Introducing BASF Ultrafuse PP GF30, PAHT CF15 and PET CF15: High-Class Engineering Filaments
Summary
- Zortrax has introduced three engineering BASF Ultrafuse filaments for the M300 Dual 3D printer.
- BASF Ultrafuse PP GF30 is commonly used in automotive industry and operates in the range of temperatures required by all leading automakers, while BASF Ultrafuse PAHT CF15 has excellent thermal and mechanical performance and can be used to 3D print parts with significant impact resistance.
- BASF Ultrafuse® PET CF15 is a strong and rigid material designed for operation in humid environments due to very low moisture absorption.
BASF is one of the biggest players in the chemical industry and now its tried and true Ultrafuse filaments are available for Zortrax M300 Dual. The first one is called Ultrafuse PP GF30 and consists of polypropylene reinforced with 30% addition of glass fiber. The second is Ultrafuse PAHT CF15, a polyamide reinforced with 15% of carbon fiber. The PP GF30 has been widely used in automotive industry for years. A quick glance under the hood of pretty much any modern car, and this material can be found there. The PAHT CF15 is even stronger and more resistant to high temperatures, so it can be used in advanced robotics and aerospace applications as well. Here’s a brief overview of these amazing materials.
BASF Ultrafuse in Automotive Applications
PP GF30 is heavily used in the automotive industry for a wide range of components. Using this material for structural and semi-structural parts instead of a more traditional aluminum generates significant weight and cost savings. For this reason, various automotive OEMs choose to go for PP GF30 when building tailgates or lift-gates, instrument panel carriers, mirror brackets, engine covers, door module assemblies, active grille shutters and more. PAHT CF15 can be used in even more demanding applications, where higher rigidity and better thermal stability is required.
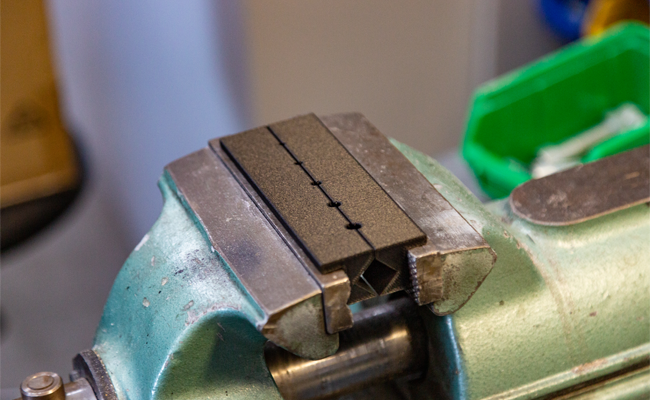
BASF Ultrafuse materials have exceptional mechanical properties.
Using plastic instead of metal alloys in all those applications grants more design freedom to engineers who can achieve optimal shapes and geometries. Weight savings are also crucial, especially with the recent rise of electric vehicles where relatively heavy batteries need to be compensated for by making other components lighter to increase range. All these considerations contribute to growing popularity of polymeric materials in automotive industry.
Excellent Stiffness and Thermal Stability
Glass fiber addition makes parts 3D printed with PP GF30 exceptionally stiff. This is particularly important in parts used in automotive interiors. A part that does not give in and deform under stress does not generate creaking noises. Moreover the material retains this high stiffness in a wide range of temperatures.
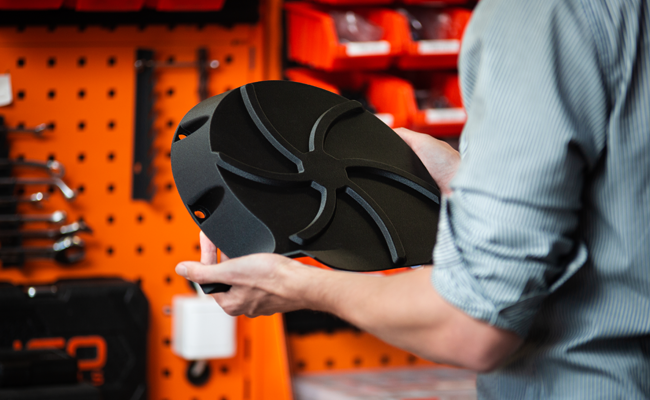
Zortrax Apoller rear cover 3D printed with BASF Ultrafuse PP GF30 on Zortrax M300 Dual.
The heat deflection temperature of PP GF30 is 73 °C at 1.8 MPa and over 127 °C at 0.45 MPa. This corresponds neatly with the general requirements of automotive manufacturers that need to use materials retaining their properties in a range between -30 °C and 80 °C for interiors and a little above 120 °C for parts working under the hood, near the engine.
