Metal 3D Printing Now Possible on Zortrax Endureal
Summary
- Zortrax has introduced metal 3D printing capability to the Zortrax Endureal 3D industrial 3D printer.
- Metal 3D printing is possible due to Zortrax Full Metal Packages - kits with everything necessary to print with BASF Ultrafuse metallic filaments and post-process the printed models into steel parts.
- There are two Zortrax Full Metal Packages providing a capability to make parts of either 316L surgical grade stainless steel, or precipitation hardened 17-4 steel.
Working with BASF Forward AM, one of the largest chemical companies in the world, Zortrax has introduced a process that enables manufacturing of metal parts on the Zortrax Endureal industrial 3D printer out of two most commonly used types of steel: the stainless 316L surgical-grade and precipitation hardened 17-4 PH grade. Bringing metal 3D printing capability to polymer extrusion-based 3D printers marks the opening of the next chapter in cooperation between Zortrax and BASF. Everything there is to know about how it works and how to implement it is covered in detail below.
How BASF-Powered Metal 3D Printing Works
Metal 3D printing on the Zortrax Endureal is possible due to Zortrax Full Metal Package 316L and Zortrax Full Metal Package 17-4 PH kits containing everything necessary to make steel parts.
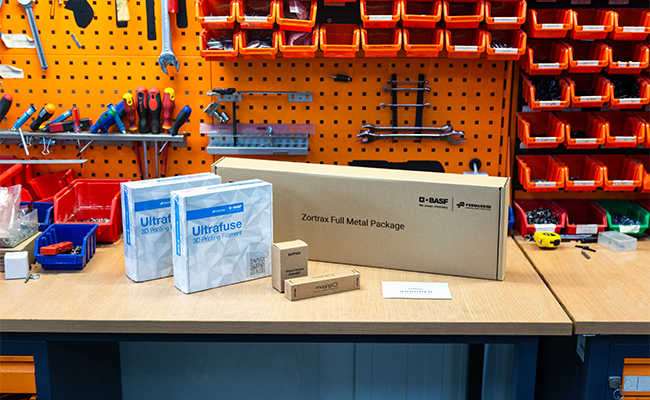
Zortrax Full Metal Packages are kits with everything you need to start 3D printing metal parts on the Zortrax Endureal.
The way all this works is simple.
- First, the hotend module in the Zortrax Endureal 3D printer has to be replaced with the one provided in the kit. It is the same module, but we highly recommend using a new hotend to get the best possible results.
- Second, a spool of either BASF Ultrafuse 316L or BASF Ultrafuse 17-4 PH metallic powder filament has to be installed as the model material and the BASF Ultrafuse Support Layer has to be installed as the support material in the Endureal 3D printer.
- Third, the parts that are to be 3D printed need to be checked for compliance with our design guidelines explained in this Metal 3D Printing Manual.
- Fourth, the build platform in the Endureal has to be covered with Magigoo Pro Metal glue to facilitate proper build platform adhesion.
- Fifth, the 3D printing process has to be started using the default setting available in Z-SUITE software for BASF metallic filaments.
- Sixth, the 3D printed models have to be packed and sent to post-processing which is free with the included post-processing voucher.
- Seventh, post-processed, fully functional metal parts arrive in the mail.
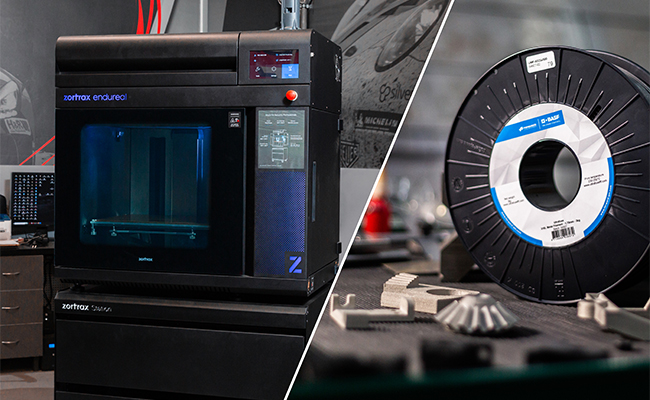
The way to start printing metal parts on the Endureal 3D printers is simple.
