Gear Up for 3D Printing with Zortrax M200
You’ve got to admit that we’re quite persistent in our mission of providing you with examples of successful 3D printing applications. Although we do love challenges, this mission is as far from impossible as you can imagine. Incorporating 3D printing technology is getting more popular each day and we like to think we’ve contributed to the trend by providing reliable and user-friendly 3D printing solutions. There’s more and more Zortrax Ecosystem users out there, who have already gained profits from 3D printing. Are you one of them or are you about to become the next one? Either way, we bet you’ll be interested in one of our latest projects.
Make a Move
Prototyping is a must in variety of industries. It’s especially vital in engineering, robotics and automotive. Checking if the parts work together, testing their shape and size for ergonomics or ensuring that the design turned out exactly as you intended are just a couple of standard proceedings deemed necessary before starting a production line. Traditional prototyping methods, however, tend to consume a lot of resources and, as we all know, time is money. Why waste it when more beneficial ways are easily available? 3D printing technology opens up the possibility of low-cost rapid prototyping. To make a point, we’ve prepared a special model that will encourage you to move forward at full speed. Here’s the Zortrax gear.
On the Outside
Most of us tend to associate mechanical parts mainly with practical use and, unsurprisingly, has less regard towards their appearance. Our gear has been designed with functionality in mind first and foremost. But, as it is, boredom is definitely not one of our strong suits. So, it shouldn’t come as a surprise that we’ve decided to add some flourish to the model and prove that with 3D printing ‘functional’ can be as far away from ‘ordinary’ as you want. Since we do have a soft spot for industrial design and low-cost customization, we’ve focused on giving the gear that appealing modern feel. Strong lines, rectangular shapes, bold colors, semi-transparent walls, LED lights, our gear has it all with cherry on top – the openwork cups. The modern touches not only complement the model but they’re also used to clearly demonstrate the motion.
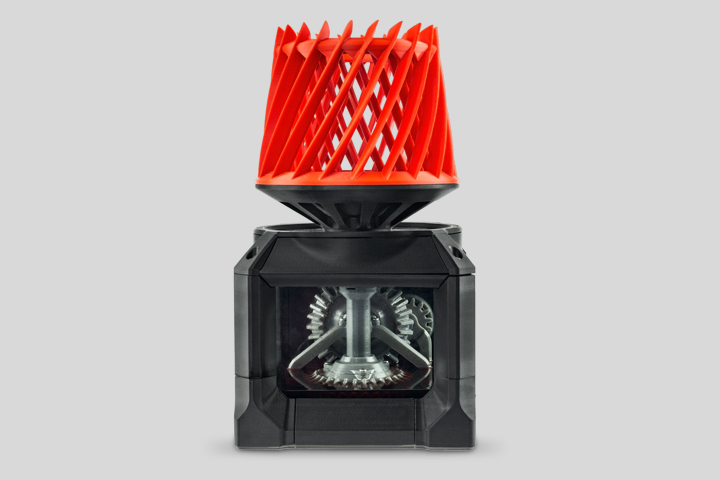
3D printed gearing mechanism by Zortrax
Switch and Turn
If you think that our focus on the gear’s appearance eclipsed the mechanism, you’re in for a surprise. We’ve made sure the outside of our gear matches the inside, not the other way around. To put it simply, the mechanism consists of gear trains connected to a stepper motor. The motor powers up the front and bevel gears, where the direction of motion is changed perpendicularly. The torque is transferred to epicyclic gearing. There, the sun gear activates the inner openwork cup and the ring gear, through planet gears, the outer one. The cups move in opposite directions that can be shifted with just one press of finger. We’ve equipped the model with switches and a knob that give complete control over the movement. One of the switches powers up the mechanism, the other changes the motion direction and the knob regulates the speed.
Clockwork Material
The mechanism, including epicyclic and bevel gear trains, was 3D printed on Zortrax M200 in grey Z-PETG. We’ve chosen this material due to its high resistance to salts, acids and alkalis as well as durability. These features make Z-PETG a go-to material when 3D printing prototypes of mechanical parts or machine components. Its properties ensure that the complete mechanism can be tested in its ultimate environment or a similar one. Combining Zortrax M200, Z-PETG and Z-SUITE software have made high 3D print quality a given. Just look at the sharp edges and accuracy of gear teeth.
