Wykorzystanie żywicznego druku 3D w sektorze DIY: Budowa panelu świetlnego
Cristiana Felgueiras, znana jako Get Hands Dirty, to popularna YouTuberka DIY (do-it-yourself), specjalizująca się głównie w meblarstwie, której kanał opiera się na “tworzeniu rzeczy własnymi rękoma”. W swojej pracy wykorzystywała już wiele technik produkcyjnych, m.in. rzeźbienie w drewnie. Po niedawnym włączeniu druku 3D do swojego rzemiosła zauważyła, jak korzystna może być ta technologia w sektorze DIY. Wykorzystując żywiczną drukarkę 3D Zortrax Inkspire, zaprojektowała i zbudowała niesamowity panel świetlny. Oto jak wygląda.
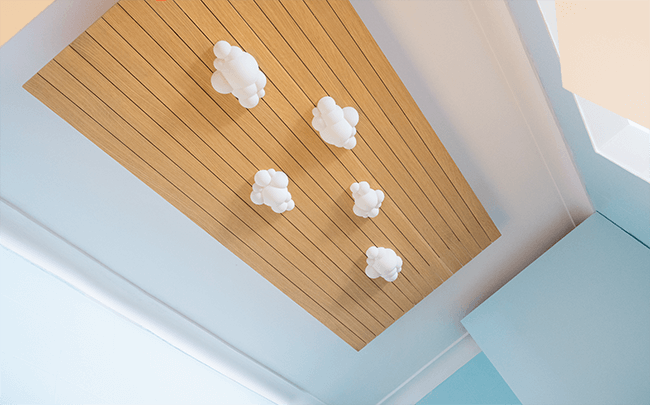
Gotowy projekt panelu autorstwa Get Hands Dirty.
Użycie drukarki 3D Zortrax Inkspire okazało się świetnym rozwiązaniem do tworzenia zaokrąglonych kształtów lamp do panelu, ale także znacznie ułatwiło cały proces produkcji. Jak to ujęła Cristiana: “Ręczne modelowanie pewnych form i kształtów jest naprawdę trudne. Fakt, że mogę nacisnąć przycisk i uzyskać wiele kopii tego samego obiektu jest niesamowity i znacznie zmniejsza czas i wysiłek poświęcony na dany projekt.” Jak zatem wyglądała budowa unikatowego panelu świetlnego krok po kroku?
Projektowanie i drukowanie modeli 3D
Krok 1: Projektowanie cyfrowe
Cristiana rozpoczyna proces twórczy od zaprojektowania pożądanych elementów w programach do modelowania 3D. Używa SketchUp dla form geometrycznych lub Fusion 360, gdy ma do czynienia z bardziej organicznymi kształtami. W przypadku projektowania cyfrowego “dużo łatwiej jest uzyskać produkt o ściśle określonych wymiarach, prostopadłych kątach, równomiernie rozmieszczonych detalach i geometrycznie doskonałych kształtach” – podkreśla Get Hands Dirty. Projektowanie cyfrowe okazało się więc bardzo przydatne w przypadku lamp w kształcie chmur potrzebnych do panelu, ponieważ trudno jest uzyskać tak nieregularną formę ręcznie.
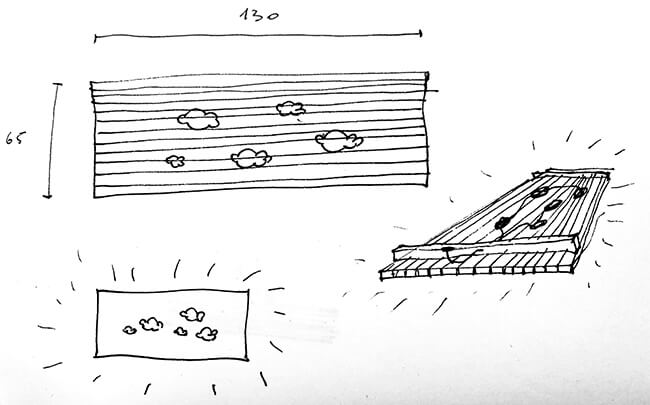
Zanim projekt zostanie stworzony w programie do projektowania, a następnie przygotowany w Z-SUITE, Get Hands Dirty szkicuje go na papierze.
Modele 3D są następnie przygotowywane do druku w Z-SUITE, dedykowanym oprogramowaniu dostarczanym wraz z wszystkimi maszynami Zortrax. Ponieważ Z-SUITE został zaprojektowany tak, aby automatycznie dobierać najbardziej optymalne parametry dla danego projektu, nie ma potrzeby wiele w nich zmieniać. “Zazwyczaj utrzymuję automatyczne ustawienia w Z-SUITE i używam wysokość warstwy 0,05. W zależności od projektu mogę zmniejszyć grubość i gęstość podpór, aby zapobiec uszkodzeniu modelu podczas jego przycinania” – mówi Get Hands Dirty. Po dostosowaniu ustawień związanych z podporami twórczyni przechodzi do procesu produkcji.
