Industrial 3D Printing at an Automotive Manufacturing Plant – RM Motors
Another example which shows how 3D printing can be employed at an automotive plant comes from RM Motors, a Polish manufacturer of cars’ exhaust systems. By implementing an industrial 3D printer in their production hall, the company was able to customize other specialized machines with 3D printed models. The roll press, which is used for stamping thermal insulation on a daily basis by RM Motors engineers, has to be adjusted to produce specific shapes of the insulation with a die and a stamp. That’s why, instead of having those components CNC-milled, which is expensive and time-consuming, the engineers simply modeled and 3D printed them. Having two Zortrax Endureal industrial 3D printers in their workshop allows the team to obtain any shape that is required to fabricate their products. In this case, 3D printing in automotive translates into utility projects which can significantly facilitate the workflow of the whole production. 3D printers can effectively replace CNC machines in areas where geometries necessary for production must be delivered quickly and flexibly.

Zortrax Endureal 3D printers working in an automotive manufacturing plant - RM Motors.
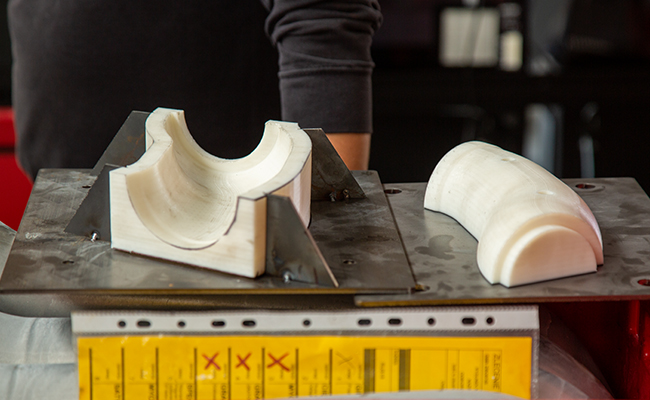
Custom 3D printed components for a roll press.
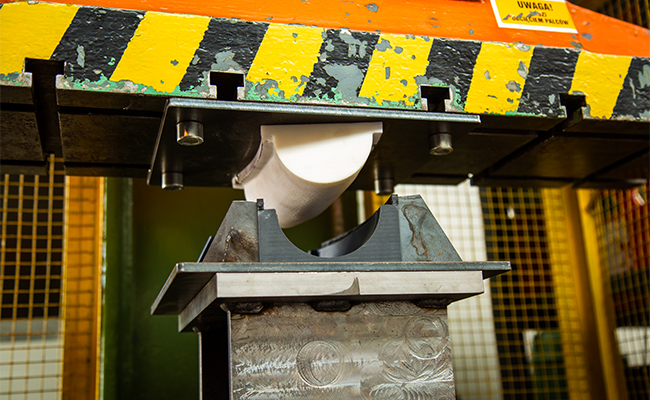
Custom 3D printed components for a roll press used for stamping thermal insulation in an automotive plant.