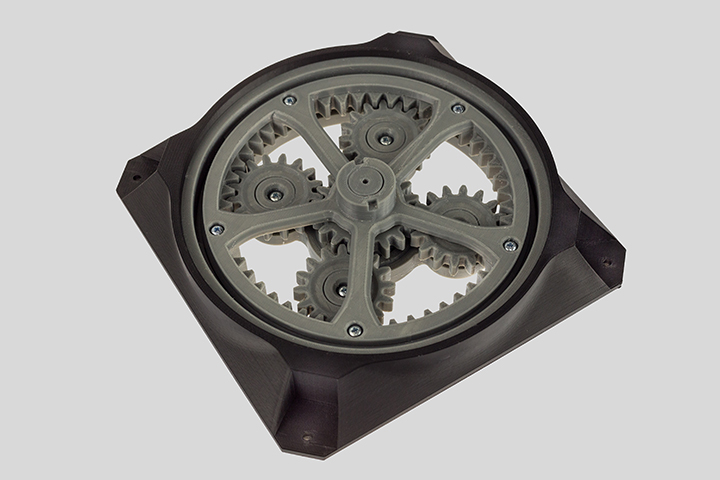
Gears 3D printed with Z-PETG
Mix and Match
Having a vast range of 3D printing materials with various properties at hand, we decided to make the best of them. That’s why, apart from Z-PETG, we 3D printed parts in Z-HIPS and Z-ULTRAT. The motor casing and container support structure were 3D printed in black Z-HIPS. The material’s durability and matte finish made it a perfect choice
for our design. To keep the modern feel of the gear, the upper part of motor casing and openwork cups were 3D printed in red Z-ULTRAT. The matte finish of Z-HIPS and semi-mat of Z-ULTRAT completed the design perfectly and eliminated the need to post-process the 3D printed elements. We also added plexiglass panels used as container walls.
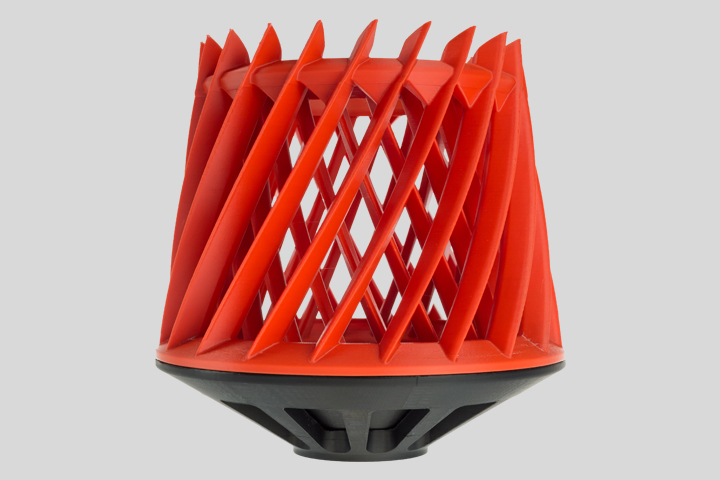
Helix 3D printed with Z-ULTRAT
Full Enclosure
Rapid prototyping offers you the possibility of creating a model for tests, well, rapidly, but that’s one thing. Doing it efficiently is another one. 3D printing technology gives you that and more, meaning with the right material you can test your prototype in the ultimate environment or a similar one. Let’s take engineering or automotive industry and parts that are required to work submerged in liquid as an example. You’d like to make extra sure that the shape and size of your prototype have been designed to fight fluid resistance exactly as you need, wouldn’t you? This is what Z-PETG’s properties have allowed us to do. All the gear trains have been inserted into a special container filled with automatic transmission fluid. So, after making some serious calculations, we’ve been able to see for ourselves how the gears move surrounded with fluid.
PS. Our calculations have been correct, of course, but we’ve had fun while testing.