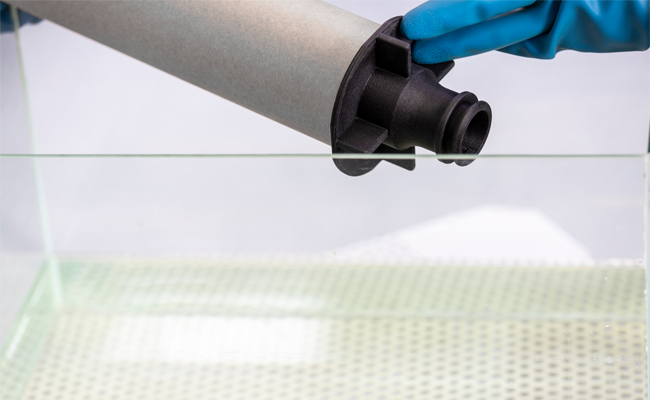
BASF Ultrafuse filaments all have strong chemical resistance.
PAHT CF15 offers slightly wider range of operating temperatures. Its heat deflection temperature at 1.8 MPa is 92 °C and goes all the way up to 145 °C at 0.45 MPa. Addition of carbon fiber guarantees the rigidity of PAHT CF 15 is even higher than PP GF30.
Finally, both materials are particularly resistant to UV light which means it can be safely used for components exposed to direct sunlight like mirror brackets or grille shutters.
Ultrafuse Filaments in Automotive Design Workflow
A new car goes through various design stages before it hits the market. Once the digital design is done, the manufacturer usually begins with the demo stage where new solutions intended for a new vehicle are tested in a refurbished outgoing model.
After building demo cars, the functional concept car is built from the ground up with all the new features including the interior, the chassis, the suspension and so on.
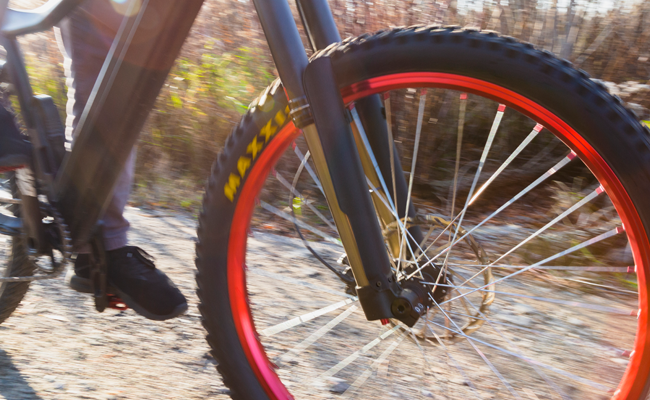
Covers protecting shock absorbers 3D printed with BASF Ultrafuse PP GF30 on Zortrax M300 Dual.
When the manufacturer is happy with those functional concepts, it proceeds to order a couple dozen of pre-production models to test them in various parts of the world and expose them to different driving conditions.
Out of these three main stages of automotive product cycle, 3D printing is heavily used in the first and the second. And a capability to 3D print with PPGF30 and PAHT CF15 that are very likely to be used as target materials in production-level cars certainly makes the life easier for engineers and designers who can get better idea about how a specific part would work in the end-use product.
Ultrafuse Filaments in Automotive Manufacturing Support
Excellent thermal and mechanical properties of PPGF30 and PAHT CF15 make these materials perfect for end-use automotive parts but they can be used on the manufacturing line as well.
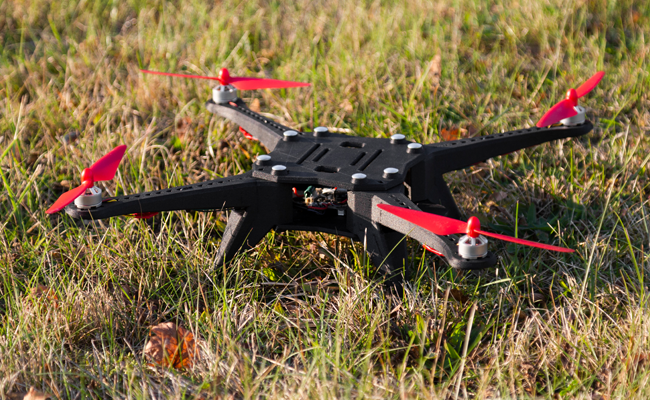
Shock-resistant drone body 3D printed with BASF Ultrafuse PAHT CF15 on Zortrax M300 Dual.
There are various jigs and fixtures that can be 3D printed right at the factory floor to improve the production process. PP GF30 and PAHT CF5 can be used for printing positioning jigs, assembly tools, and different seals and covers. High wear resistance of the both Ultrafuse filaments increases the lifespan of such jigs and therefore generates significant time and cost savings.
