An Innovative Merge of Music and 3D Printing
Summary
- Ryan Pereira, an acclaimed clarinet player, uses Zortrax M200 and M300 Dual 3D printers to customize and repair clarinets.
- He successfully creates instrument accessories with Z-ABS, Z-HIPS, and external materials.
- Apart from 3D printing accessories for his very own clarinet, Ryan also helps other artists which allowed him to establish a fully-fledged company.
The musical instrument manufacturing industry is a resilient sector of the global economy. Every year it generates billions of dollars of revenue and is expected to grow even more in the upcoming years (source dnb.com). This industry comprises of large corporates, such as Yamaha, Roland, or Steinway, which offer professional instruments to artists worldwide. Yet among these global giants, there are small companies using unconventional manufacturing methods to produce high-end musical devices. Here’s a story about how the world of 3D printing has entered the world of music.
3D Printing and Physics Combined
Back in 2014, a classically-trained clarinet player, Ryan Pereira, founded Pereira 3D Clarinet Services – a shop based in Philadelphia where he produces custom clarinet and other instruments accessories, repairs woodwind instruments. For these purposes, he has successfully adapted 3D printing with Zortrax printers.
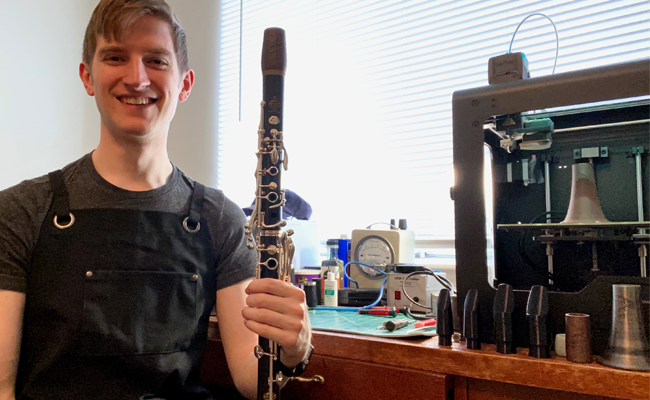
Ryan Pereira in his workshop with his Buffet Crampon clarinet equipped with 3D printed accessories.
Ryan Pereira has always expressed interest in customizing his equipment to better match his playing needs, and coming from a family of engineers, he has had great help in combining technical aspects of manufacturing with his musical artistry. However, Ryan was able to fully develop his potential only when his father Carlos M. Pereira introduced him to 3D printing. Carlos is an electrical engineer who completed his PhD in electromagnetism and semiconductors. He put greater focus on the way electromagnetic waves carry and deliver energy when they interact with various geometries. Both Ryan and Carlos were eager to experiment with designs for physical musical devices.
“With Ryan’s perceptions, input, and desire to succeed, I thought that a design method which allowed the manipulation of geometric features in a CAD 3D program, and then transferred to a file format that is understood by a FDM machine, could be a very powerful tool.” – says Carlos M. Pereira.
Working together, they gained appropriate knowledge and motivations that developed into a real capability of creating accessories of musical instruments using additive manufacturing. Therefore, Ryan went on to trying out 3D printing to produce clarinet barrels, bells, and mouthpieces.
The Perfect 3D Printing Tools
These accessories are traditionally made out of a vast majority of hard woods. As Ryan says, wooden clarinets are prone to cracking due to temperature differences and moisture. He even claims that some clarinet elements can become deformed over the initial months of playing. Facts Ryan Pereira has began work with 3D printers 7 years ago He exclusively uses Zortrax M200 and Zortrax M300 Dual 3D printed clarinet items Ryan manufactures are up to 50% less expensive than aftermarket traditional clarinet products
This was yet another reason that led Ryan to apply 3D printing in his work. He decided to equip his workshop with a set of Zortrax M200 and M300 Dual 3D printers and began work on items for his clarinet. Zortrax devices turned out to be the perfect match for his project. “I find them very reliable and I can get very consistent results with both Zortrax filaments as well as external filaments.” – remarks Ryan.
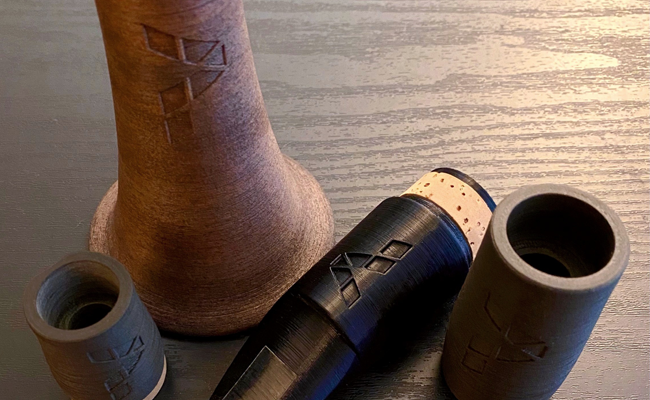
3D printed clarinet accessories: bell, barrel, and mouthpiece.
