3D Printer in R&D Department Support Lean Manufacturing
Lean manufacturing is considered one of the most efficient philosophies of production anywhere in the world. 3D printing technology and the introduction of affordable 3D printers such as the Zortrax M200 makes it possible to enhance the concept even more. 3D printers used in R&D departments result in time saving, higher efficiency and lower costs. Here’s how 3D printers support the processes.
Continuous improvement: 3D printing accelerates rapid prototyping
One of the basic applications of 3D printers is fast prototyping. Devices such as the Zortrax M200 3D printer let you 3D print out a complete item in a time period of between less than an hour and about a dozen hours. The time depends on the item’s size, precision of 3D printing and complexity of design. Nevertheless, it’s hours, not days, which is crucial for R&D experts who can thus conduct more tests and try out more concepts in a shorter time frame. Simultaneously such prototypes are cheap and experiments become affordable. As a result prototyping becomes faster and more efficient than when using other methods.
Increase of efficiency: 3D printing accelerates implementation
If 3D printing makes prototyping faster, it also influences the time needed t introduce the final product. This results in an overall increase in the company’s productivity.
Reacting to the needs of the client: 3D printing allows for better adjustments and greater flexibility
One of the key elements of the lean manufacturing philosophy is reacting to the needs of the client in a timely manner. 3D printing technology makes it possible to easily adjust elements in low volume production. Similar objects can be manufactured, but of different dimensions or with additional elements. The use of 3D printers allows for greater flexibility.
Increase in quality: 3D printing improves cohesion of production
Thanks to 3D printing it’s possible to conduct low-volume manufacturing with high precision and repetitiveness. This means that each 3d printed model will be of the same quality. With traditional manufacturing methods, whenever unique elements are needed, there’s no way to produce them. With 3D printing, however, you obtain precision which surpasses even typical mass production.
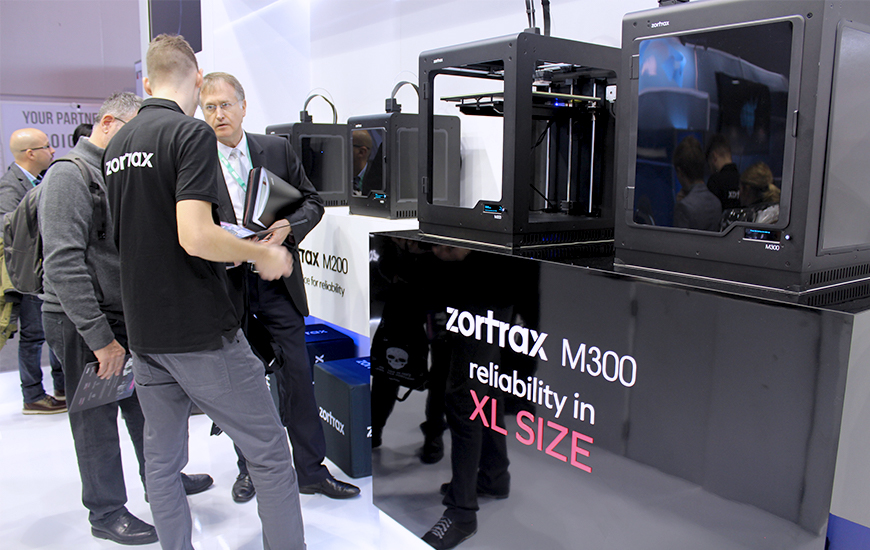
Reducing stock: 3D printing lowers costs.
3D printing technology makes it possible to lower costs in the prototyping phase as well as in the phase of utilizing 3D printing for production, for creating spare parts and for improvements in production. The best example comes from the use of Zortrax M200 3D printers in the R&D department of a French factory of Bosch. Within less than a year after the introduction of 3D printers the company saved upwards of €80,000. 3D printing makes it possible to limit the costs of stocking up on spare parts, the cost of spare parts themselves and to limit waste, as 3D printing involves a minimal amount of leftovers. Thanks to providing elements quickly 3D printing also reduces the time of inoperability thanks to providing necessary elements in a timely manner.
Saving time: 3D printing allows for local production
The innovativeness of 3D printing makes it possible to gain quick access to elements wherever you are. The technology is based on digital files and Zortrax M200 3D printers can be bought all over the world. Therefore, manufacturing specific elements with the use of 3D printers can take place anywhere. Moreover, clients can print spare parts on their own or even improve on the product through using their 3D printers or employing the service of local companies.
3D printing is more about changing the way a company works than just about improving on lean manufacturing. Thanks to 3D printers many actions can be performed faster, cheaper, simpler. This causes a company to build up its advantage, reduce waste and costs.