To seamlessly go through this process every time, each Zortrax Full Metal Package contains:
- 1000 g spool of either BASF Ultrafuse 316L filament or BASF Ultrafuse 17-4 PH filament
- 300 g spool of BASF Ultrafuse Support Layer support filament
- 50 g bottle of Magigoo Pro Metal glue
- Endureal hotend module
- Post-processing voucher valid for 1000 g of metal parts
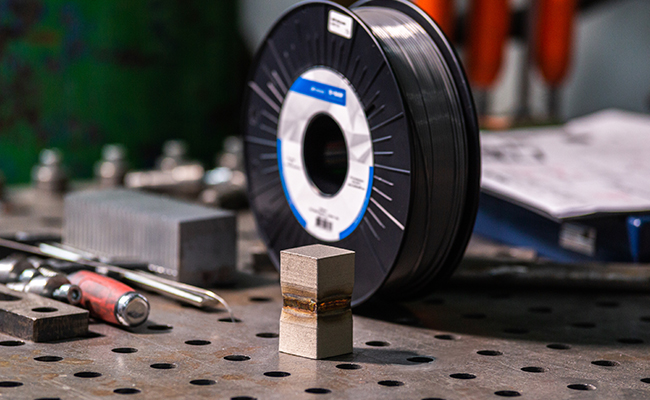
3D printed metal part after welding in the front and BASF Ultrafuse metallic filament spool in the background.
To secure the prints on their way to the Elnik Systems GmbH which is a company responsible for turning them into metal parts, we even threw a bubble wrap in there. Just to keep you on the safe side of things.
Choosing the Right Type of Steel
Each of the two introduced Full Metal Packages comes with a BASF metallic powder filament that enables making parts out of two different types of steel. The first type is a stainless, surgical-grade 316L steel which is particularly resistant to corrosion due to relatively high percentage of chromium present in the alloy. Chromium, when it comes in contact with oxygen, form a very thin protective layer on the surface of your parts that prevents them from corroding.
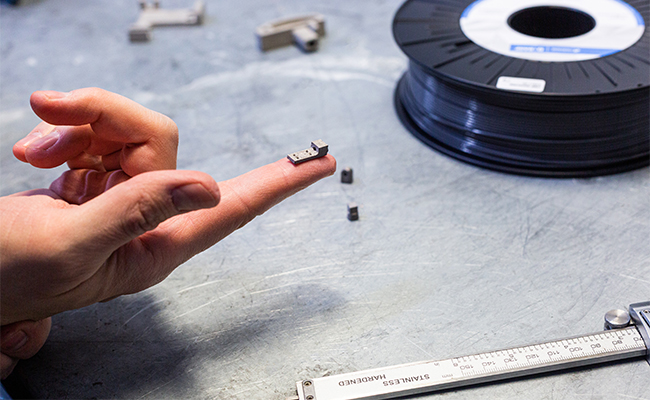
316L steel works well in printing small, precise and non-magnetic parts for precision mechanisms.
This makes it perform good in challenging environments where parts are constantly exposed to liquids, chemicals, or salt. The 316L steel is also aesthetically pleasing, especially after polishing, which makes it a popular choice for decorative applications. This steel, however, is relatively soft and has quite high elongation at break reaching 53%. It will bend rather than break under critical load.
The 17-4 PH steel, on the other hand, is an alloy that has very high hardness due to increased addition of carbon and undergoing a process called precipitation hardening. It is therefore way harder than the 316L type and has a lot lower elongation at break measured at just 4%. This means the material can withstand much higher loads with tensile strength of 1004 MPa which is nearly twice as much as 316L rated at 561 MPa.
