3D Printing End-use Parts for Heavy-duty Machines of PMC Harvesters
BACKGROUND: With Industry 4.0 on its way, we observe more and more companies switching to the smart manufacturing. It’s true to all sectors of the industry, no matter the field of operations. It also applies to agricultural equipment, as one of the leaders of the branch is keen on introducing innovative solutions. Since 1970, PMC Harvesters specializes in constructing cutting-edge machines for agriculture. The company operating in Fakenham, England is a part of Ploeger Oxbo Group. Innovation is present in everything they are doing, not only their equipment is filled with latest technology, but they are also implementing the most reliable and productive methods of design and manufacture of their products.
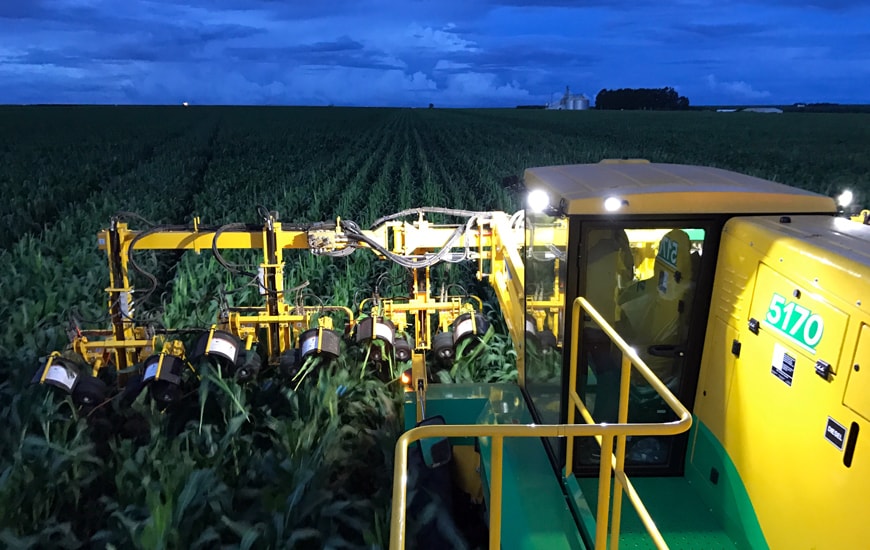
Oxbo 5170 detaseller by PMC Harvesters
THE GOAL: While looking for improvements to their production cycle, the engineers wanted to reduce the costs of machining of certain parts of the vehicle. For the first time, PMC Harvesters used 3D printer during the construction of Oxbo 5170 detassler. Detasseling is delicate process of removing pollen-producing flower from the top of corn. To precisely track the varying height of the plants, the manufactured installed a laser sensor for the measuring system. Furthermore, 5170 can dynamically change the suspension’s height, allowing transformation between field, transport and sport modes. To give you the scale of the vehicle, one could drive a family car under it. Changes in the suspension are measured by four sensors, which required new casings.
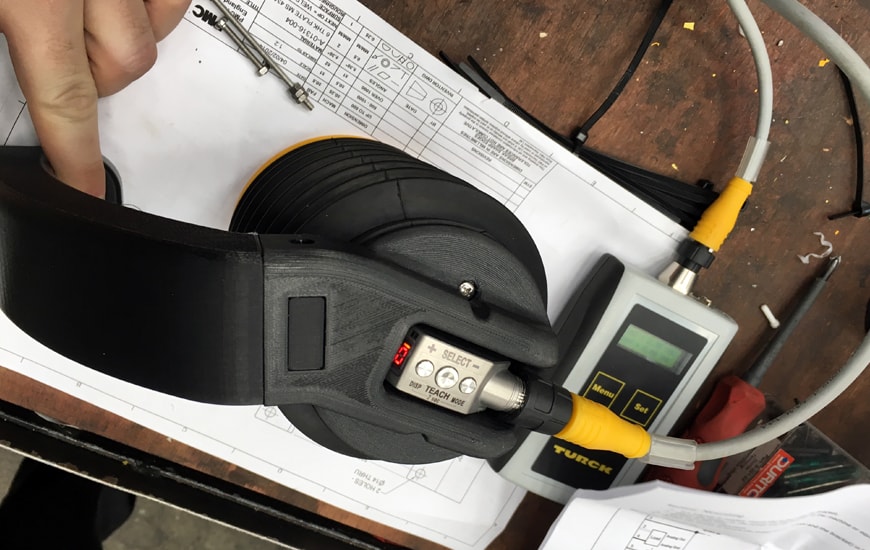
Testing of the 3D printed part
Because the components are located outside of the machine, they needed a reliable protection. The task of devising the new method of designing, testing and producing of the parts was given to the engineer working on Oxbo 5170. Paul Wooding, having previous experience with additive manufacturing, decided to incorporate 3D printing to the process.