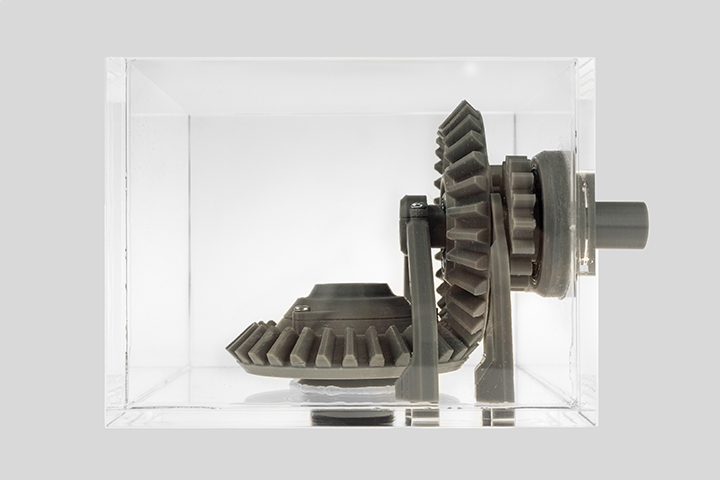
3D printed gears
Piece by Piece
Assembling the gear model was a bit of a challenge, but we do love them, so we got to work eagerly. After removing the support material, we put together the container support structure. Then we focused on the mechanism itself and fixed all the gear trains. The front and bevel gear trains were glued into the plexiglass walls of the container and sealed securely with silicone. The mounting plate for epicyclic gear train was glued into special casing. Next the sun gear and ring gear were glued onto the plate. We then screwed in the planetary gears along with a round gear clutch.
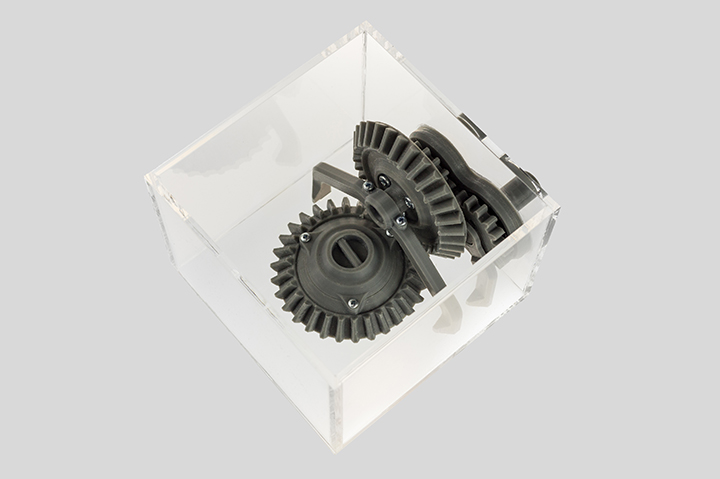
3D printed gears
Power Up
The time for the stepper motor has come. The motor was inserted into the casing. We then set our minds on electronics and wired the switches and the knob and mounted the upper part of the casing. We also attached the LED lights. After wiring it all up, the automatic transmission fluid was poured into the container. Then, the protective plexiglass plate was mounted on the top of epicyclic gear train. Next, we attached the bases for openwork cups and, the final touch, cups themselves. And… it’s on! Take a look at the end result. Quite amazing, isn’t it?
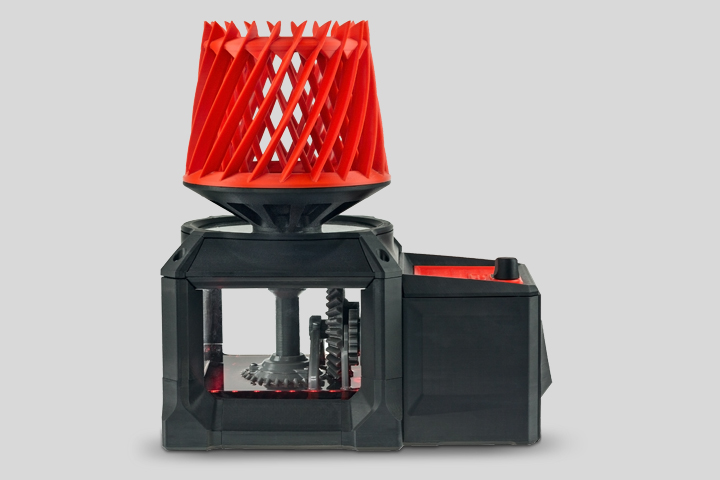
Z-PETG is resistant to salts, acids and alkalis, which allows it to work in demanding conditions.
When it comes to applying 3D printing technology to such industries as engineering or automotive you can’t go wrong. But if you have any doubts, we’ve been providing you with success stories based on incorporating 3D printing for quite some time now. Take a look at our blog or social media and let them inspire you. The advantages and possibilities speak for themselves and our gear just adds to it. Don’t stay behind the competition, become a leader in your industry. We dare you to shift gears and make a move.