What he also noticed was that 3D printing filaments allowed him to improve the durability of the elements which are so susceptible to changing conditions: “Wood/PLA filaments make for stable materials over the life of the product. In addition, they’re incredibly lightweight, and my clarinet barrels and bells run almost half the weight of traditional wooden products.” Being able to replicate expensive manufacturing materials in woodwind instruments helps Ryan eliminate high costs of repairs. The synthetic version of the clarinet barrel Ryan makes with 3D printers costs $50, whereas traditional custom barrels can range around $200-$300.
Perfecting Prototypes and Producing Final Parts
In the process of learning how to adapt 3D printing in clarinet accessories production, Ryan had made nearly 1000 prototypes before he perfected the final versions.
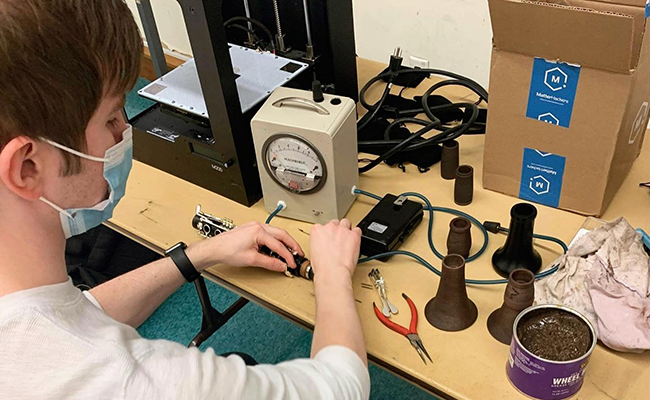
Ryan Pereira installing 3D printed elements onto an analog clarinet.
“It’s a very extensive process to create a production model for something so intricate as a musical instrument, but you truly have to ensure each part functions properly and produces a beautiful sound.” – emphasizes Ryan.
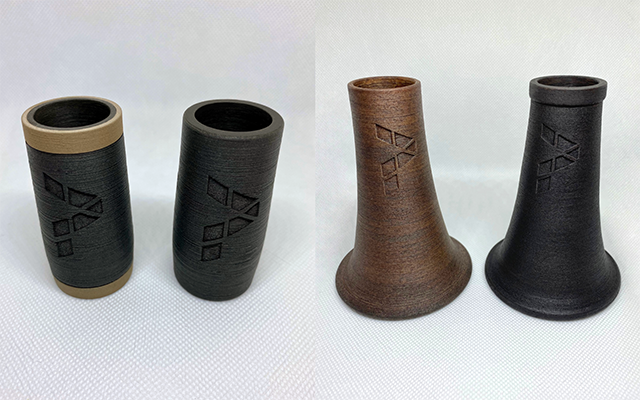
3D printed clarinet barrels and bells after post-processing.
Apart from 3D printing, his workflow involves many post-processing stages, such as:
- sanding the outside surface,
- filing the bore to adjust internal dimensions,
- reaming sockets on the ends of the printed items,
- staining parts with oil-based wood stain,
- sealing surfaces with wax or oil,
- 3D printing metal rings from bronze/PLA filaments.
The rest of clarinet items follow similar production processes.
Customizing Musical Instruments
Fantastic results Ryan was able to obtain with Zortrax 3D printers forced him to widen the scope of his business. He continued to help other clarinetists and artists who play niche instruments, such as bagpipes, by successfully repairing their work tools. With such projects, prior to designing and 3D printing models, Ryan takes necessary measurements so that the instrument will sound properly for the player.
Facts Ryan’s workflow involves at least 6 stages of post-processing after 3D printing clarinet items Ryan chooses Z-ABS and Z-HIPS for their high surface quality 3D printing filaments allow him to reduce the overall weight of the instrument Clarinet bells and barrels Ryan makes are about 43% lighter compared to their wooden counterparts He also takes into account the aesthetic aspects of his projects. For that reason, he uses Z-ABS and Z-HIPS in various shades. As he thinks, these filaments require little post-processing after printing.
“I do plenty of custom work for artists. Speaking functionally, I craft many products with custom dimensions to either match equipment they currently use (make a copy) or to fit an instrument brand that’s not as popular and features different-sized joints… There are so many options for personalization with 3D printing!” – points out Ryan.