Filament for High-Humidity Environments
Third BASF Forward AM filament with wide applications in the automotive industry available for the Zortrax M300 Dual 3D printer is BASF Ultrafuse® PET CF15. It is a polyethylene terephthalate blend reinforced with carbon fiber. BASF Ultrafuse® PET CF15 has high rigidity and mechanical strength, features found in most carbon fiber reinforced materials, but it also has very low moisture absorption. This, combined with heat resistance confirmed up to 108 °C, means parts 3D printed with this filament can easily work in highly humid environments and can be used in contact with various greases and mineral oils. Overall, BASF Ultrafuse® PET CF15 is a good choice for 3D printing mechanically strong designs intended for long, continuous operation like fans or gearbox components.
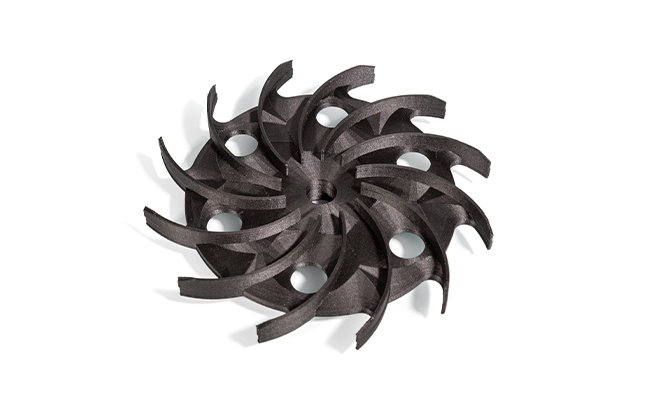
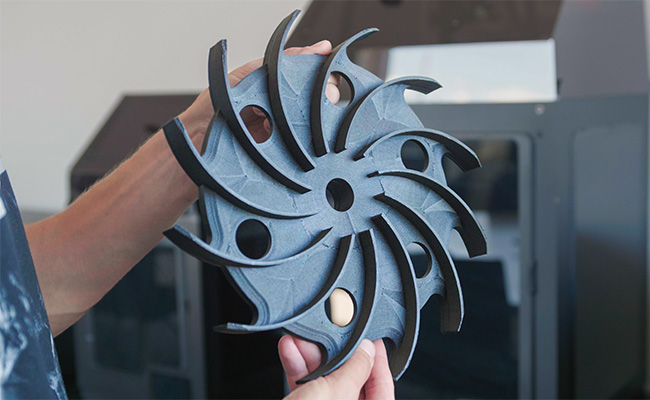
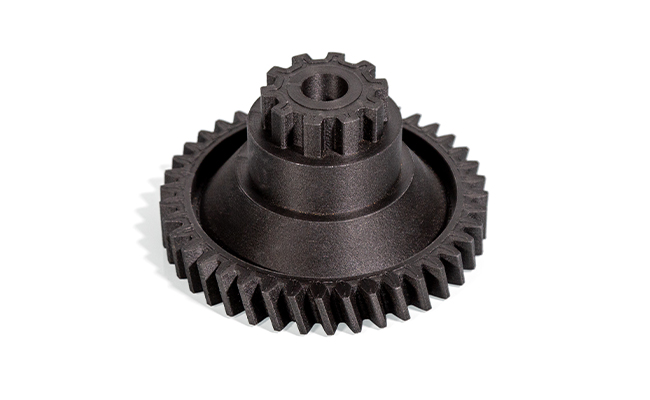
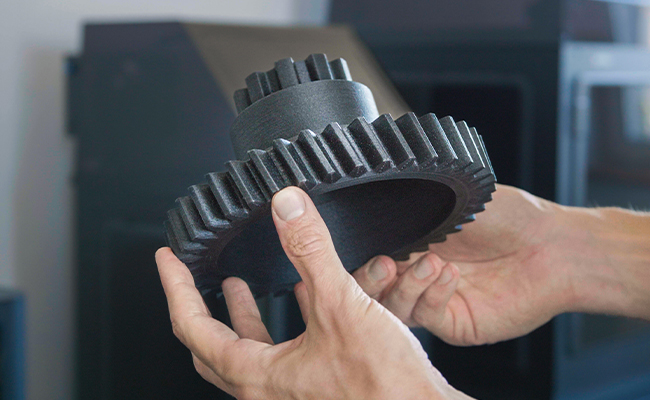
Filaments for automotive industry, compatible with the Zortrax M300 Dual 3D printer, can be ordered at Zortrax Online Store or at your local Reseller’s. Please remember that it is recommended to dry the filaments as directed in the products’ safety data sheets. It is also highly advised to use predefined printing settings to get the best possible results. Ultrafuse PP GF30, PAHT CF15 and PET CF15 have strong abrasive properties, therefore, a hardened steel nozzle with a diameter of 0.6 mm should be used when 3D printing.