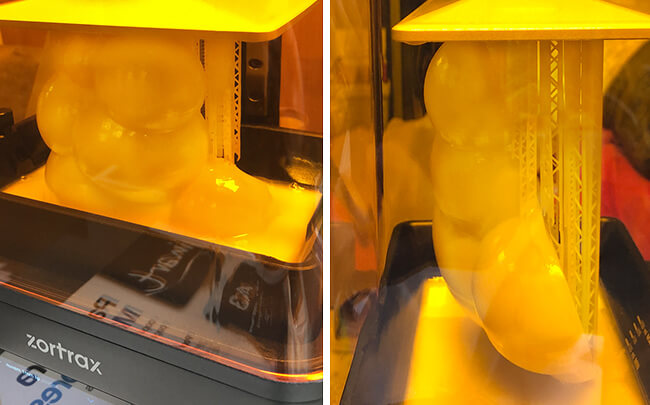
Modele w kształcie chmur podczas procesu druku 3D z żywicy na Zortrax Inkspire.
Krok 2: Drukowanie 3D z żywicy
Na tym etapie Cristiana wybiera żywice, z których będzie drukować swoje modele. Dwie żywice Zortrax BASIC, dostarczane w pakiecie razem z Inkspire, są odpowiednie dla większości jej projektów. W zależności od efektu, jaki chce uzyskać, najczęściej wybiera żywice szarą i białą. Pierwsza z nich stanowi doskonałą bazę dla wszystkich modeli, które będą później malowane, natomiast druga sprawdza się idealnie, gdy docelowe modele mają być białe. Choć ten uniwersalny duet influencerka stosuje do wielu różnych projektów, to na tym nie kończy się gama żywic, które chce wypróbować. Jak sama stwierdza: “Używam żywic fotopolimerowych głównie w kolorze białym i szarym, ponieważ, szczerze mówiąc, te materiały są bardzo wszechstronne. Planuję wypróbować jeszcze te półprzezroczyste i elastyczne.” Ponieważ lampy w kształcie chmur są białe, żywicą wybraną przez Cristianę do tego projektu była Zortrax Resin BASIC w tym właśnie kolorze.
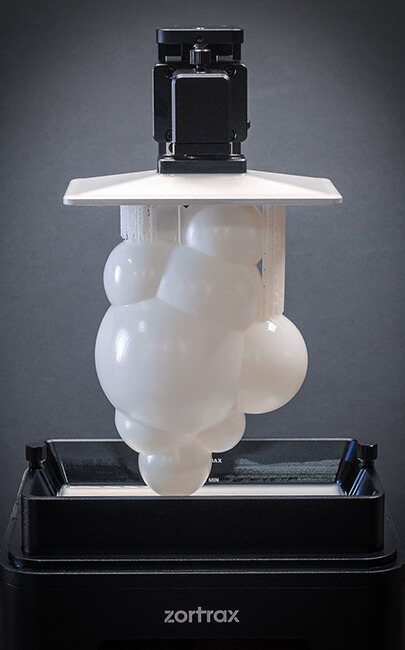
Drukarka Zortrax Inkspire jest idealna do tworzenia skomplikowanych kształtów w 3D.
Metody obróbki końcowej
Krok 3: Czyszczenie i usuwanie podpór
Po zakończeniu procesu drukowania z żywicy, Get Hands Dirty czyści wydruki i usuwa podpory, umieszczone w Z-SUITE, aby zapobiec zapadaniu się niektórych fragmentów danego modelu. Następnie pozostawia wydruki na słońcu. Zabieg ten przyspiesza utwardzanie modeli 3D drukowanych w technologii UV-LCD i przygotowuje je do dalszych etapów obróbki końcowej. Tutaj dobór stosowanych technik zależy w dużej mierze od kształtu i przeznaczenia danego modelu. Czasami szlifuje jego powierzchnię, aby nadać mu gładkość. Innym razem wywierca otwory, które zapomniała dodać do modelu podczas jego projektowania. Najczęściej jednak po usunięciu podpór projekty nie wymagają dalszej obróbki. Tak było w przypadku projektów lamp. Były praktycznie gotowe zaraz po tym, jak Cristiana oczyściła wydruki i pozbyła się niepotrzebnych fragmentów materiału podporowego.
