Light Without Shadows – Quartica Lamp by Paolo De Giusti
Designers are busy folk. The constant chase for perfection of form and function leaves little time for anything else. If they are not concocting designs of a new bike, furniture or space equipment, they might be as well tinkering with everyday objects. Let’s take a lamp as an example. Some of you might think, there’s not much to be done with it. You would be surprised how resourceful designers can be. Just give them a 3D printer and a task of making working environment more comfortable.
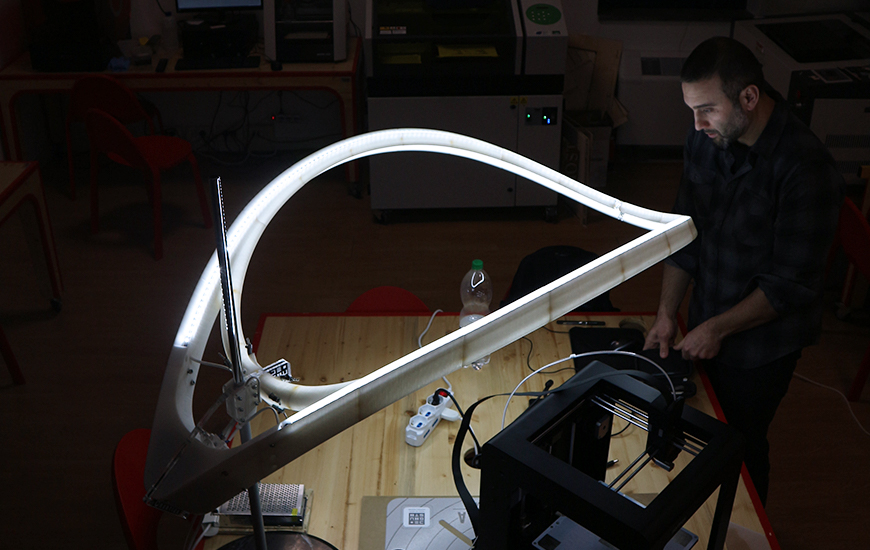
Quartica lamp, Paolo De Giusti and Zortrax M200
Quartica No Shadow Lamp designed by freelance industrial designer Paolo De Giusti from Olevano Romano, Italy is an excellent example of reimagined common products. The idea behind it was simple – to improve work comfort. Everyone who spends long hours in front of a computer or in a workshop understands how important proper lighting is. It’s a matter of ergonomics and health, after all. Nevertheless, the lamp offers much more than even distribution of light. As its name suggests, objects lit by it cast no shadows. Light evenly emitted by a set of diodes located inside the lamp’s frame removes all shadows under it. And it makes all the difference, if you are an artist, engineer or photographer.
No Shadow Lamp
Shape of Quartica was modeled to create a big area of super smooth light. However, the structure was too complex to prototype with traditional methods, so Paolo De Giusti decided to rely on 3D printing. 1,5m in diameter, the lamp’s model had to be divided into 24 sections, each 3D printed separately and easily merged using acetone. That’s one of the perks of using Z-ABS. Economical 3D printing material not only offers superb quality, but also can be effortlessly post-processed. Still, in this case the post-processing was minimal. Paolo well-versed in additive manufacturing, knew how to position his 3D prints to minimalize further work. Thus, all parts were 3D printed without support structures. Moreover, proper positioning provided them with extra durability. After joining the elements together, Paolo De Giusti sanded the structure and applied a layer of transparent paint. The last step provided the lamp with stain protection and made cleaning easier. In total, 2,5kg of Z-ABS were used to 3D print the prototype.
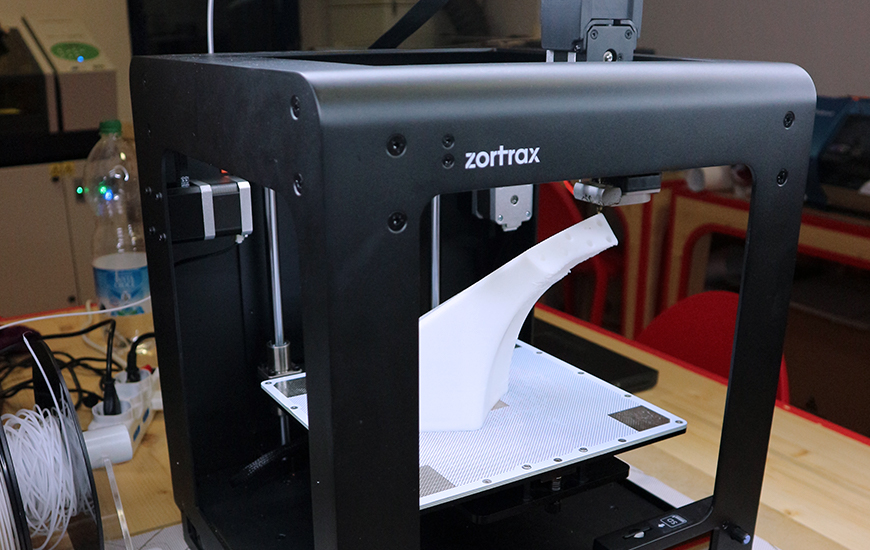
3D printed part of the lamp inside Zortrax M200
Let There Be Light
Paolo’s studio – De Giusti Design specializes in industrial design, working for both big companies and startups. Many of his past projects were prototyped using 3D printing. The No Shadow Lamp was designed and 3D printed for “Make Your Idea” contest. During three months, all participants could use resources of the local Fablabs in order to create a working prototype for European Maker Faire 2017 in Rome. Needlessly to say, Quartica was chosen.
