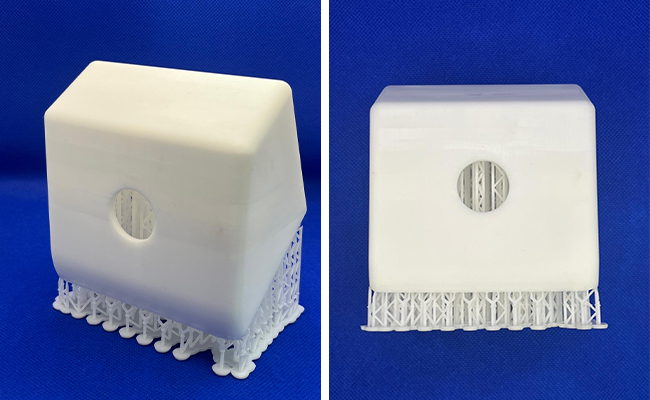
Same control system component 3D printed with Zortrax Resin Basic White on the Zortrax Inkspire 2 3D printer.
Quandum team achieved equally good results with used to fabricate the same design.
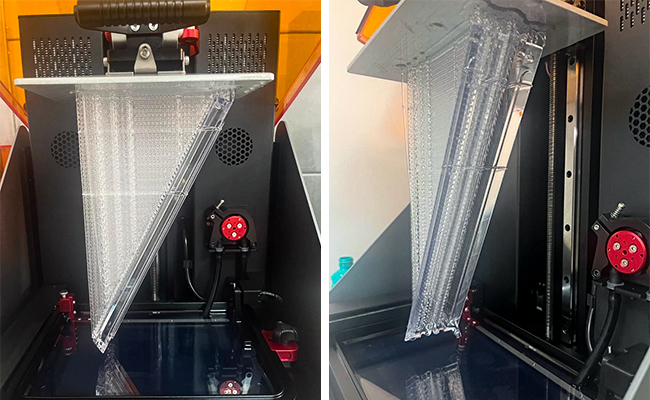
Light diffuser for the same medical device 3D printed with translucent photopolymer on the Zortrax Inkspire 2 3D printer. Shot taken just after the printing was done with the model still attached to the build platform and with support structures present.
The second 3D printed design was a translucent light diffuser made for the same medical device. For this project, the Quandum team chose the E-Glass 3SP.
This resin is made by Envisiontec and is not factory-calibrated for the Inkspire 2 3D printer. Because the Inkspire 2 is an open system fully capable of working with external materials the team could choose the printing settings manually via the External Materials section in Z-SUITE.
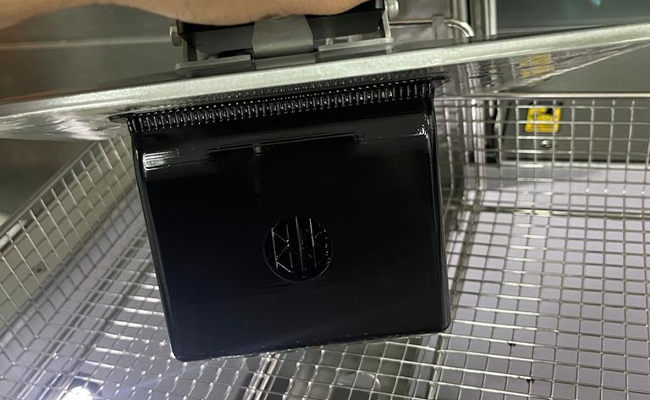
Part of the medical device control system 3D printed with Zortrax Loctite PRO 410 photopolymer after cleaning in the Zortrax Cleaning Station.
All parts 3D printed on the Zortrax Inkspire 2 went through the post-processing stage in the Zortrax Cleaning Station and Zortrax Curing Station.
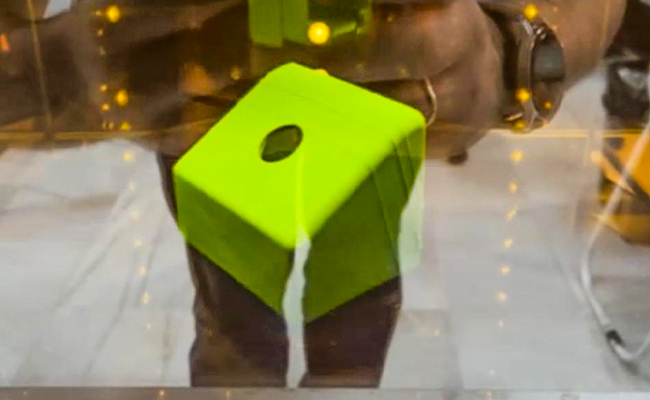
Part of the medical device control panel in the Zortrax Curing Station.
