Reducing Production Costs with 3D Printed End-Use Items
Summary
- 3D Creative, a Lithuanian provider of 3D printing services, used Zortrax equipment to produce a 3D printed logo for electrically powered city buses made by DANCER bus.
- The logo was made out of Z-ABS and post-processed in several steps, including sanding, painting, and varnishing.
- The 3D models showing DANCER bus's logo can be seen on the buses driving around Klaipėda, Lithuania.
In the recent years, 3D printing has become more and more frequently used in the production of parts implemented in the final products. It turns out that small-series 3D printed items fit perfectly in many types of projects where cost-effectiveness is a vital requirement and there is a need for a flexible customization. Additive manufacturing is the right tool whenever products are made in limited quantities and need unique solutions. Learn how this exact strategy was executed in Lithuania with the help of Zortrax 3D printers.
Supporting Sustainable Solutions with 3D Printing
Back in 2013, DANCER bus, a company based in Klaipėda, Lithuania, came up with an idea of creating an electrically powered city bus. Following the demand to protect natural resources, the company managed to design and develop an innovative vehicle over the next six years. The bus’s design included fast-charging batteries as well as some components made in the large part out of materials from recycled PET bottles. The first two buses were delivered to Klaipėda’s transport system in 2019, creating the so-called zero-emission Klaipėda Bus Park.
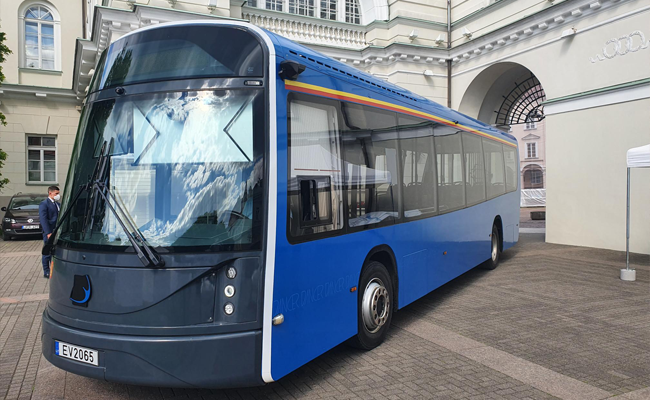
The electrically powered city bus created by DANCER bus ready for use.
But before the buses hit the roads, DANCER bus had been looking for a way to complete their project in the spirit of sustainable production. They decided to finish off the bus’s design with the company’s customized logo installed on the front of the vehicle. For that purpose, DANCER bus commissioned 3D Creative, a Lithuania-based provider of 3D printing services, to create the logo without the need of starting mass production through injection molding.
3D Printing Parts for the Automotive Branch
DANCER bus had their designers prepare two versions of the logo and laid down some requirements for the model’s execution. They wanted it to be as durable and smooth as possible with no visible marks of layers. 3D Creative and their AM engineers had the right experience to perform the task as the company has been successfully operating in the Baltic States region since 2014. They also knew that the possibilities offered by Zortrax 3D printing solutions would help them satisfy their client from the automotive branch. The preparation began in Z-SUITE with choosing the default settings available in the slicer and a 0.19 mm layer. Due to the design of the project and high quality they wanted to achieve, 3D Creative divided the logo into two parts.