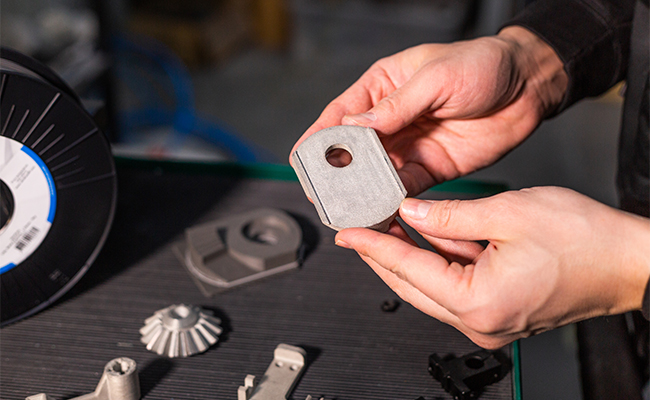
17-4 PH steel is great for stiff structural parts like brackets.
Low elongation, however, means that it would break rather than bend under critical load. The 17-4 PH, although still falling into the stainless steel category, is also significantly more prone to corrosion than 316L type and thus requires more maintenance. Finally, its matt surface has never been considered particularly pretty, so it’s a better choice for scenarios where form is secondary to function.
Key differences between the BASF Ultrafuse 316L and BASF Ultrafuse 17-4 PH are wrapped up in the following table.
Type of steel
|
Corrosion resistance
|
Structure
|
Mechanical performance
|
---|---|---|---|
316L | Stainless | Non-magnetic | Medium harndness / high elongation |
17-4 PH | Corrosive | Magnetic | High hardness / low elongation |
Why the Endureal is the Right Choice for Metals
Zortrax Endureal 3D printer is the first machine in our range to support printing with metallic filaments and there are good reasons for that.
It has a well-designed, dual-extrusion system that has been proven time and time again in printing high-performance components for extremely demanding applications, including space flight. Dimensional accuracy of printed parts is ensured by the heated printing chamber with fully controllable temperature. The standard nozzles used in the Endureal are made of a special kind of industrial bronze that is extremely resistant to abrasion. Considering that especially BASF Ultrafuse Support Layer is a very abrasive material, using nozzles like these significantly prolongs the lifespan of the system and lets it run longer without maintenance.
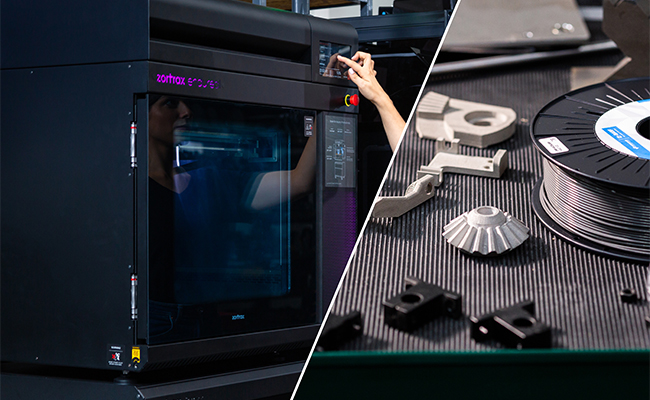
When it comes to 3D printing with metallic filaments, Zortrax Endureal is one of the very best 3D printers on the market.
Finally, because we make both the 3D printer and the slicing software, we could include multiple useful features, such as autoscaling and metal-specific infill type, to name just a few, in our Z-SUITE software that comes free with every Zortrax 3D printer.
All this adds up to one thing – parts 3D printed on the Endureal with metallic filaments have solid internal structure found in traditionally made metal alloys which is the ultimate goal in any metal 3D printing process.
Z-SUITE 3D Printing Slicer Features for Metal Filaments
In the Z-SUITE 3.2.0 BETA update released on 29 May, 2023, we have introduced a set of improvements for 3D printing with metalic powder filaments. The majority of changes relate to the settings of infill, supports, and the shrinkage plate.
First of all, there’s a new gyroid infill pattern, which allows you to 3D print metal models with infill with density range from 60 to 90%. This is particularly useful for cases where the part’s weight has to be as low as possible. Secondly, all support structures are now divided into smaller areas and narrowed at the bottom. Both features facilitate support removal, especially in places that are difficult to access, and reduce the visibility of support marks on models after post-processing. Last but not least, we’ve improved the way the shrinkage plate is printed. Now, this element, which is essential for metal 3D printing, helps to counteract model deformation even better. Take a look at the graphics below where we highlighted the most important features of the Z-SUITE 3.2.0 BETA update.