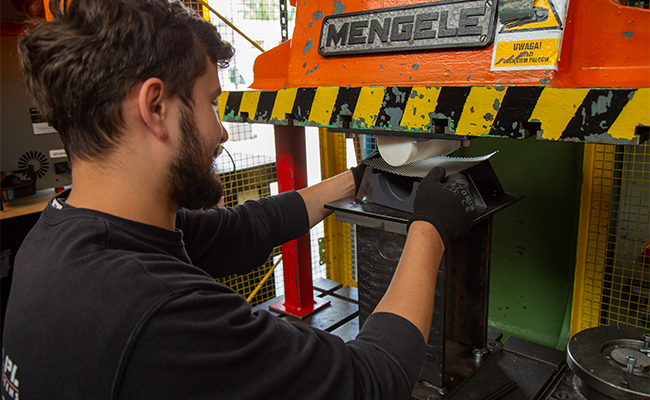
Automotive plant engineer working with a roll press equipped with 3D printed components.
Designing a Performance Motorbike by Vins Motors
At an earlier stage of vehicle production, that is designing, 3D printing is equally useful. Vins Motors, an Italian company founded by former Ferrari engineers, has designed a performance motorbike, called Duecinquanta, with a revolutionary 2-stroke engine and innovative approach to aerodynamics of the vehicle. With such a clear vision to produce an ultra-light motorbike with a carbon fiber chassis, in which each part had to perform at least two functions, the prototyping stage required a meticulous approach. All parts of both the chassis and the engine were designed in CAD software and 3D printed on Zortrax M300 out of filaments like ABS and HIPS. Vincenzo Mattia, the person who stands behind the idea for the motorbike, admits that “a 3D printer in automotive offers a completely automated process which became a natural way of communicating design ideas.” Mattia’s company 3D printed enough parts to build an entire full-scale model of the motorbike, which they used as a pre-production display prototype at motorcycles’ fair.
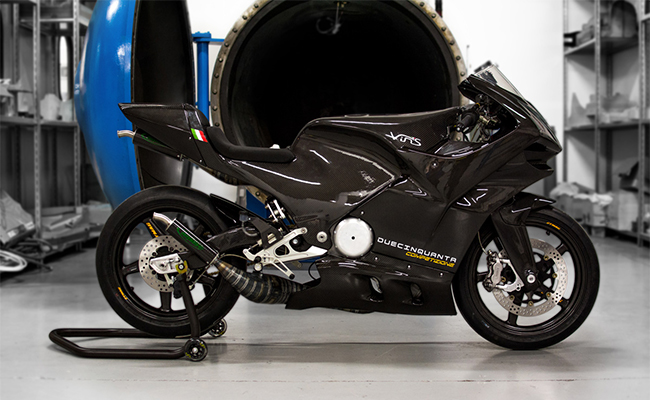
Duecinquanta motorbike produced thanks to 3D printed prototypes.
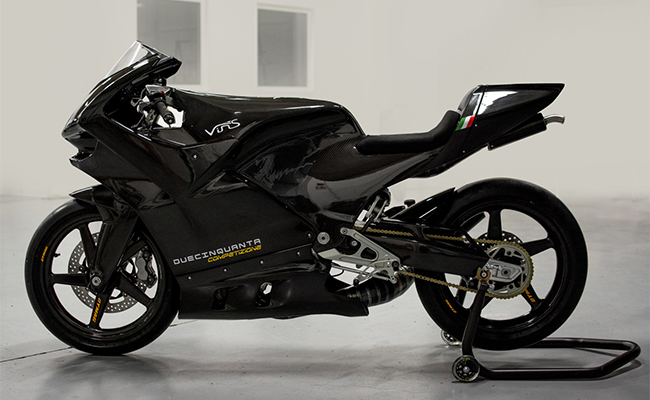
Duecinquanta motorbike with a 3D printed element that supports rear damper and improves aerodynamics.