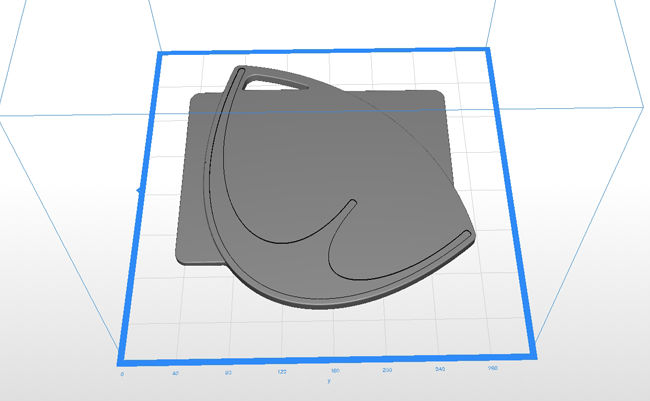
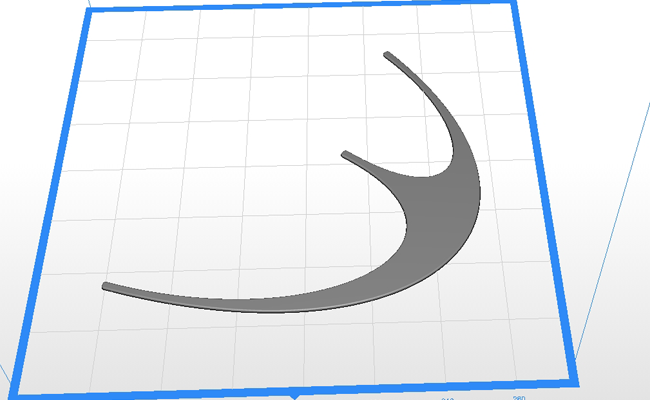
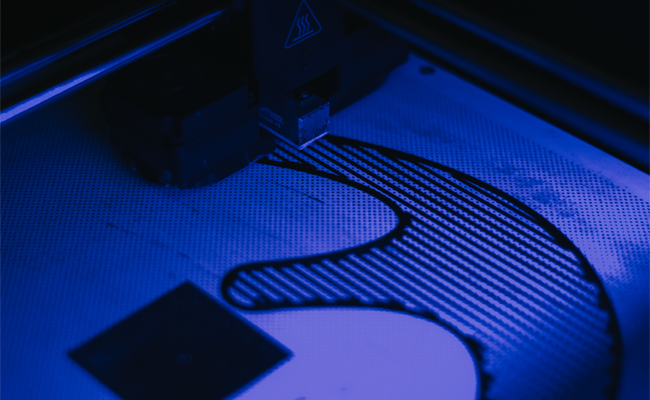
3D Creative’s workshop is made up of 5 Zortrax machines:
- 3 Zortrax M200,
- 2 Zortrax M300 Plus.
Both models were used for the DANCER bus project and, in fact, having machines from two printer lines allowed the team to complete the task in a very short time: “We used the M300 Plus for the bigger parts of the logo, and the M200 for the smaller ones just for optimizing the manufacturing time,” says Indrė Zabielaitė, Chief Staff Officer at 3D Creative. The filament they went for was high-quality and easy-to-use Z-ABS. The 3D printing stage was then followed by thorough post-processing procedures.
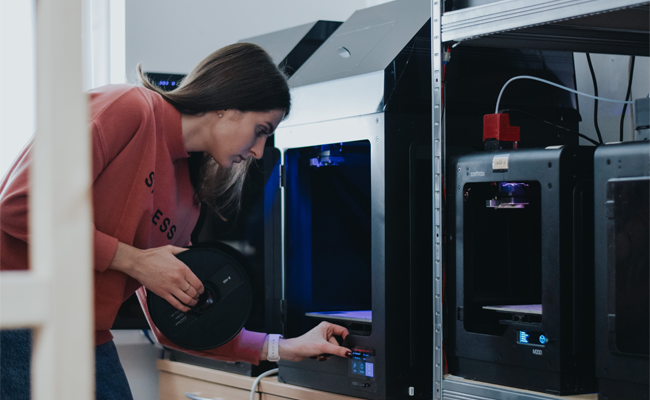
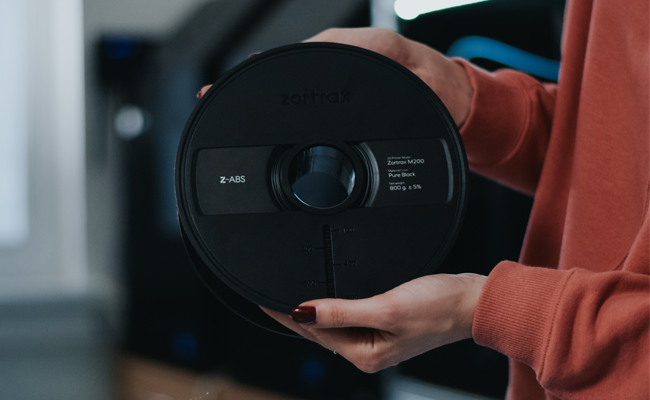
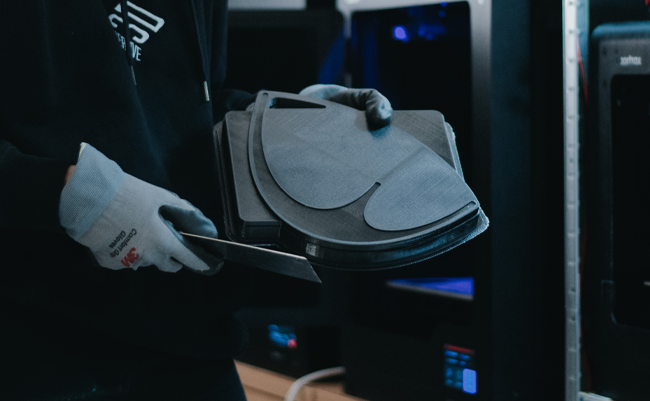
Z-ABS Durability Proved in Practice