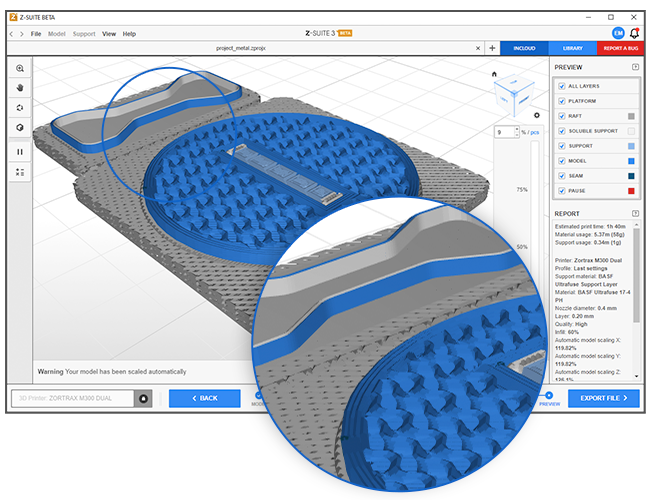
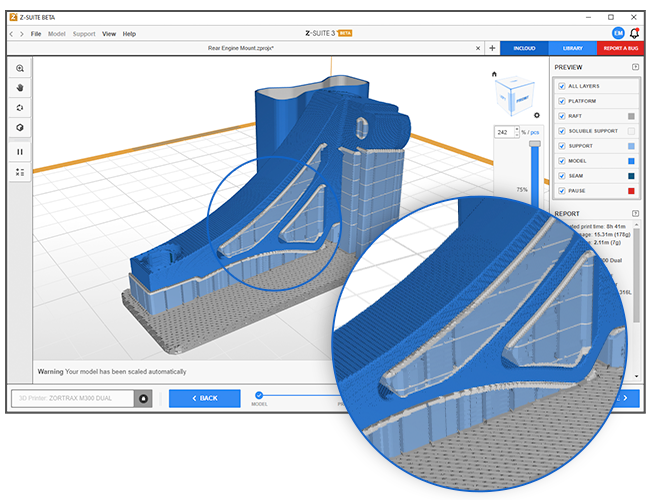
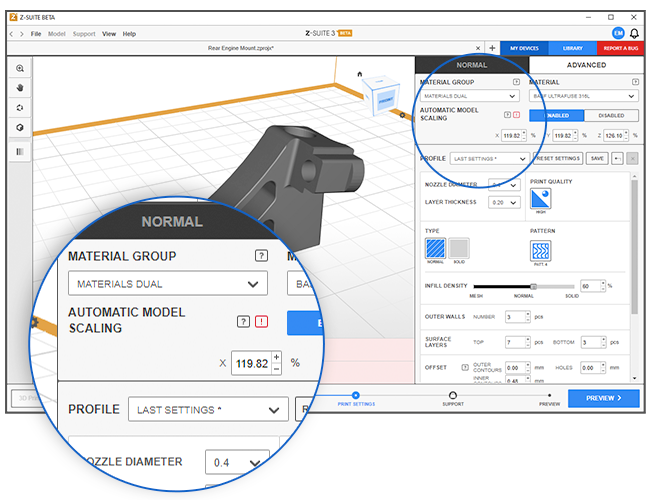
How 3D Printed Parts are Turned into Metals
Once the parts made with Zortrax Full Metal Packages are 3D printed, they need to undergo a post-processing stage developed by BASF Forward AM and performed by Elnik Systems GmbH, a company making the most advanced furnaces in the world. Without going too deep into the details of the process itself, it comprises two key stages.