THE PROCESS: To complete to rigorous requirements of the heavy-duty vehicle, Paul has chosen Zortrax M200 3D printer and Z-ULTRAT material. The reasoning behind the decision was simple, he wanted to ensure a failsafe repeatability of the printed elements. Initial designs went through careful testing, until the desired form was achieved. In total, the vehicle is equipped with seven 3D printed parts: 4 suspension sensor holders, angle sensor holder, width indicator and speaker holder. All made on Zortrax M200.
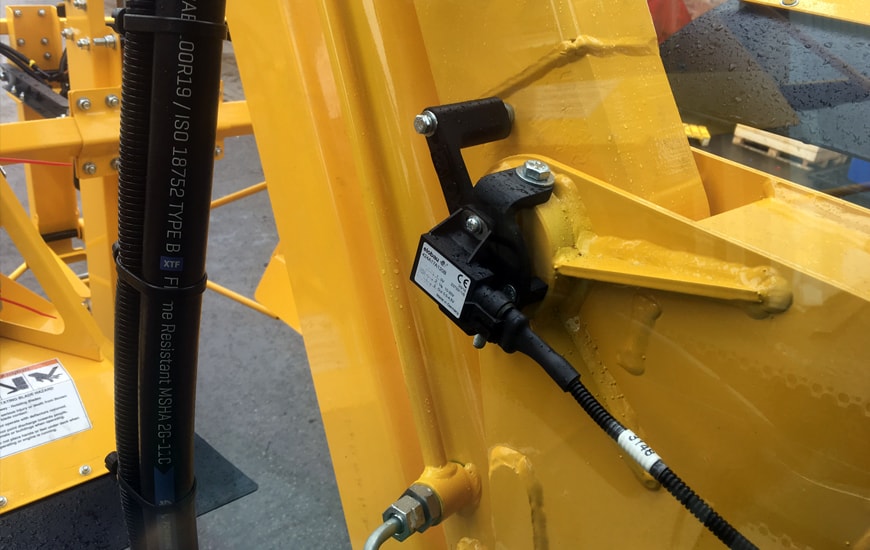
3D printed part installed on the vehicle
Suspension sensor holder consists of two elements: arm and housing for ultrasonic sensor. The main challenge was to design it to accommodate a rotating element inside and at the same time, provide it with protection. Each holder takes less than 19 hours to finish. The second 3D printed part is angle sensor holder. Located in the front of the machine, it measures the angle of the lift arm, to which tools are attached. Besides those, Paul successfully implemented two more 3D printed parts: width indicator for visual measuring of wheel track’s width and warning speaker holder.
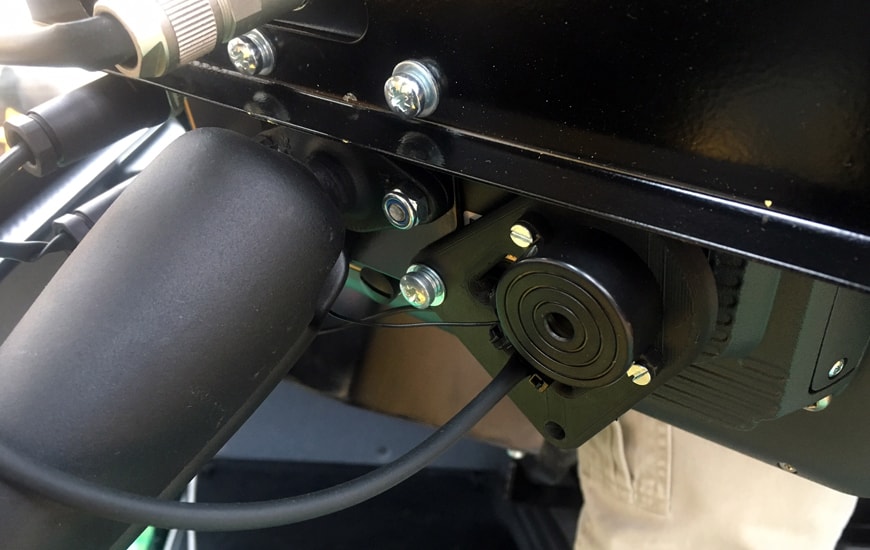
3D printed part installed on the vehicle
THE RESULT: Noteworthy, all the aforementioned 3D printed parts passed tests and were installed on the machines. Zortrax M200 was present in every step of the production process: from the prototyping, testing, redesigning to the final production. Thus, components printed with black Z-ULTRAT became physical parts of the machine. One of the reasons to use this 3D printing material was its remarkable resistance to impact damage. At the same time, its composition makes it long-lasting and highly immune to temperature’s changes. That’s a definite plus, considering the tough conditions in which Oxbo 5170 operates.