3D printed end-use part for the motorbike's engine.
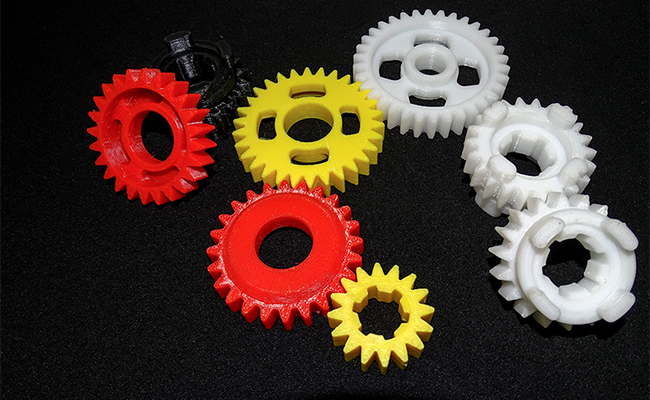
3D printed cogwheel prototypes for the motorbike's engine.
3D Printing in a Project of an Electric Motorbike by Falectra
Another example of how additive manufacturing technologies have enabled the production of a two-wheeled vehicle comes from Poland. Falectra is the first Polish electric motorbike brand founded by Piotr Krzyczkowski who decided to enter the e-mobility sector with his idea for a green and economical urban transportation solution. However, for his start-up company to gain funds from investors, he needed something more than a virtual project. To fit the tight budget, he decided to employ 3D printing as one of the manufacturing methods for the prototype. Around 10 parts of the vehicle were made with the use of Zortrax M200 Plus and M300 Plus — the front gate, rear fender, side covers, air inlet for charging the battery and a mounting part of the front lamp. In half a year, Krzyczkowski created a fully functional prototype, consisting of mostly 3D printed parts, and evaluated the bike’s potential for mass production, which is the key factor when developing a product: “The whole process cost almost seven times less and we were able to show the world a functioning motorcycle,” says Krzyczkowski.