Despite initial doubts the team had about this project, they produced 3 sets of the final version of the logo, which have already been attached to the buses that drive around Klaipėda: “The biggest challenge was to produce a product with an absolute capability of withstanding outdoor conditions the whole year – from hot summer to freezing winter. However, it has been almost two years since the 3D printed parts were mounted on the buses and there are still no issues with them,” Indrė remarks.
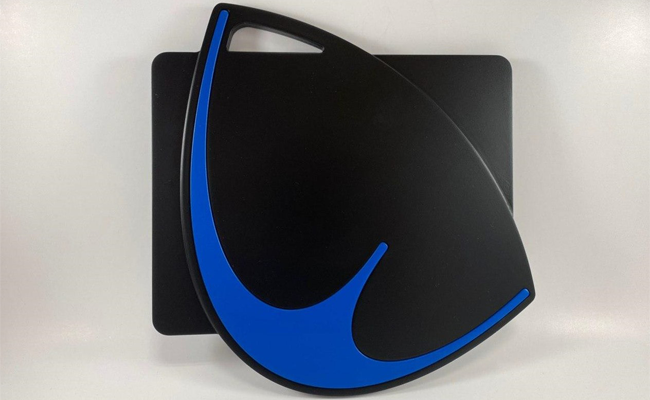
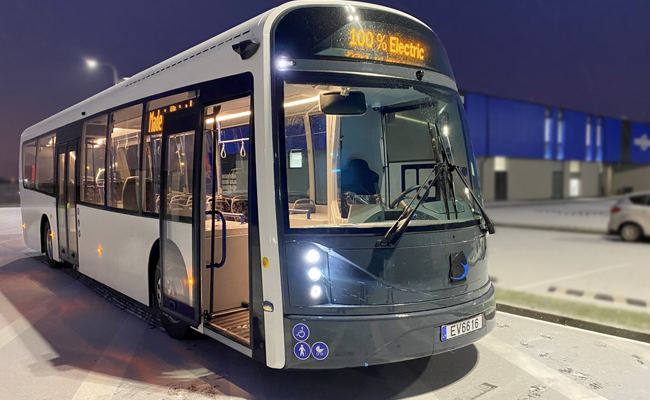
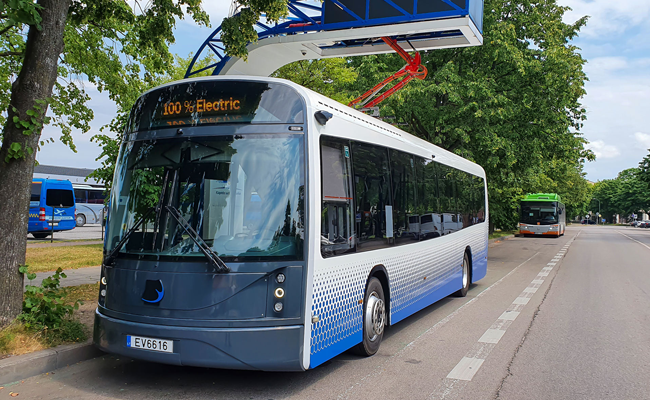
To achieve that, 3D Creative performed sanding of the logo parts and prepared them for painting with an automotive spray primer. Next, the 3D models were painted and covered with a coat of varnish protecting them from humidity and UV light. All in all, post-processing went smoothly as Indrė points out: “It’s easy to post-process 3D prints made with Zortrax devices. Surfaces are very smooth and Z-ABS prints without problems.”