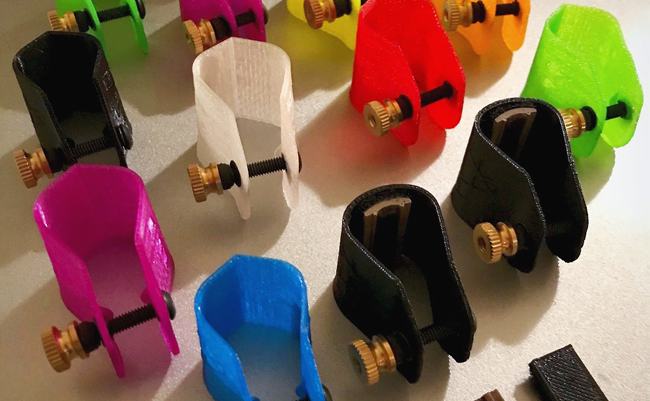
3D printed customized clarinet ligature bodies with a screw mechanism. These items are installed on the clarinet mouthpiece.
Over the years, Ryan has supported many American artists who reach international success. All of them claim that Ryan’s 3D printed products are completely reliable and perfectly fitted to their individual style of playing, providing refined sound in their performances. Also, for musicians who struggle with repeated tendonitis, having an instrument with reduced weight is game-changing during lengthy rehearsals and performances. 3D printed barrels and bells are about 43% lighter compared to their traditional wooden counterparts.
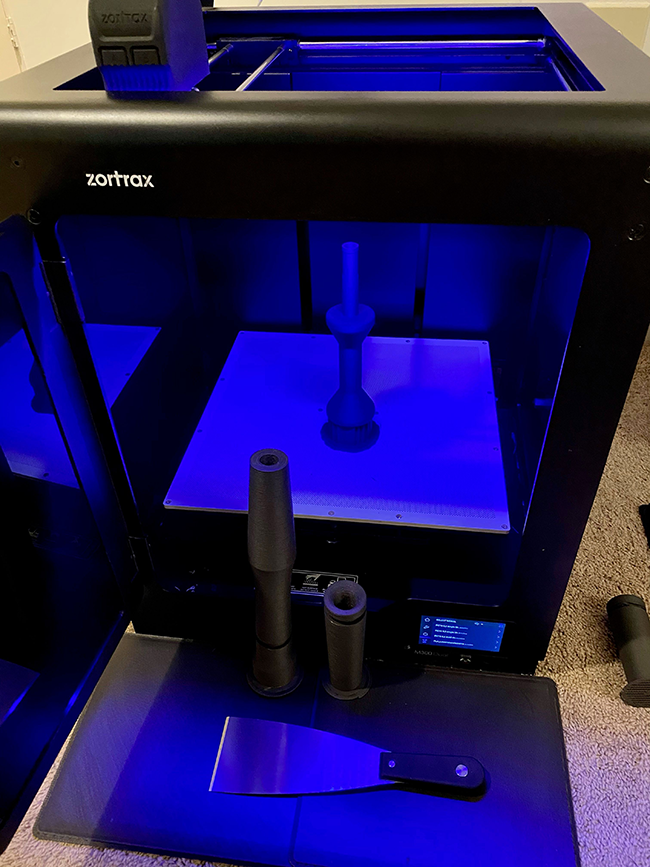
3D printed joints for the drones on bagpipes Ryan creates on special requests using Zortrax M300 Dual.
Nevertheless, what Ryan achieves thanks to 3D printing competes with professional analog instrument parts. “As a military musician, I am constantly performing in variable conditions. Having equipment that can provide stability and still allow me to create an exceptional musical product is vital to executing day to day performances. Pereira 3D gives me just that. Quality product, consistent sound, and the added bonus of reducing the weight of the clarinet is the icing on the cake.” – says Ashley Oliveto, U.S. Navy Band Clarinetist, one of Ryan’s clients.
Fully 3D Printed Clarinet Plans
Ryan doesn’t stop to develop his skills both in music and 3D printing. He’s currently following his academic career path of Musical Arts in the United States. He performs regularly with the clarinet he customizes himself. In the video below, Ryan performs in front of symphony orchestra in Boston with the piece “II Concerto” by Oscar Navarro. He uses a clarinet barrel, bell, and ligature all made with his Zortrax 3D printers during this performance.
And as for the next step, he’s planned to 3D print an entire clarinet: “I’ve made significant progress since 2020 and plan to hopefully release the first 3d-printed production clarinet within the next year.” Zortrax will be the brand to rely on for this task.
Learn more about Z-ABS and Z-HIPS 3D printing filaments used in this case on our webpage: Z-ABS and Z-HIPS.