Z-SUITE 4.0 Enters an Open Beta Phase: Here’s What You Can Do with It
Summary
- Z-SUITE 4.0 enters an open beta phase and is available for all customers to download.
- The core feature of Z-SUITE 4.0 is choosing different printing settings for different sections of the model.
- Z-SUITE 4.0 enables 3D printing multimaterial parts and brings ways to optimize 3D printing with single filament.
The Z-SUITE 4.0 for a long time has been an internal, custom slicing software Zortrax engineers used internally to 3D print parts made with two different filaments in the most advanced projects like the ones done for the European Space Agency. Now, we’re releasing it as an open beta to all our customers worldwide. Here’s how Z-SUITE 4.0 can help you work faster and more efficiently with your M Plus Series and M300 Dual 3D printers.
How to 3D Print Multimaterial Parts
The core feature of the Z-SUITE 4.0 is an ability to divide the model down into sections with their own, separate printing settings. The first and most obvious way to use this feature is 3D printing models with multiple materials.
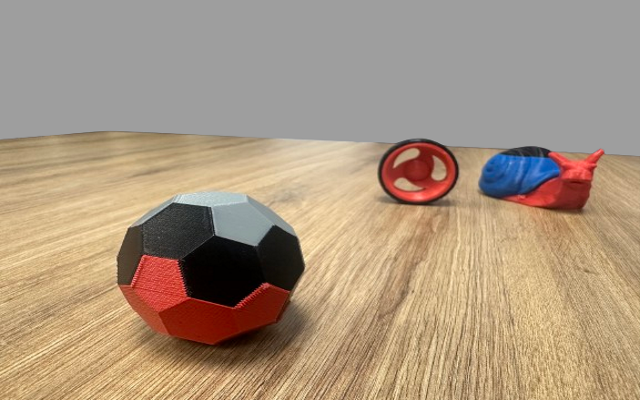
Parts 3D printed with multiple materials using Z-SUITE 4.0.
When designing your parts for multilateral printing in CAD software you need to decide which sections of your part are to be made with which target material.
For example, one of the production jigs made on Zortrax 3D printers at Toyota factory in Poland comprises an ABS body and nylon pins. The body and the pins are designed as separate models, printed separately in two printing sessions, and assembled afterwards. Here’s how Z-SUITE 4.0 can simplify and speed up this process:
Design and Importing:
Designing the multilateral part in CAD software remains unchanged. The difference starts when you import your models to Z-SUITE. Instead of importing the pins and the body to two separate projects you can now import all the models into one project.
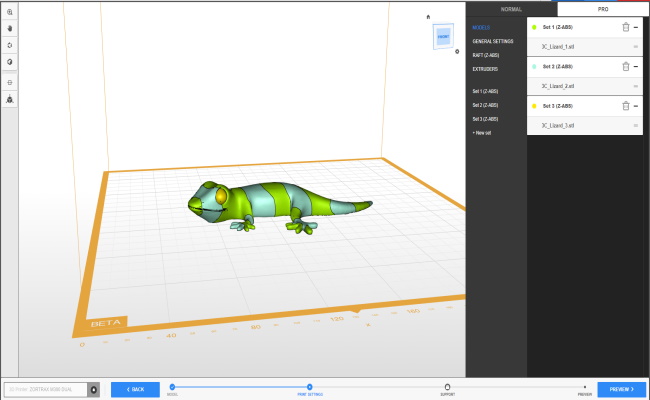
A lizard model divided down into sections imported into Z-SUITE 4.0. Each section is marked with a different color.
Z-SUITE 4.0 will automatically arrange the models on a build platform just as they would arranged in a fully assembled part.
Choosing the Printing Settings:
Once the multilateral part is imported to Z-SUITE and all sections are placed correctly, you can define the printing settings, including the printing material for each section. In the Toyota example you’d need to assign the body to extruder A and the pins to extruder B. Then you just choose the ABS as the printing profile for extruder A and nylon for extruder B.
3D Printing Process:
The 3D printing process of a multimaterial part looks differently depending on whether you have a dual extrusion or a single extrusion 3D printer. In a dual extrusion machine, the printer will automatically switch between extruders to change the material when necessary. In single extrusion M Plus Series 3D printers, Z-SUITE will schedule pauses in the print to let you change the filament manually.