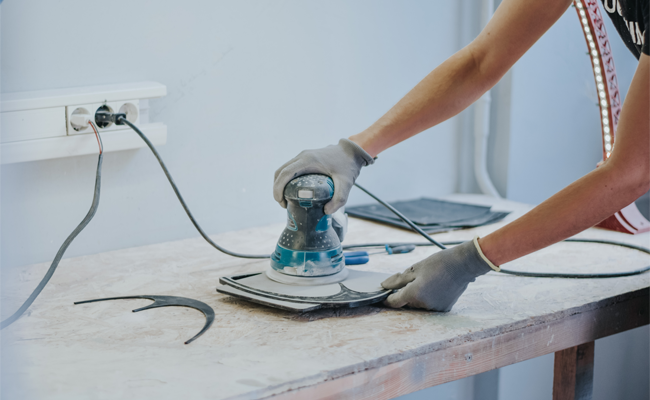
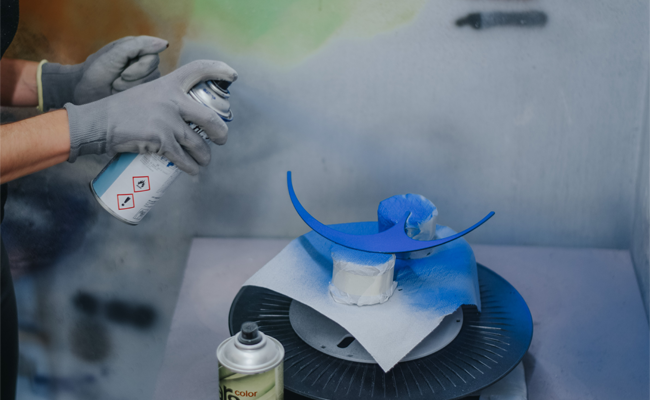
Keeping Costs Low with 3D Printing
Implementing Zortrax machines in a 3D printing business to produce end-use parts such as the DANCER bus logo proved to be the right choice. Compared to other manufacturing techniques, Zortrax 3D printers are cost-effective and leave room for making necessary adjustments and improvements in the project: “Such small-scale production with, for example, injection molding would be very, very expensive and any mistakes would bring huge losses,” Indrė underlines.
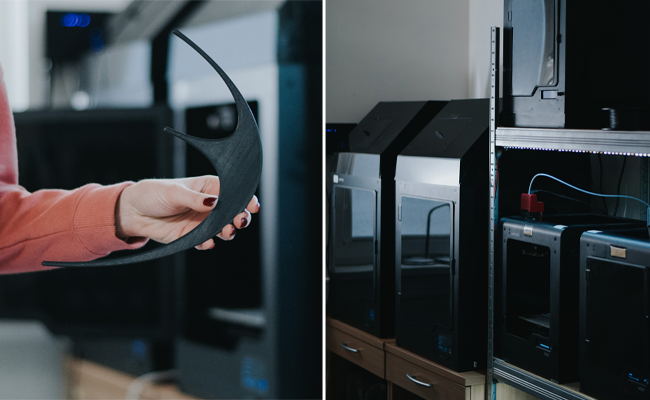
3D printed end-use item (on the left) and Zortrax M200 and M300 Plus 3D printers (on the right).
And since the DANCER bus project was meant to be sustainability-oriented from the very beginning, 3D printing of the logo, which left almost no production waste made the whole project even more coherent and socially responsible.
Learn more about the functionalities of M300 Plus – the 3D printer used in this project.
Read more about the DANCER bus project on their webpage. Special thanks to our Official Reseller in Lithuania – 3D Creative – for contributing necessary information for this article.