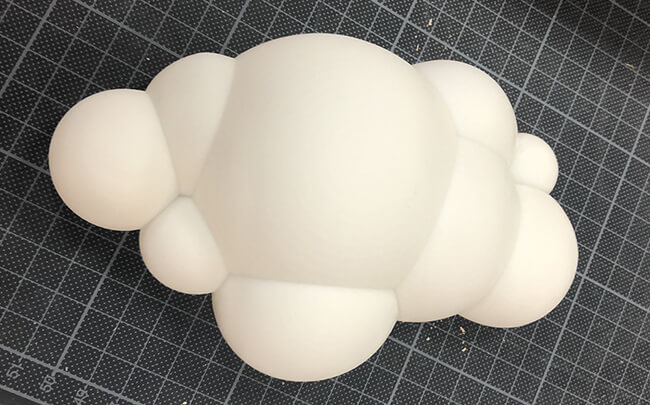
Wydruki z kloszem nie wymagają zbyt wiele obróbki końcowej: wystarczy usunąć podpory.
Krok 4: Montaż wszystkich części
Aby zmontować panel świetlny, gotowe do użycia części wydrukowane w 3D muszą zostać połączone z podstawami, a następnie przymocowane do drewnianego panelu. Zarówno podstawy, jak i drewniany panel zostały wcześniej przygotowane przez Get Hands Dirty – zadbała ona o dokładne połączenie wszystkich części elektrycznych, zapewniając ich prawidłowe działanie. Po połączeniu wydrukowanych w 3D form w kształcie chmur z panelem, Cristiana uzyskała efekt końcowy: unikalny panel świetlny. Można go teraz wykorzystać do oświetlenia i udekorowania dowolnego pomieszczenia.
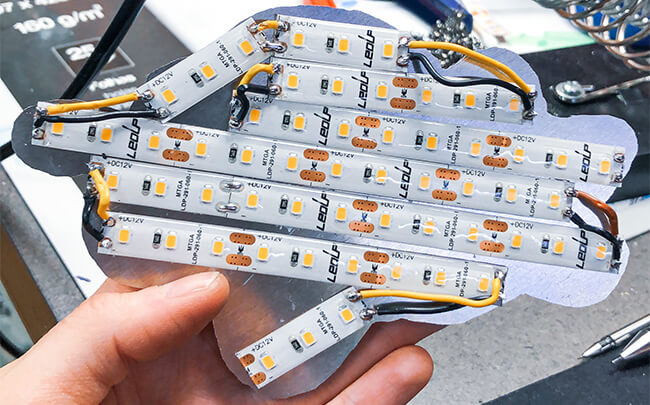
Klosze lamp w kształcie chmur należy połączyć z częściami elektrycznymi.
Jak podkreśla Get Hands Dirty, proces DIY jest o tyle satysfakcjonujący, że można otaczać się ręcznie wykonanymi przedmiotami, które są nie tylko piękne, ale i pragmatyczne. “Lubię eksplorować różne pomysły, od dużych do bardzo małych rozmiarów, a ostatnio inspiruje mnie przede wszystkim potrzeba posiadania wokół siebie funkcjonalnych elementów” – twierdzi. Panel świetlny, który stworzyła przy użyciu Zortrax Inkspire, jest doskonałym przykładem połączenia estetyki z użytecznością. Przekonawszy się o korzyściach płynących z posiadania drukarki 3D w swoim warsztacie, Cristiana Felgueiras poleca ją teraz “każdemu, kto chce wcielić w życie pomysły, które trudno zrealizować ręcznie”.
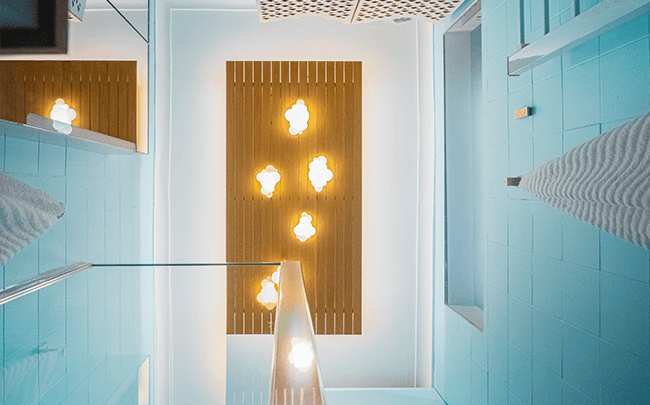
Panel stworzony przez Cristianę Felgueiras zainstalowany w łazience, aby rozświetlić jej wnętrze.
Odkryj inne zastosowania drukarek 3D i materiałów Zortrax w artykułach opublikowanych na oficjalnym blogu Zortrax.