3D Printing in Automotive: Economical Reproduction of a Vintage Scooter
Summary
- Falectra is a Polish e-mobility automotive company, taking advantage of 3D printing in their daily work.
- They have recently designed and produced a Be-e scooter, inspired by one of the 60's models, where most of the parts were 3D printed on Zortrax M200 Plus and Zortrax M300 Plus desktop 3D printers.
- The scooter has been noticed by motorization aficionados and there are currently 5 more items during production.
Falectra is an automotive company founded by Piotr Krzyczkowski, which is recognized for building the first Polish electric motorbike. The brand is also involved in vehicle reproduction, and has recently created a classic scooter called Be-e, based on the WFM M50, a Polish motorbike from the 1960s. 3D printing has played a significant part in Falectra’s business activity since the very beginning and it’s been no different for the Be-e project. The company has used Zortrax M200 Plus, Zortrax Inventure and Zortrax M300 Plus desktop 3D printers for the reproduction of this vintage scooter.
Designing 3D Parts for Automotive: a Classic Scooter Reconstruction
The idea for the Be-e scooter project emerged in parallel with the development of the Falectra e-motorbike, and during their collaboration with 911 Garage on the “Remastered” Porsche series, a variation on classic 911 models along with modern details. When work on the Falectra stalled, for reasons beyond the company’s control, the Be-e was put to the forefront. As there is the ever-growing fashion for restomods, Krzyczkowski knew such a project was going to grasp the attention of automotive enthusiasts. He also knew he wanted to base his new scooter on a WFM’s 60’s flagship model and use his favorite additive manufacturing technology for that purpose. The only issue that puzzled him was the project’s name. The designer wanted it to be associated with the original model, as well as reflect what the company specializes in. “Be-e” seemed to be a perfect choice: “Vespa is Latin for wasp, Bee is English for bee, and Be-e, in our case, is an extension of “Be electric,” Piotr Krzyczkowski, Falectra founder explains. Now, what exactly did the creative process look like in this case?
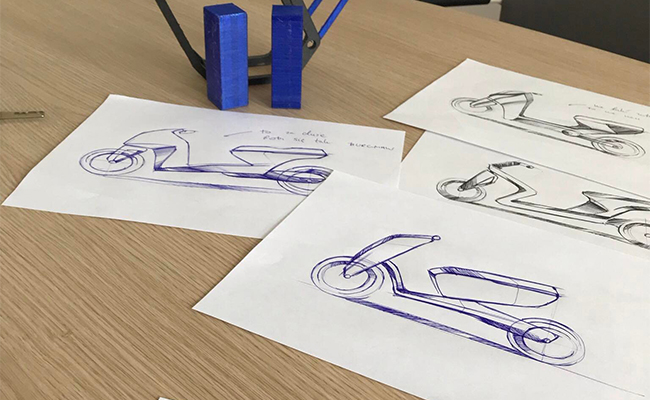
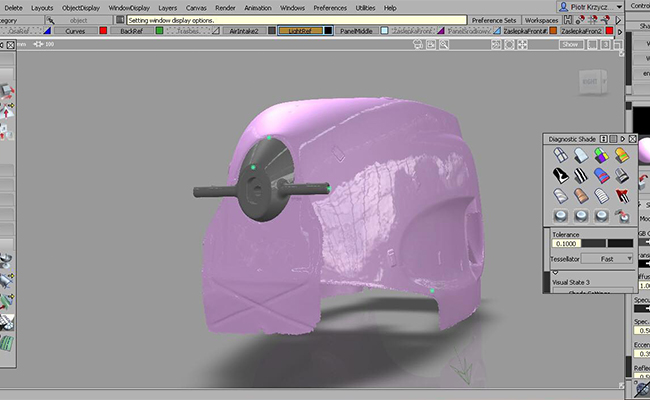
Workflow step 1: Sketching the Parts and Creating CAD Models
First, Piotr sketched the entire body of the scooter. “We decided to take inspiration from the lump, but simplify it – getting rid of elements that shot the overall form,” says Piotr Krzyczkowski. Then, after preparing the first sketches of the particular elements, the first visualizations began to emerge – the designer decided, e.g, on what details to implement, what is missing from the frame, or where to employ the functional items, such as rear lighting. The creator used Autodesk Alias CAD software.