The team found both post-processing devices to be very user-friendly, well-made, and reliable. The quality and properties of the 3D printed and post-processed models were therefore described as excellent.
Quandum’s Thoughts on Zortrax Powerful Trio
Quandum’s team found the Zortrax Powerful Trio to be fast, easy to use and efficient. According to them, the Zortrax Inkspire 2 3D printer, Zortrax Curing Station, and Zortrax Cleaning Station are “amazingly designed”, complement each other perfectly, and can support constant, intensive workloads in high-tech manufacturing company.
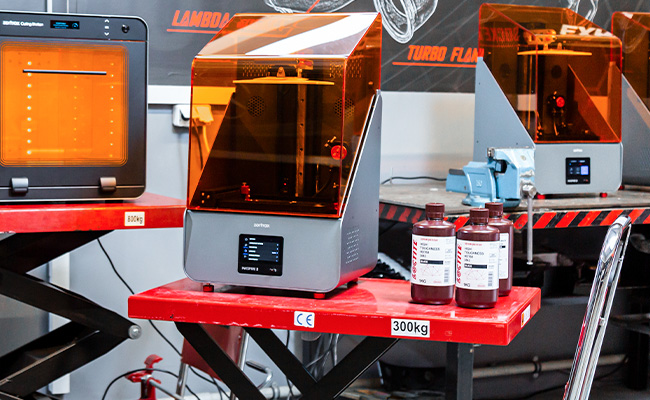
Zortrax Inkspire 2 UV LCD 3D printers.
The team concluded that the Zortrax Inkspire 2 was perfect for fabricating large prototypes and short-series manufacturing. They stated that the machine was easy to clean and maintain in perfect working condition. Other features highlighted by them included factory-calibration of the build platform, and the resin control system which made it possible to build fairly large parts.
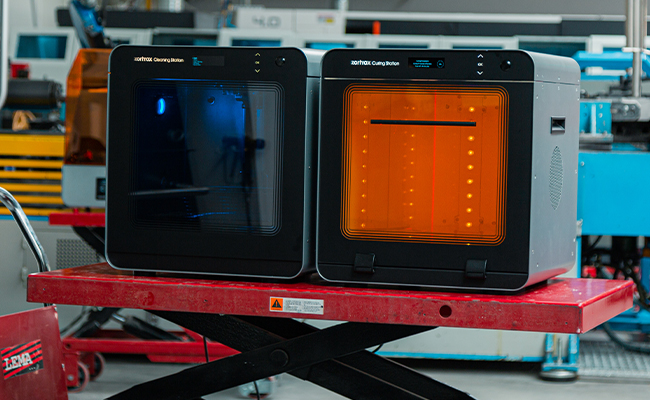
Zortrax Cleaning Station on the left and Zortrax Curing Station on the right.
Zortrax Cleaning Station was appreciated for its automation, especially for elevating the models of the cleaning fluid after the cleaning process is done. Zortrax Curing Station, the last link in the resin 3D printing chain, was also found to be simple and easy to use. Each curing session took only a few minutes. Since the correct post-curing time is indicated in Z-SUITE software, there was no confusion as to choosing the right settings.
“Feedback on the Zortrax Powerful Trio we get from Quandum and many others is very encouraging to say the least. Users like this new lineup, find it efficient, rock-solid, and easy to work with. That’s what we aimed for. Now we know that’s what we delivered.”, says Mariusz Babula, CEO of Zortrax.
Feel free to get in touch with our Sales Department or local Resellers and talk about the Zortrax Powerful Trio capabilities, pricing, and availability. Zortrax Inkspire 2 3D printer, Zortrax Cleaning Station, and Zortrax Curing Station can be also ordered via Zortrax Online Store. Full range of Henkel/Loctite 3D printing resins calibrated for the Inskpire 2 3D printer can be found here.