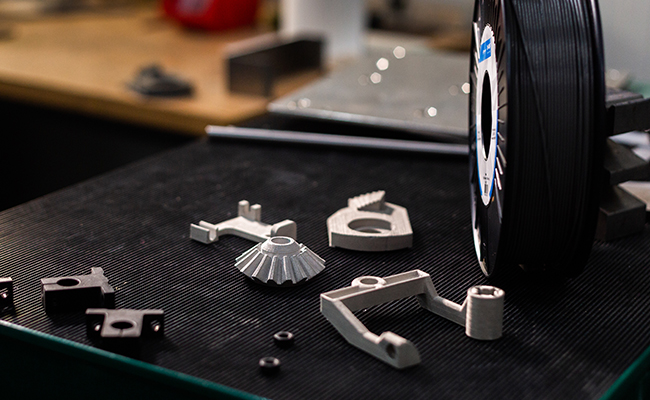
Models 3D printed on the Endureal 3D printer with Zortrax Full Metal Packages retain excellent dimensional accuracy and surface quality even after elaborate post-processing needed to turn then into steel parts.
The first stage is called debinding. Your parts are placed in the furnace and the right temperature is applied to remove the polymer filler from the models. Once this first stage is complete, the furnace enters the second stage called sintering, where parts turn into metal alloys. By applying an ultra-high temperature, the metallic powder left after the polymer filler has been removed is fused into a solid structure of a metal alloy. Finally, the parts are cooled down and taken out of the furnace to be packed and sent back to you.
Most of the design guidelines and limitations explained in our Metal 3D Printing Manual are dictated by the technicalities of this elaborate post-processing. For example, the polymer fillers present in BASF Ultrafuse metallic filaments account for roughly 20% of their volume. That is why the parts shrink 20% after the debinding stage. Size limit for the metal 3D printed parts is simply there to make them fit into Elnik furnaces.
Working with 3D Printed Metals
After the post-processing, the parts made with Zortrax Full Metal Packages can undergo all kinds of post-processing typically employed to give finishing touches to metals.
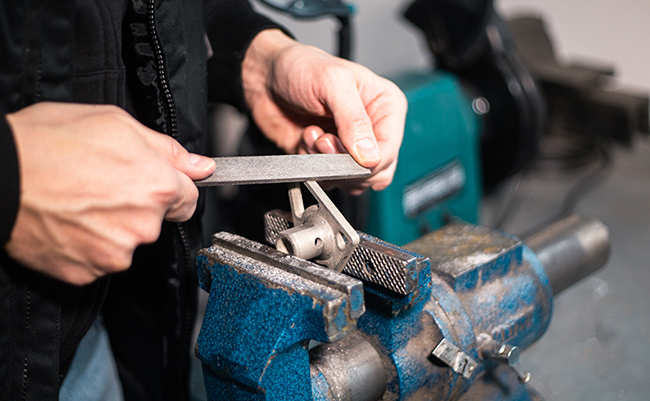
3D printed steel can be sanded just like standard steel.
Holes included in the designs can be threaded to make place for screws or bolts. Parts can be welded together with no problem or sterilized if needed. 3D printed steel can also be polished to achieve mirrored surfaces wherever necessary or sanded to get the dimensions right down to a fraction of a millimeter. Basically, 3D printed steel behaves like any other steel.
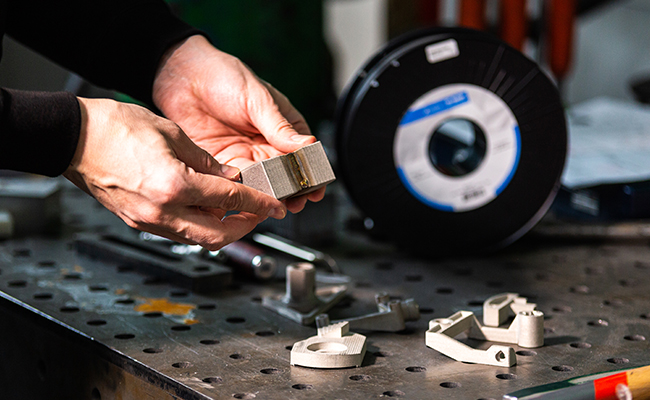
Due to internal structure indistinguishable from traditionally made steel, the 3D printed metal parts can be easily welded.
Knowing that the metal 3D printing process is a bit more complex than using standard polymer filaments, we prepared a host of detailed guidelines and manuals. You can find them all here.
If you can’t find what you’re looking for in there, just get in touch with our Support Center. They’ll be happy to answer all your questions.