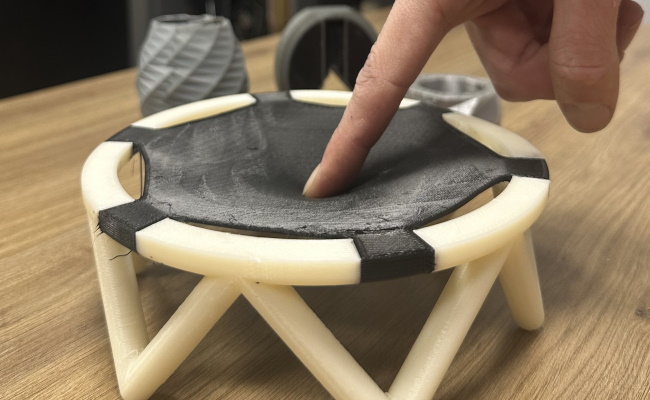
Z-SUITE 4.0 enables combining flexible and rigid materials in a single print.
Since changing the material manually can be burdensome, especially in multilmaterial parts where different filaments are used in every layer, we strongly recommend using the M300 Dual 3D printer for this application.
But Z-SUITE 4.0 offers plenty of features for single extrusion 3D printers as well.
How to Optimize Single Material Prints
The same technique of dividing the model into sections with different printing settings can be used also when all the sections are printed with the same filament. Each section in the model can be printed with different speed, infill type, or even layer height. This can prove useful in a wide variety of applications such as:
3D Printing Topologically Optimized Parts:
Topological optimization is a technique of using advanced computer simulations to identify how stress is distributed in load bearing parts like brake calipers or brackets. The goal is to make the part strong exactly where it needs to be strong and save weight in areas that are not exposed to much stress. In Z-SUITE 4.0 this can be done by manipulating infill patterns – your model can be printed with the strongest, solid infill along the stress lines, and with lighter infill patterns in non-load bearing areas.
Solving the Precision vs Speed Tradeoff:
Reducing the printing speed and layer height usually lead to more precise details but increases the time a 3D printer needs to complete the model. Z-SUITE 4.0 lets you choose the right balance between precision and speed by defining different printing speeds and layer heights for different parts of the model.
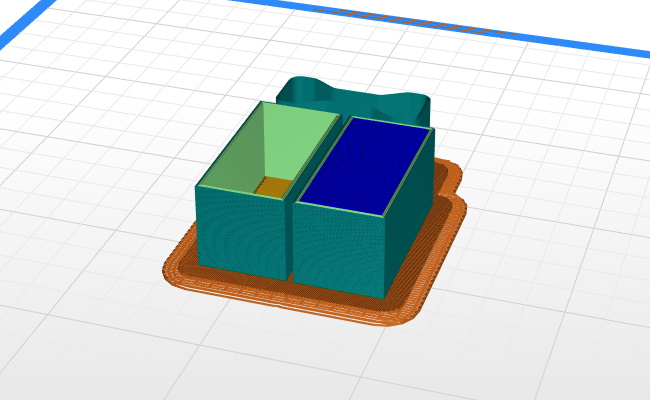
Different printing settings can be chosen for every model placed on a 3D printer’s build platform.
For example when printing a human statue you can have the base 3D printed at high speed with large layer height to get that part done quickly and choose low printing speed and low layer height for the areas with facial features that need to be made with the highest possible precision.
Dealing with Batch 3D Printing
Batch 3D printing relies on placing many different parts in a 3D printer’s build platform to have the entire batch manufactured in one printing session. Z-SUITE 4.0 can help you make this process faster by choosing different printing settings for each model in a batch. For instance, you can choose higher printing speeds and layer heights for parts that do not have small, precise details, and lower printing speeds with lower layer heights for parts that need to be manufactured with narrower tolerances.
Of course, these are just highlights of what Z-SUITE 4.0 can do. All new features are covered in full release notes.
Keep in mind that Z-SUITE 4.0 is still in the open beta phase so make sure to get in touch with us with feature requests and possible bug reports.