Falectra electric motorbike with 3D printed air inlet.
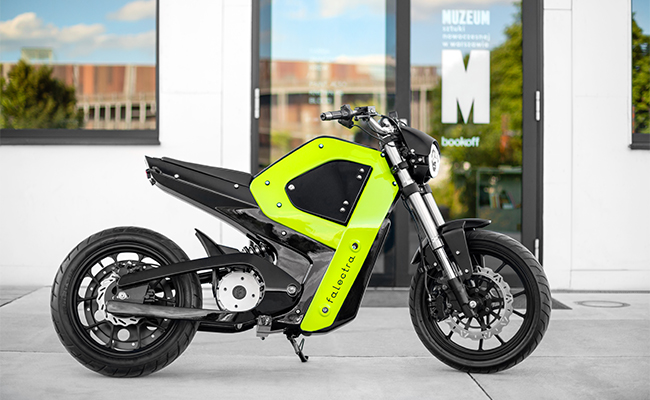
Falectra electric motorbike with 3D printed side covers.

Piotr Krzyczkowski working on a motorbike with 3D printed components.

3D printed housing for the front lamp in Falectra motorbike.
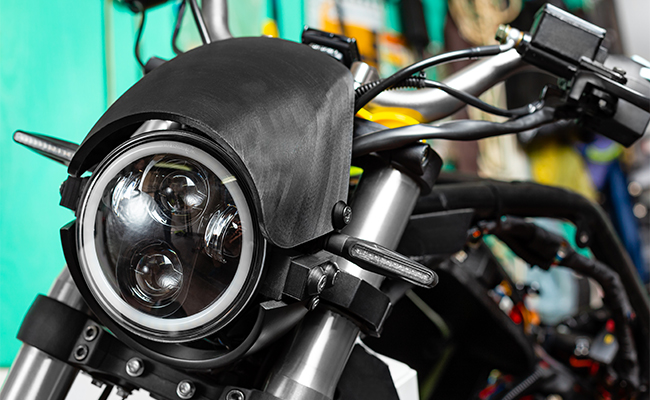
Motorbike front lamp housing 3D printed by Krzyczkowski from Falectra.
3D Printing Spare Parts for Classic Cars: ABcars and Alfa Project
Yet another business model in the automotive sector where 3D printers are an important tool is car restoration. Fabricating the parts that are damaged or missing in a vintage car usually involves working with old design documents, photographs, or any component that is left in a particular vehicle. In most cases, the additive manufacturing technologies make it possible to obtain elements which have been out of production for decades. One of the companies working in that field is ABcar Oldtimers from Poland. They used Zortrax Inkspire 3D printer to fabricate items of the steering wheel in a Ferrari 599 or elements of the dashboard in a vintage Mercedes Benz. Also, the M300 Plus and M200 3D printers helped the team restore a classic Porsche 911. “3D printing in automotive is incredibly helpful. It speeds up work and limits costs linked to prototyping individual parts. Additionally, elements 3D printed for cars work just fine and do not change their properties over time,” points out Bartłomiej Błaszczak, Design & Engineering Director at ABcar Oldtimers.
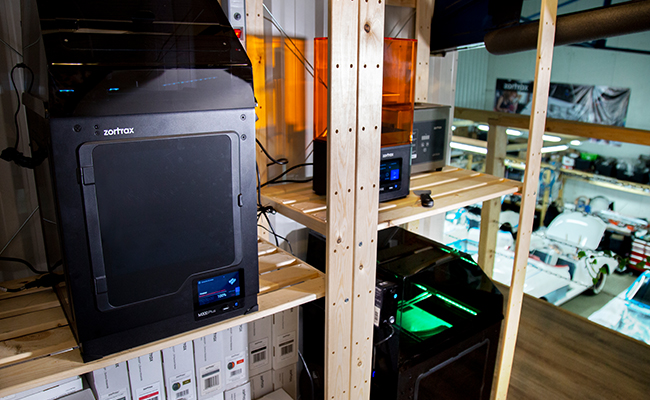
Zortrax 3D printers for automotive industry - Zortrax M200 Plus, Zortrax M300 Plus and Zortrax Inkspire.
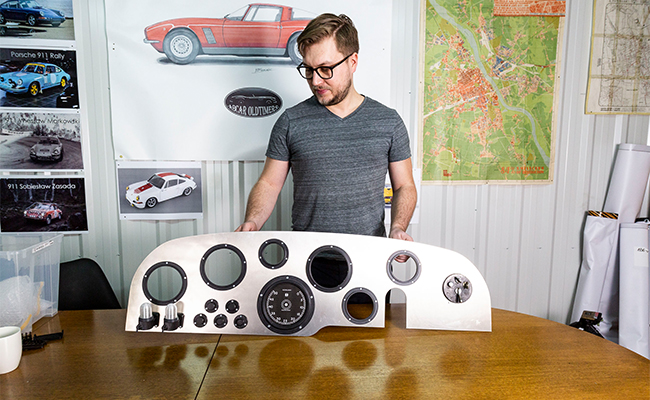
A designer working on 3D printed car components.
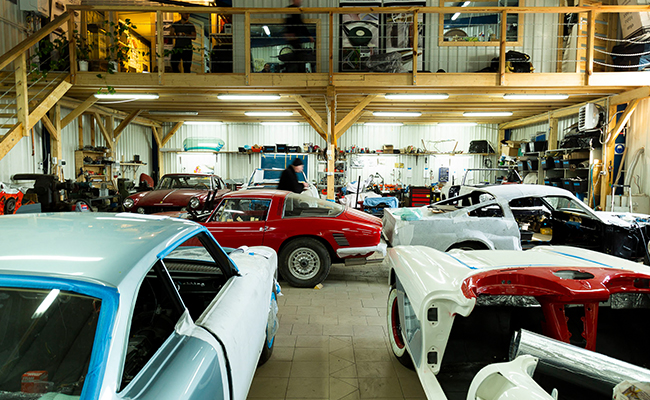
An automotive workshop which restores vintage cars.

3D printed steering wheel components.