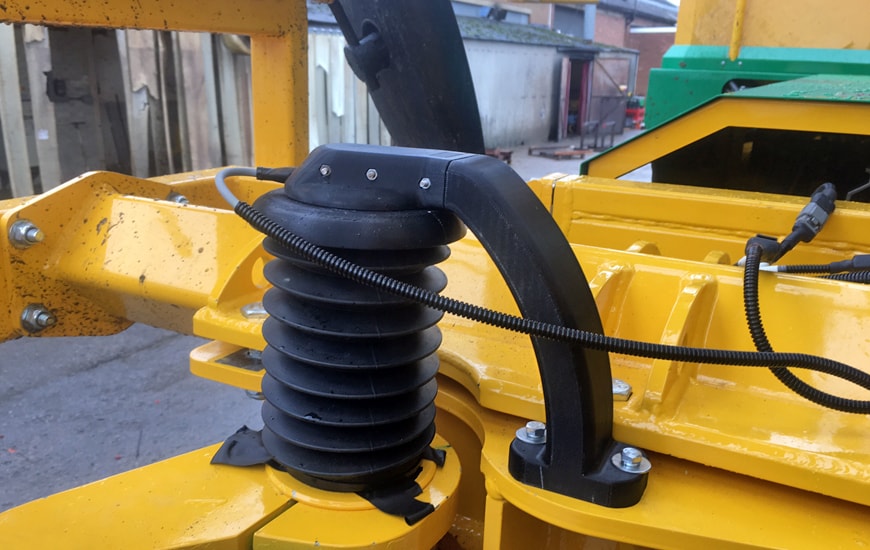
3D printed part installed on the vehicle
THE CONCLUSION: Even though, it was the first time PMC Harvesters relied on 3D printing, they are sure that in future, they are going to use Zortrax solutions again! The production, now in full swing and in a part done on Zortrax M200, is going smoothly. The 3D printers are tirelessly making the new parts for the detasselers. Furthermore, parts are 3D printed so well, that they do not require any additional post-processing. All that Paul has to do, is to remove the supports and occasionally sandpaper them. It greatly saves time, so he can concentrate on other tasks.
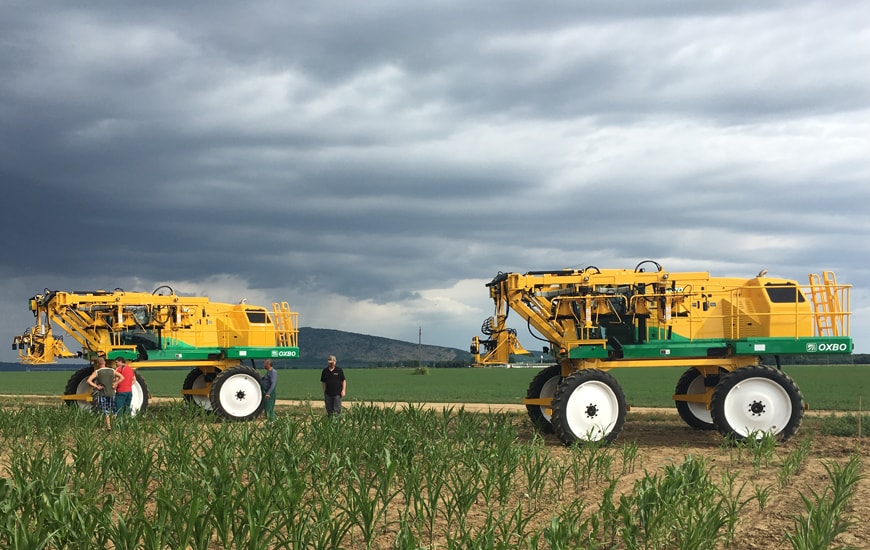
Oxbo 5170 detasellers in the field
As the matter of fact, there’s more about the savings! Additive manufacturing contributes also to the cost-cutting of the vehicle’s production. 3D printing each part is 2/3 cheaper than the regular machining. For example, making one suspension sensor would normally cost $265, while 3D printing it is only $75. The scale of the production makes those numbers even bigger. As the company is planning on replacing next parts with 3D printed versions, Paul is considering purchase of Zortrax M300. Having a substantially larger workspace would open possibilities of 3D printing more elements in one part, while keeping the remarkable quality.