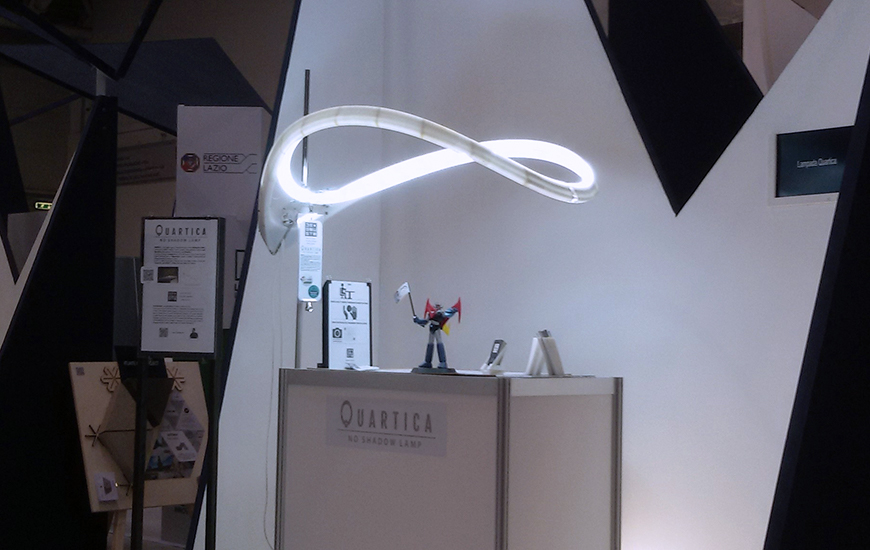
Paolo’s stand during Maker Faire 2017
In three months time, Paolo was cooperating with Ferentino Fablab Powered by LazioInnova, with the help of Spazio Attivo Colleferro, equipped with Zortrax M300, to take care of larger parts, some of which required up to 40 hours to finish. Smaller elements were 3D printed on Zortrax M200 in Ferentino. Both machines, although different in size, offered exceptional quality of 3D printed objects. A heated build platform, side covers and printing rafts ensured that all parts were 3D printed without the risk of warping. Consistent and designed to work flawlessly straight out of a box, 3D printing involved no further adjustments. Experienced with other brands of 3D printers, Paolo found the process highly intuitive. Starting with straightforward settings selection in Z-SUITE 2 Beta and ending with fail-safe 3D printing on Zortrax M200 and Zortrax M300.
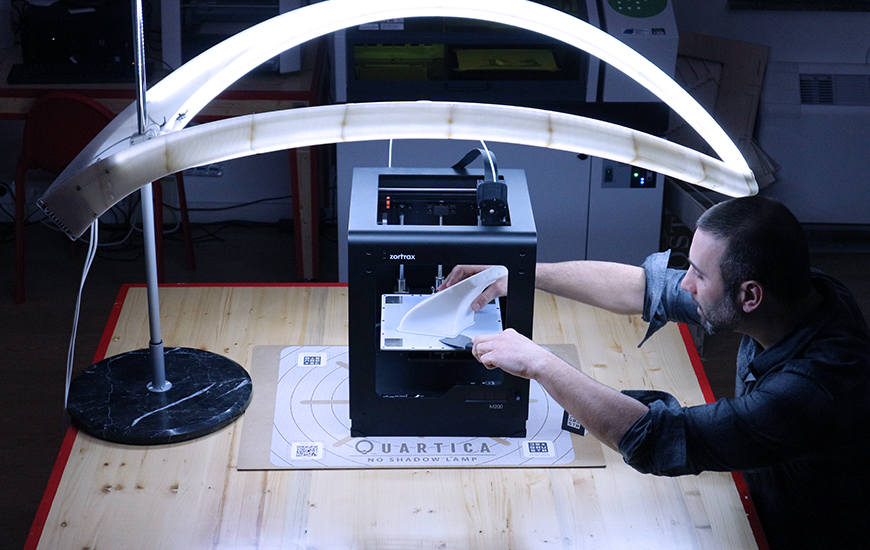
No shadows casted
Production of Quartica No Shadow Lamo is intended to start, as soon as the final version is completed. Furthermore, the designer is determined to stick to 3D printing. Four 3D printed prototypes have proved their usefulness in Paolo’s workshop providing smooth lighting. Stay tuned for more projects of Paolo De Giusti and meanwhile read about other 3D printed lamp projects: IcoLED and Bardi. All photos courtesy of Paolo De Giusti. Quartica No Shadow Lamp has been 3D printed with the help of Silvia Putano – Technical Manager at FabLab Ferentino and Barbara Santucci From Spazio Attivo Colleferro.