An ABcar designer preparing a model to be 3D printed for a car.
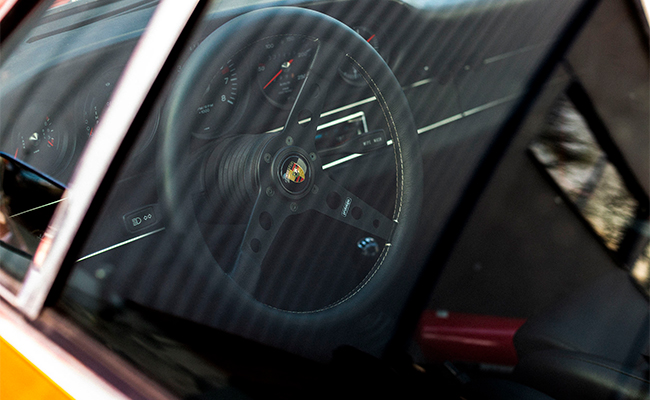
Elements 3D printed for a car in ABcar workshop.
Alfa Project is another company which has taken a similar approach with 3D printing in automotive. Through reverse engineering, they reproduce damaged and unavailable parts in classic Alfa Romeo cars. They 3D model and reproduce spoilers, bumpers, gear knobs, gearbox mechanism covers, mirror holders, and multiple elements of the dashboard, such as clock frames, air vents, AC control panels, or blanking plates. Since these plastic elements have been susceptible to damage through regular use, the team enhances each part’s design in CAD software. With features, such as strengthening ribs, Alfa Project continues the work on their Zortrax M300 Plus to 3D print high-quality ABS elements. “In printed plastic elements, ABS gives a satisfactory temperature resistance, and is adequately resistant to bending at the same time. It can be used in 3D models with fasteners or anchoring elements,” claims Mateusz Dziwisz from the team.
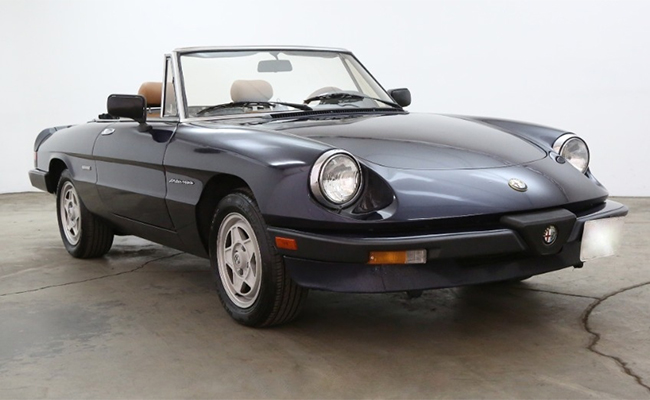
Alfa Romeo Spider renovated with 3D printed interior components.

Gear box cover 3D printed for a car.

Air vent panel 3D printed for a car.
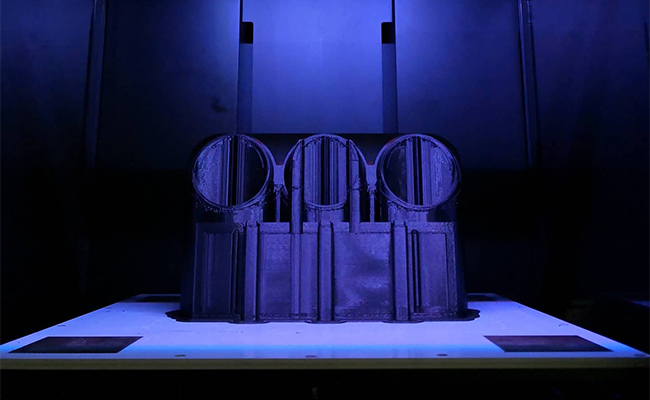
3D printed clock frames for an Alfa Romeo.
Customizing Cars with Durable 3D Printed Components – Indrė Zabielaitė
On the other end of the spectrum, there are hobbyists and true car enthusiasts who want to customize and upgrade their vehicles in a cost-efficient way. 3D printing is one of the technologies that perfectly fits car-tuning projects. Indrė Zabielaitė from the 3D Creative team upgraded her MINI Cooper with a used bumper coming from the MINI’s newer edition. However, the air intakes in the bumper that she ordered were damaged and unfit for being installed in her car. Therefore, with the access to a 3D scanner and a Zortrax M300 Plus 3D printer, Indrė produced new intakes, which after some post-processing, were fully functional and nicely fitted the entire bumper. The elements she 3D printed for a car are durable enough to be used in changing conditions: “I drive this car daily, even in winter and the 3D prints still look amazing. I’m truly satisfied with the quality,” Indrė sums up. 3D printing allowed Indrė to realize her vision for a car upgrade while maintaining low costs of the job.
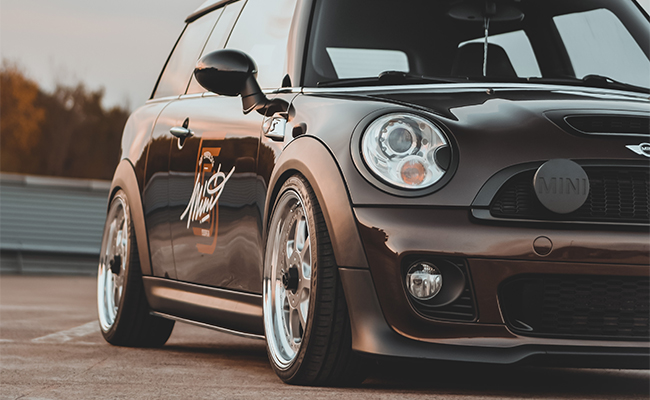
MINI Cooper S with 3D printed air intakes in the bumper.
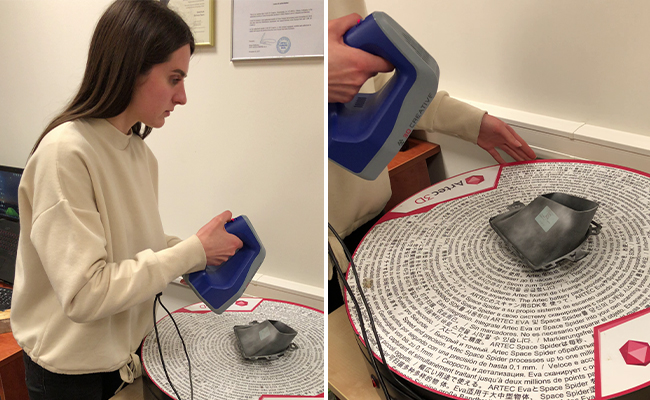
3D scanning of a car bumper element.

Indrė Zabielaitė in a 3D printing workshop.
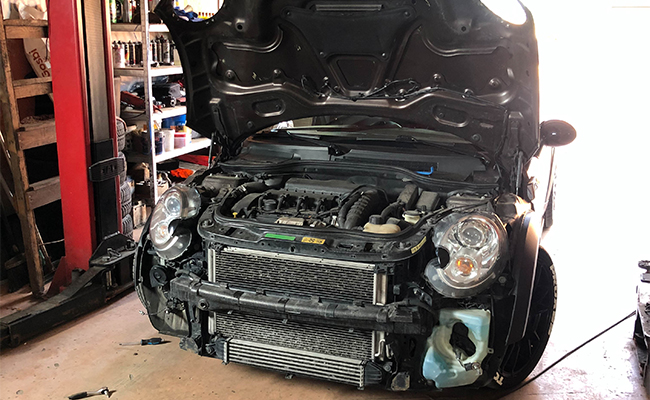
Customizing car with 3D printed components.
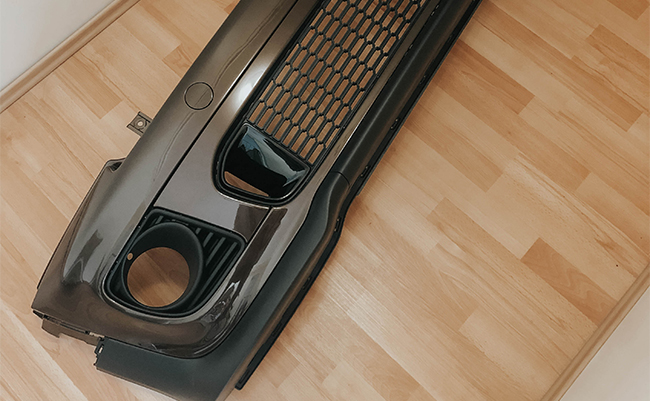
A car bumper with 3D printed air intakes.

3D printing in automotive - MINI Cooper S.
Contact us at sales@zortrax.com to check the possibilities of advanced 3D printing technologies using high-temperature and metal filaments in automotive sector. Our representatives can help you choose individually configured Zortrax 3D printing solutions that can include Zortrax Endureal or Zortrax M300 Dual.